Level up your mass timber IQ & stay up-to-date on industry trends
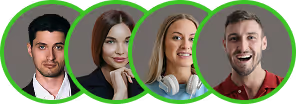
With the global data center market projected to reach $418 billion by 2030, driven by AI advancements and cloud services (Comarch), construction must adapt to new priorities, including speed, scalability, and environmental responsibility.
Mass timber products, like Mass Ply Panels (MPP), excel in these areas. Their prefabricated nature enables faster construction timelines, making them ideal for time-sensitive projects such as warehouses or data centers. Additionally, mass timber's inherent carbon storage capabilities align with the sustainability goals of these major industries. The material sequesters carbon and reduces CO₂ emissions, offering a competitive edge as companies seek greener building solutions to meet regulatory and environmental demands.
In warehouse construction, the rise of e-commerce—expected to account for 25% of total retail sales in the U.S. by 2025 (CBRE)—requires facilities that are not only functional but also environmentally conscious. Mass timber warehouses provide the durability and flexibility necessary to optimize storage while contributing to carbon reduction goals.
Mass timber’s versatility and scalability make it an ideal candidate for future industrial projects. As industries face growing pressure to build quickly, sustainably, and cost-effectively, adopting mass timber could redefine how we construct critical infrastructure.
Freres Engineered Wood has completed construction on a groundbreaking, nearly 60,000-square-foot mass timber warehouse at its Mill City facility, showcasing the potential of mass timber as a sustainable and cost-effective building material. This innovative project, constructed entirely of Mass Ply Panels (MPP), not only provides much-needed storage space for plywood inventory but also serves as a testament to the company's commitment to pushing the boundaries of wood construction.
"From the beginning, this project has been a case study to demonstrate that a mass timber warehouse is not only possible, but that it can compete in cost with traditional Pre-Engineered Metal Buildings (PEMB) and Concrete Tilt projects," says Kyle Freres , Vice President of Freres Wood
The warehouse, designed for Type V-B Construction, boasts an impressive array of features. It is 57,936 square feet with grid spacing of 40' x 48' and a height of 30’ to ridge, 25’ to purlin. The warehouse will have four truck loading stations and two tarping stations.
The environmental benefits of this project are significant. "We believe that this project met its goal of demonstrating that Mass Ply products are cost-competitive with both PEMB and concrete tilt construction," - Kyle Freres.
The warehouse utilizes 1,047 m3 (36,958 ft3) of wood, representing a carbon storage of 1,110 metric tons and an avoided CO2 emission of 429 metric tons. The total carbon benefit amounts to 1,539 metric tons of CO2, equivalent to taking 325 cars off the road for a year.
The construction process itself offered valuable insights into the advantages of mass timber. The prefabricated nature of the mass timber components allowed for a remarkably fast erection schedule of just six weeks, significantly shorter than a comparable concrete tilt project.
CD Redding, the general contractor for the project, highlighted the time savings: "Our erection schedule of 6 weeks was approximately 3 months shorter than that of a concrete tilt project, because all of the wall panels were constructed prior to the slab being poured. This is not possible with concrete tilt, which requires the slab to be complete so that the walls can be poured on the slab." - CD Redding Team
The design choices also addressed practical considerations. The bay spacing, set at 36 ft. by 48 ft., was determined to optimize storage efficiency for plywood units. Additionally, a pull-through bay for truck loading was incorporated to enhance traffic flow.
Beyond functionality, the warehouse exhibits an inherent aesthetic appeal attributed to its exposed wood structure.
"Yes, we are biased, but we don’t believe that a PEMB or a concrete tilt building provides an environment that is as comfortable or enjoyable to work in as wood," Freres states. "The wood on the interior is open for all to see. Our employees have commented that the building feels warm even though it is an unheated space," - Kyle Freres.
The project aligns with Freres Engineered Wood's commitment to sustainability. The company emphasizes the use of small diameter timber (9-10 inches in diameter) in their mass timber and cross-laminated timber products, contributing to responsible forest management practices and reducing the risk of wildfires.
The all-mass timber warehouse serves as a compelling model for future sustainable construction projects. Its successful implementation demonstrates the viability and benefits of mass timber as a primary building material, offering a compelling alternative to traditional construction methods. Freres Engineered Wood encourages those considering new industrial spaces, data centers, or warehouses to explore the possibilities of building with wood.
Freres Engineered Wood's innovative warehouse project stands as a beacon of progress in the construction industry, highlighting the potential of mass timber to create sustainable, efficient, and aesthetically pleasing buildings.
This is a partial list of all the individuals and organizations contributing to the Freres Engineered Wood Warehouse project. In the comments section, please let us know if you contributed in any way.
Lead mass timber projects with confidence — and leave delays, redesigns, and budget blowups behind.
✅ Solve early-stage design, sourcing, insurance, permitting, code & cost hurdles before they derail your project.
✅ Find technical answers on design, detailing, procurement, embodied carbon ROI, hybrid systems & more.
✅ Build relationships with developers, GCs, architects, and engineers shaping mass timber’s future.
Get your ticket— and get the insights, skills, and network to deliver mass timber projects successfully.