.avif)
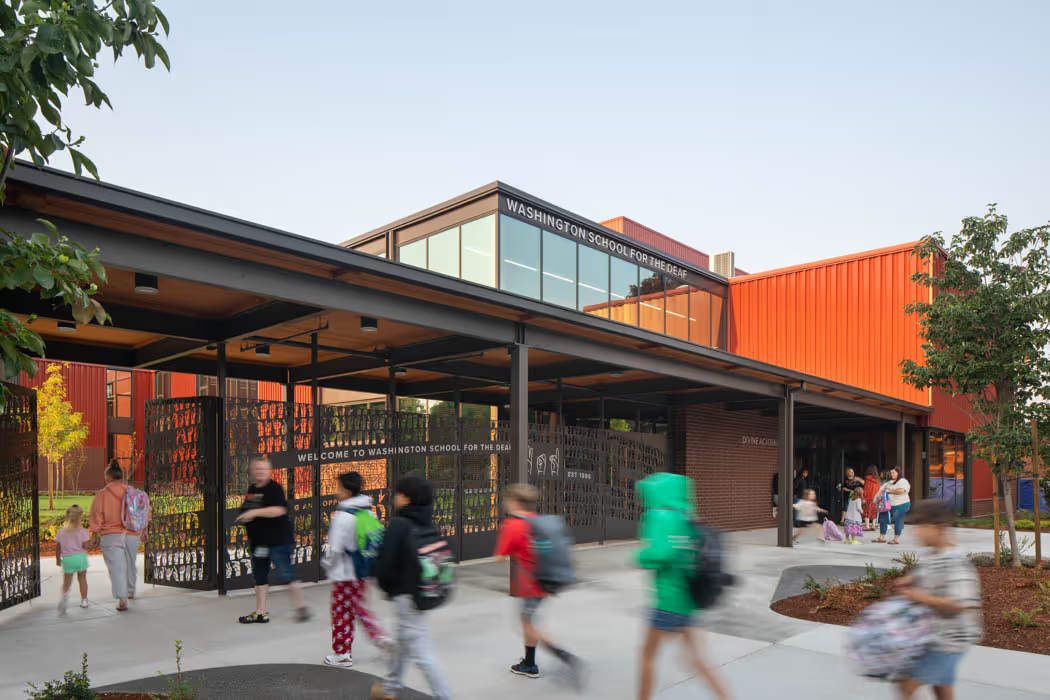
.avif)
Spotlight your incredible mass timber projects
We write and share compelling articles about innovative mass timber buildings—so more people can see them, learn from them, and get inspired to build with wood.
Simple process. Big reach.
We do the research, connect with your team, and write the story. Once we get your insights, we publish and promote it across our network.
01
Fill out our form below with your latest mass timber project.
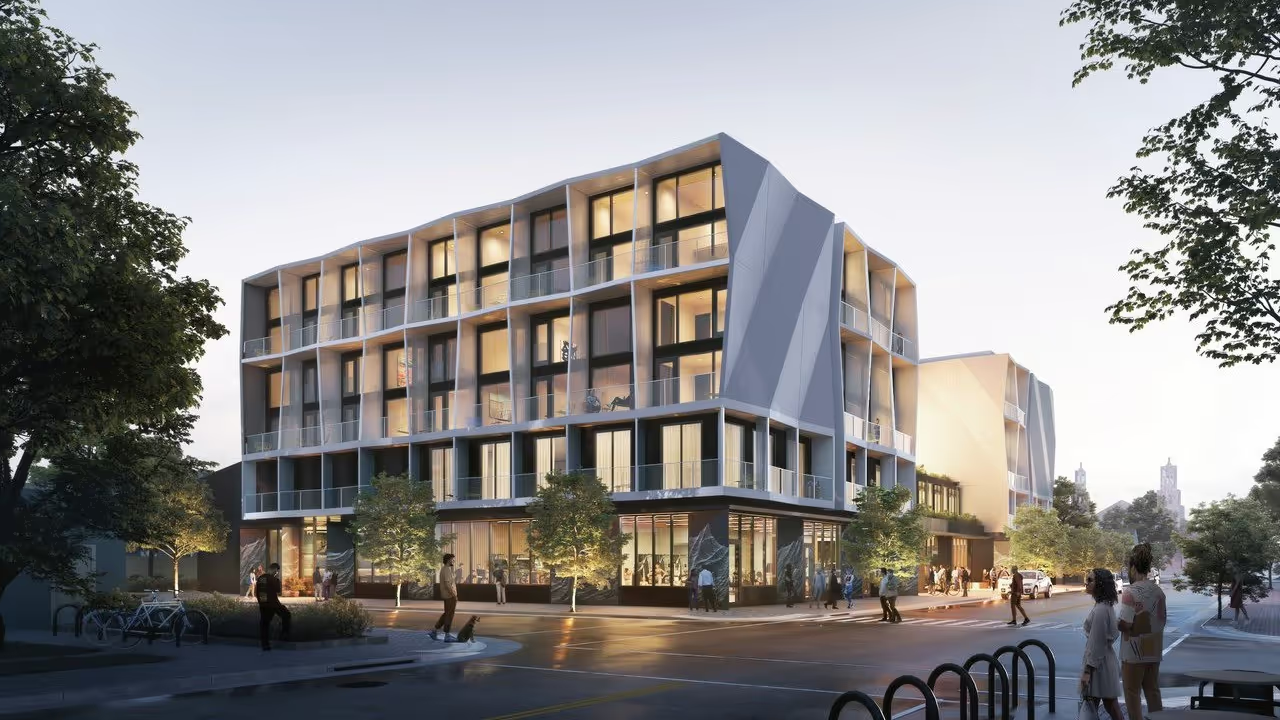
02
We gather info on your project and reach out to you.
.avif)
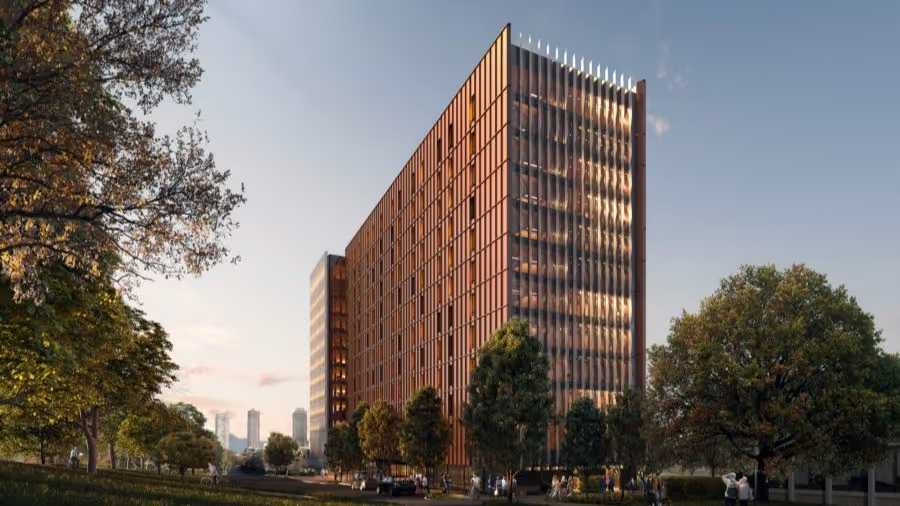
03
You provide your unique perspective via a short survey.
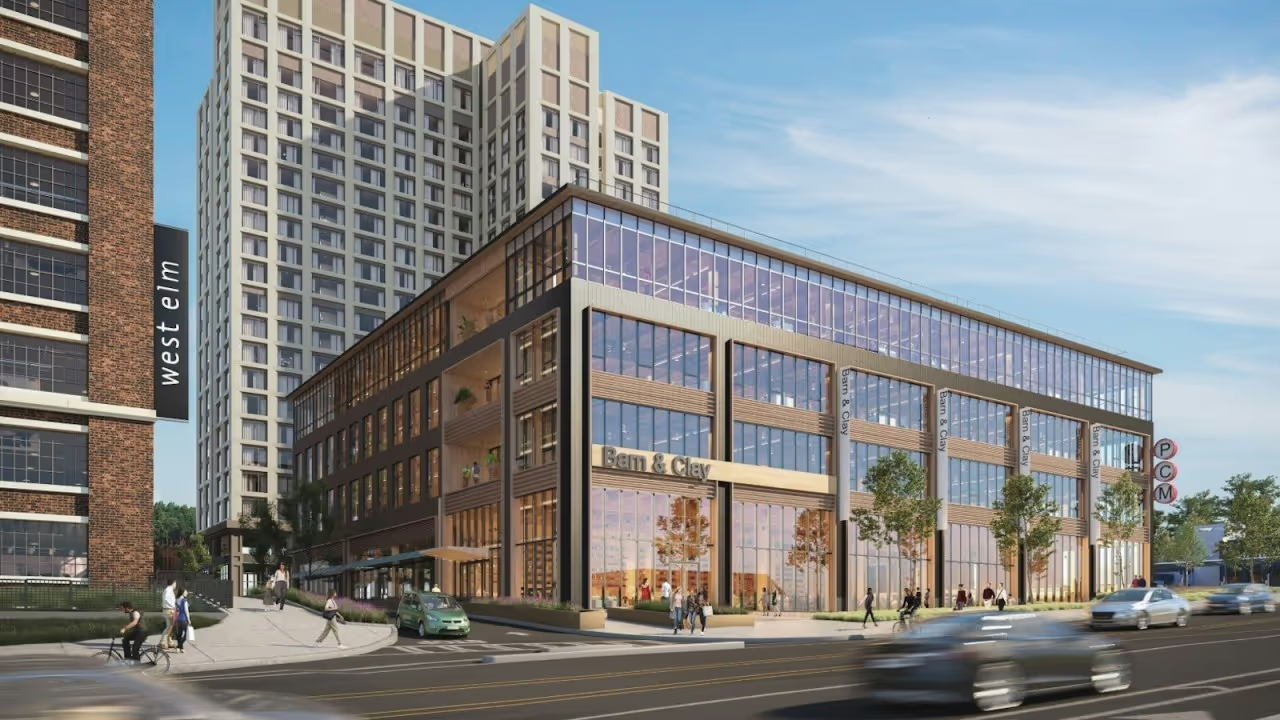
04
We write and publish the article to thousands of engaged readers.
Get featured in front of thousands of AEC professionals
Our articles are seen by the people who matter—developers, architects, engineers, and mass timber advocates.
Your project gets the attention it deserves—and helps grow the future of sustainable building.
Linkedin Followers
Newsletter subscribers
of annual website visitors
Built for AEC professionals
Read our latest building articles
Check out the latest Mass Timber buildings that we've featured in our community! Your building can be the next featured newsletter we send out.
5 Questions Architects Should Ask Their Timber Engineer
Written in collaboration with Brady Potts, Kirby Beegles, PE, SE & Martin/Martin, Inc.
Timber looks great in renderings. But getting it built to match your vision? That’s a different game.
More and more architects are reaching for mass timber, and for good reason. It’s natural. Renewable. Visually stunning. It checks the sustainability box and helps deliver the kind of warm, high-performance spaces clients love.
But somewhere between “we want mass timber” and “this got built,” things can start to fall apart. Floor systems get thicker than expected. Lateral systems eat into usable square footage. Connections look beautiful in renderings but fall apart in the shop drawings. Costs creep. Headroom disappears. And just like that, the warm, clean vision that sold the project starts to unravel.
This isn’t because mass timber doesn’t work. It’s because timber doesn’t work like steel or concrete. It has its own strengths. Its own limits. Its own sequencing logic and connection anatomy and fabrication workflows.
And unless your structural engineer has actually done this before, and really done it, your project may be headed for a hard lesson.
This article is for architects who are serious about mass timber. We’re breaking down the key systems to think through, the common traps to avoid, and the kinds of engineering decisions that separate smooth projects from painful ones. Along the way, we’ll share four real-world case studies, from a hybrid LVL arena roof to an all-wood office building, that show what it looks like when a structural team knows how to make timber work.
And at the end we have 5 Questions Every Architect Should Ask Their Timber Engineer.
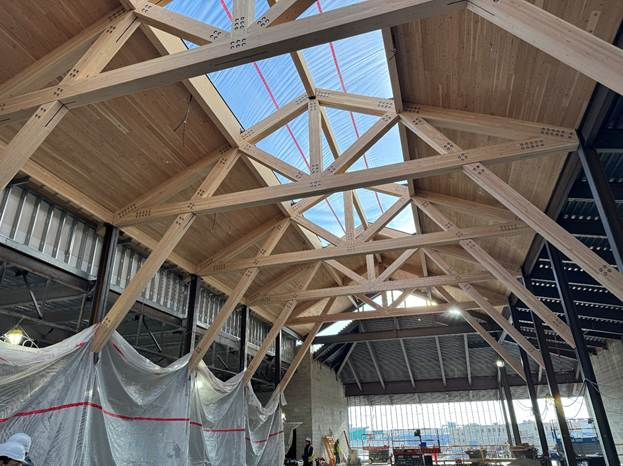
The Timber Trap (and How to Avoid It)
Big ideas are easy. Keeping them intact through detailing, coordination, and budgeting? That’s where timber projects rise or fall.
Maybe the renderings promised exposed wood ceilings and long, open spans. But then the floor assembly thickened—cutting into headroom and throwing off elevations. Or that clean timber expression got buried under last-minute steel hangers, knife plates, and bolted-on fixes no one budgeted for. Or the timber installer wasn’t looped in before MEP was finalized—and now there’s a glulam beam clashing with the main duct run.
It happens all the time. And not because the architecture was wrong, but because the engineering wasn’t ready.
Mass timber behaves differently than steel or concrete. It spans differently. Shrinks. Handles fire differently. Connects differently. And it demands a different level of precision because once it’s cut, it’s final.
When you’re working with an engineer who doesn’t know mass timber, problems like these can show up:
● Floor systems chew up ceiling height.
● Steel plates and bolts everywhere just to make the spans work.
● Bracing shows up where your clients don’t want to see it.
● Details that look clean in the model but don’t work for the install or budget.
● Cost surprises once the suppliers quote the panels & connections.
But with the right structural partner, someone who’s already engineered these systems, coordinated with suppliers, and seen projects to completion where these decisions play out, the picture changes:
● Your grid, spans, and panel sizes are coordinated early before they turn into cost and layout problems later.
● Lateral systems integrate cleanly without wrecking your layout.
● Service runs are coordinated early so your exposed timber stays clean.
● You spend less time fighting the structure and more time embracing it.
That’s the difference a timber-savvy engineer makes. They’re not just reviewing your drawings, they’re making sure the design actually gets built the way you envision it.
Proof in the Projects
Great mass timber buildings don’t happen by accident.
They demand precision across every phase from early design through construction. When the architect’s intent and the engineer’s detailing align early, structure supports design instead of limiting it.
These four projects show how that kind of partnership pays off on paper, on site, and in the finished space.
Kibbie Dome – University of Idaho
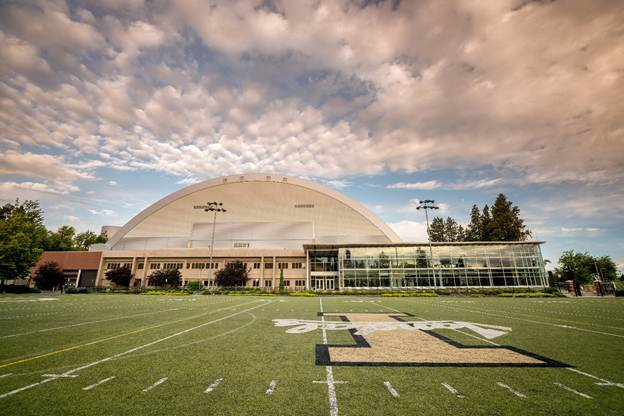
400 feet. Timber + Steel. Since 1975.
The Kibbie Dome made history. Completed in 1975, this arched barrel-vault roof still defines the Idaho campus today. Each timber truss spans about 400′, weighs around 23 tons and supports a roof covering 4.1 acres.
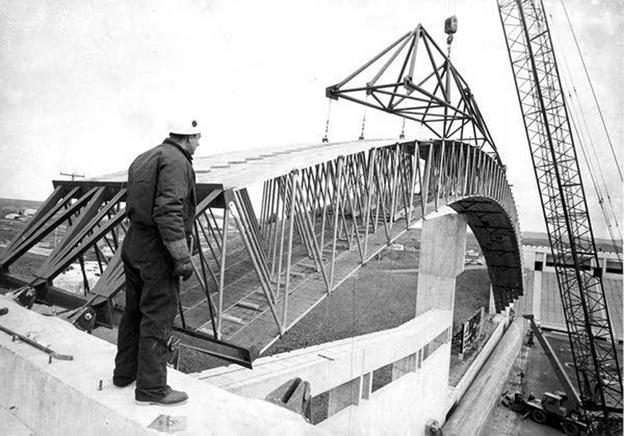
Martin/Martin, Inc’s structural team designed a hybrid LVL and steel truss system, combining engineered wood ribs with discreet steel tension elements optimized for long-span efficiency and high snow loads. They engineered a system that allowed the final arch to be erected just eight months after bid award; an unusually fast delivery for a project of this scale.
That rapid build and hybrid design earned the Dome the 1976 ASCE Structural Engineering Achievement Award.
What it proved:
● Timber can rival steel for long-span performance.
● Hybrid systems cut structural weight and complexity.
● Locally sourced wood made the structure sustainable long before mass timber was cool.
Jackson Hole Airport – Wyoming
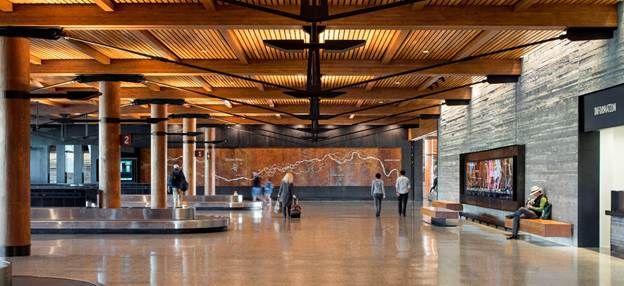
The warmth of wood with the resilience of steel.
Nestled in Grand Teton National Park, the Jackson Hole Airport terminal faced a mountain of constraints: an 18‑foot height limit, heavy snow loads, strict seismic codes, plus a big design ambition. But the result? A stunning, lodge-style space where exposed glulam trusses float over an airy ticketing hall, delivering warmth without sacrificing structural performance.
Martin/Martin worked closely with Gensler to engineer queen-post glulam trusses that spanned the ticketing hall column-free, yet stayed within vertical restrictions. Slender steel rod bottom chords and innovative timber-steel hybrid eccentrically braced frames quietly handle earthquake loads, meeting seismic performance flawlessly while enhancing the timber aesthetic.
What it proved:
● Performance needn’t compromise design.
● Long-span timber can be tailored to tight site constraints.
● Hybrid systems can meet seismic requirements without visual clutter.
HarborCenter – Buffalo, NY
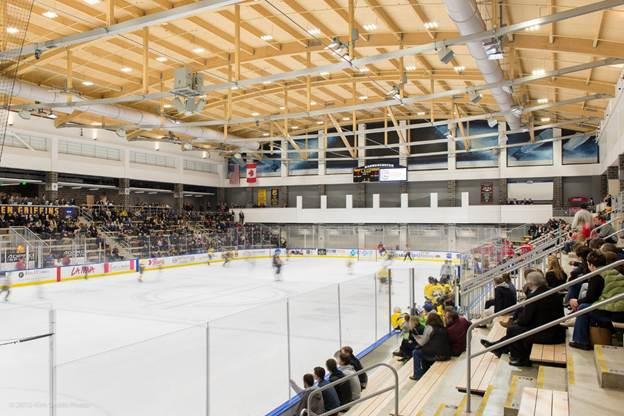
Hockey arena. Clear-span roof.
HarborCenter’s practice rink features a 140-foot clear span over the ice, supported by eight massive lenticular glulam-and-steel trusses spaced at 28.5 feet apart. The top chords are 31″×31″ glulam beams creating a warm, expressive ceiling while the bottom chords are slender 10″×10″ steel hollow sections, providing strength without visual bulk.
The best part? The hybrid roof system did not increase construction cost compared to a conventional all-steel frame.
What it proved:
● Hybrid glulam/steel trusses = clear spans + design appeal.
● Long-span timber systems are constructible and cost-competitive.
● You don’t have to choose between budget, performance, and visual quality.
Viega HQ – Denver Metro
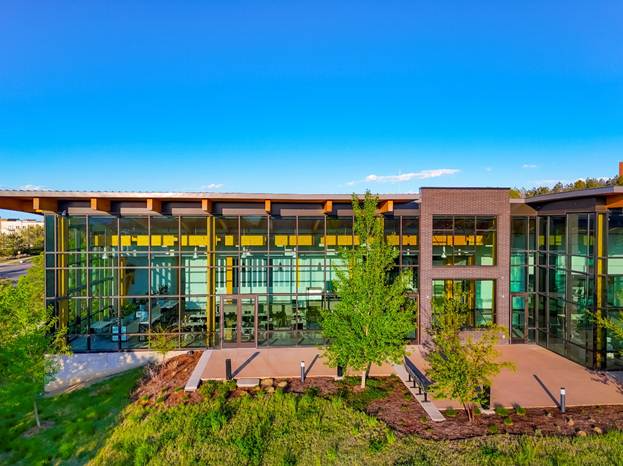
A milestone in Colorado’s mass timber movement.
Before local supply caught up, Martin/Martin partnered with Viega to import European CLT and glulam delivering one of Colorado’s first all-wood office campuses in Broomfield. This wasn’t about cladding a structure in timber. The structure became the architecture.
They engineered expressive curved rooflines, exposed glulam frames, and custom connection details that gave the building a handcrafted feel without compromising performance. Every decision had to meet code, coordinate with international suppliers, and hold up under real-world construction pressures. Martin/Martin didn’t just design it. They worked side by side with fabricators and detailers to make it buildable, cost-effective, and on schedule.
What it proved:
● Bold timber design doesn’t need a steel backup plan.
● Navigating global timber supply chains is part of the good structural engineer’s capabilities.
● When your Structural Engineer protects the vision, design intent stays intact.
Each of these projects could have gone sideways. Instead, they became proof points, because they had structural engineers who knew what to expect, how to solve it, and how to make timber perform as good as it looks.
5 Questions Every Architect Should Ask Their Timber Engineer
By the time CLT appears in your drawings, the most critical structural decisions have often already been made. That’s why successful mass timber projects don’t start with a material choice, they start with a coordinated system.
When the system isn’t right from the beginning, everything downstream gets harder: ceiling heights shrink, connections get messy, and MEP coordination turns into a headache.
So before you get too far into your design, Martin/Martin recommends you ask your structural engineer these five questions. Their answers will tell you if they’re ready to deliver a timber system that supports your vision instead of complicating it.
1. How are we handling fire and acoustics without eating floor height?
Architectural timber relies on exposed ceilings and open structure but fire ratings, STC, and IIC performance still matter. Too often, these are hidden behind drop ceilings or thick assemblies that consume vertical space. The right engineer layers tested fire and acoustic systems into slim, constructible details preserving both the design intent and clearances.
Martin/Martin’s work at Viega HQ proves it's possible to expose structure and meet performance without compromises.
2. Can this grid span cleanly without steel? If not, what’s the tradeoff?
Sometimes steel helps. But sometimes it can dilute the warmth of timber. Knowing when and why to integrate steel into a glulam or CLT system can make the difference between a buildable hybrid, or a tradeoff between budget and design.
At HarborCenter, Martin/Martin used glulam and steel together, leveraging each material where it performed best to span 140 feet with a clean expression.
3. What lateral system fits best (wood, steel, hybrid)? How does it shape your plan?
You don’t want to find out late in the design process that the lateral system will steal usable floor area. Whether it’s wood shear walls, ductile steel links, or concealed bracing, those systems shape your plan, your circulation, and your layout. Your engineer should be thinking about this on Day One.
Martin/Martin’s solution at Jackson Hole Airport used steel-timber hybrid eccentrically braced frames featuring steel links embedded within the timber system to meet performance requirements and integrate seamlessly into the architecture.
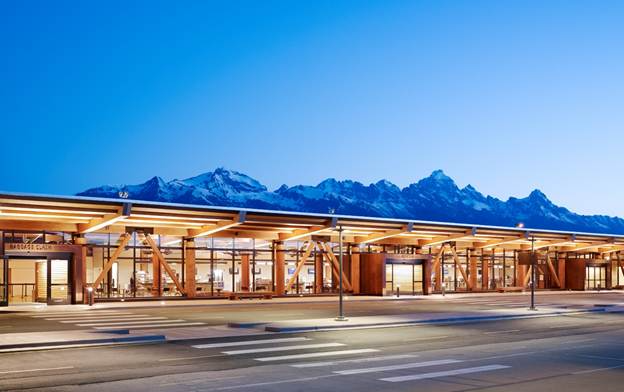
4. Will your beam/deck profiles crush headroom or overshadow proportions?
CLT and glulam systems aren’t always thin. Without careful system sizing, you’ll be forced to raise your floor-to-floor height, or lose ceiling height.
At Jackson Hole, the team maintained an 18-foot total height limit by engineering efficient glulam trusses that kept spans long and profiles lean.
5. Do we have multiple supplier options, and is the grid flexible to optimize for performance and cost?
Where your wood is coming from, and when, shapes everything from panel sizes and grid spacing, to lead times to connection tolerances. Your engineer should be asking: who’s supplying this, what’s their standard panel sizes, how’s that impact the grid, how is it fabricated, and what’s our install method?
Martin/Martin’s early involvement in the Viega HQ project meant they coordinated with European suppliers before domestic CLT was even common, solving potential issues before they ever hit the site.
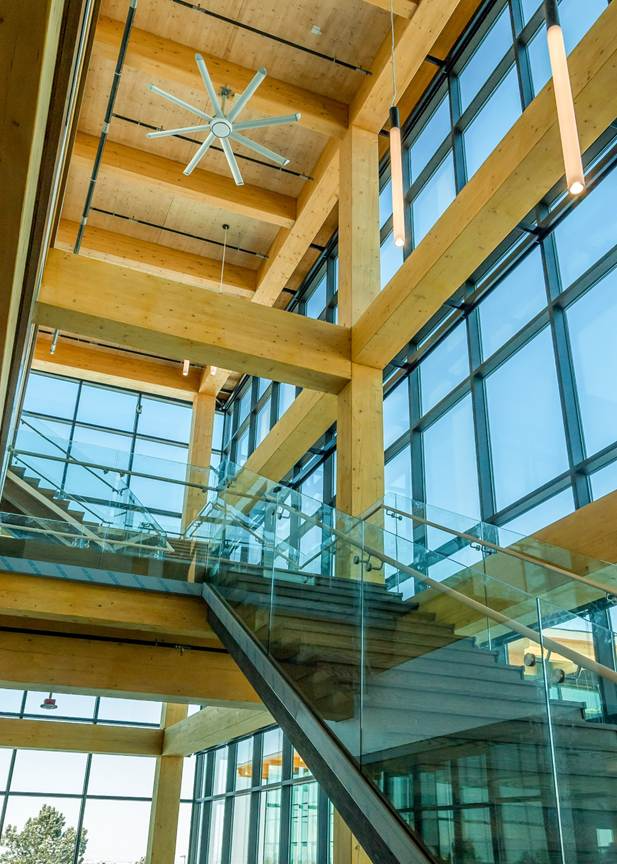
You don’t need to think like a structural engineer. But you do need one who thinks like a partner.
These questions aren’t gotchas, they’re invitations. Ask them early, ask them often, and make sure the person across the table has real answers backed by real projects.
Why Martin/Martin?
Martin/Martin’s mass‑timber portfolio isn’t just deep, it’s broad. They’ve worked on benchmark projects across categories; from long‑span glulam stadium roofs to full timber office campuses, proving timber can serve any building type. Their resume includes sports facilities, airports, arenas, office buildings, and more, with structural systems as varied as the projects themselves.
Their experience on unique, technically challenging projects translates into something every architect values: fewer surprises and more certainty. They’ve built expertise coordinating early with suppliers, GC’s, fabricators and installers refining systems through code review, and solving problems during construction.
Here’s what you get with Martin/Martin as your structural partner:
Real-world timber experience.
They’ve designed it, detailed it, and shepherded it through construction. They know what works, what doesn’t, and what to flag to keep timber in your project.
Fluency across systems.
CLT, glulam, hybrid steel-timber systems, ductile seismic links, they speak the language of materials, performance, and code while maintaining your design intent.
Supplier-connected.
They’ve worked with SmartLam North America™ , Timberlab , Nordic Structures , Mercer Mass Timber, Carpentry Plus, Inc. , Lam-Wood Systems, Inc. and international suppliers like binderholz group . That means they’re not guessing at what’s buildable, they’re coordinating with the teams that make these projects successful.
Architect-aligned.
They get what you’re trying to do. The beauty. The clarity. The grid. The clean ceiling. And they know how to preserve that while still delivering performance, cost control, and constructability.
Want to see what smart timber engineering looks like?
Connect with Kirby Beegles, PE, SE on LinkedIn, he’s the one you want in your corner when things get complex.
Even better? Meet Kirby and the Martin/Martin, Inc team in person at the Mass Timber Group Summit. You’ll get to see how they think, how they collaborate, and why they’re one of the most trusted names in timber engineering.
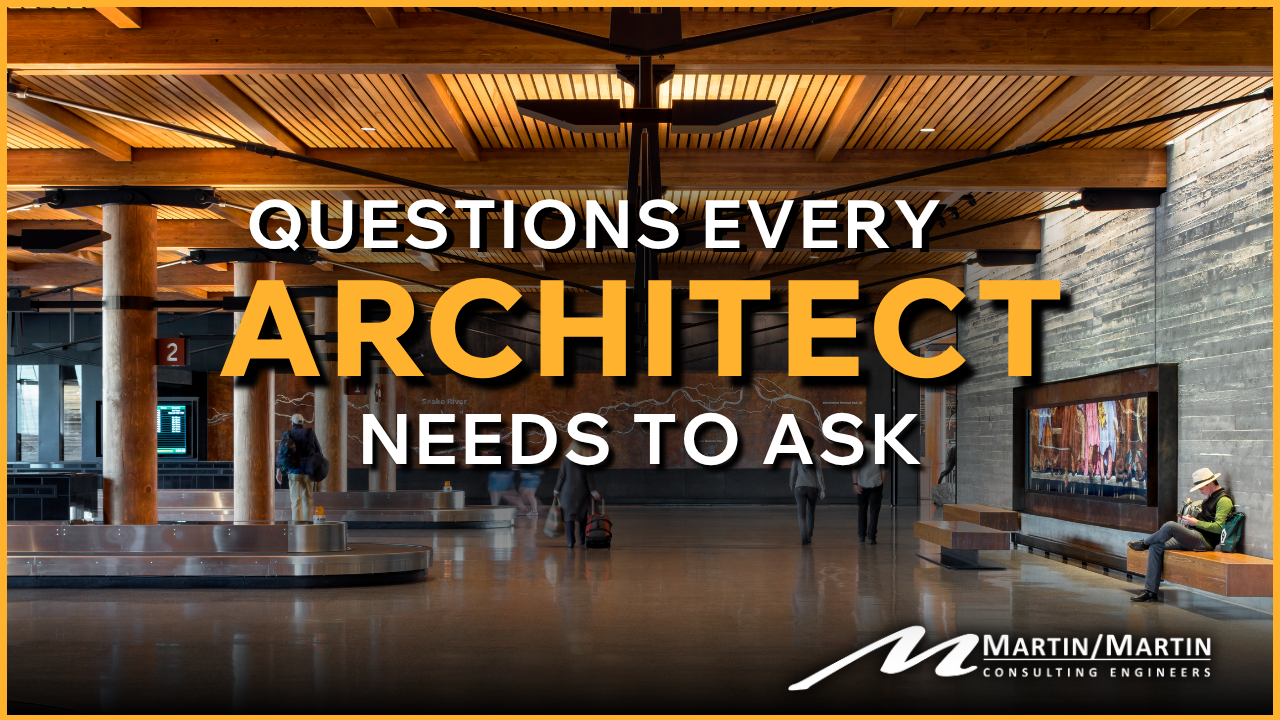
Responsive Arts & STEAM Academy: Pioneering Sustainable School Construction with Mass Timber
Have you ever wondered what it takes to build a school that not only educates but also inspires through its very fabric? In the dynamic landscape of modern education, school buildings are no longer just structures; they are learning environments, community hubs, and powerful statements about our commitment to the future.
The Responsive Arts & STEAM Academy (RASA) in Denver, Colorado, stands as a beacon in this evolution, redefining what’s possible in sustainable educational construction. This isn't merely a school; it's a living testament to innovation, collaboration, and a deep understanding of environmental stewardship.
RASA, a transformative project, is the first all-electric school for Denver Public Schools (DPS) and a pioneer in Colorado for its groundbreaking use of cross-laminated timber (CLT) construction. As DPS spearheads an ambitious climate action plan to reduce greenhouse gas emissions by 65% by 2030, RASA is at the forefront of this initiative.
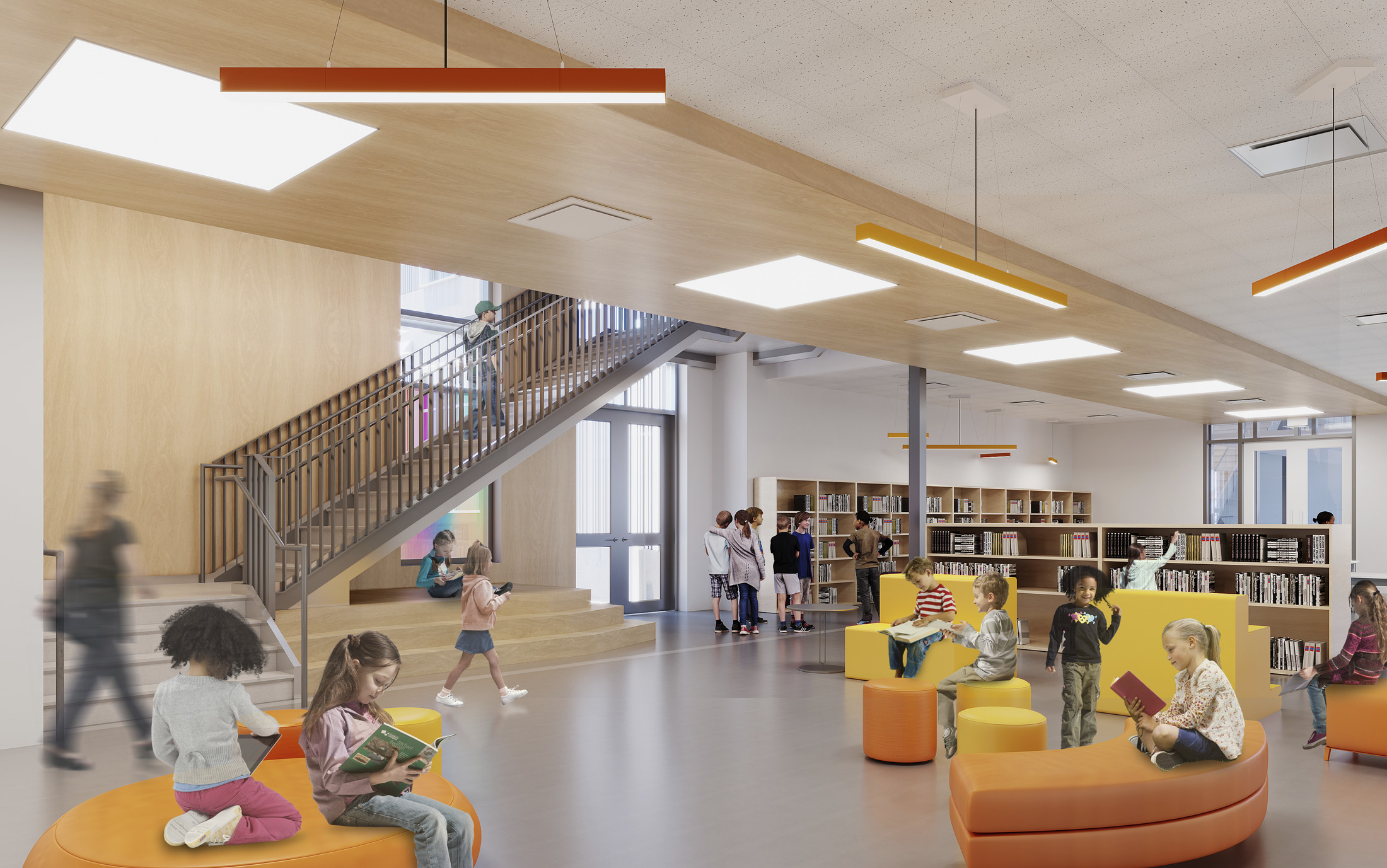
The Mass Timber Advantage
The journey to RASA’s innovative design wasn’t without its hurdles. Originally, the structural design for the school called for long-span steel joists. However, Swinerton, the general contractor, quickly identified a significant challenge: steel procurement came with a daunting lead time of more than nine months. This presented a critical risk to the project schedule.
Enter mass timber – a game-changer in the construction world. Swinerton, with its longstanding mass timber expertise, brought in Timberlab specialists to explore the feasibility of incorporating mass timber to mitigate these extended lead times.
"Swinerton was fortunate to come onto the OAC team at the concept phase," shares Jade Mercer, Project Executive at Swinerton. "This allowed us to have an impact on the design process by suggesting mass timber be considered as a solution to the long lead times for long span steel joists we were seeing."
The transition wasn't just about speed; it was also about proving cost-effectiveness. While wood was initially more expensive, Timberlab’s analysis revealed that mass timber could be procured much more quickly, shaving two months off the project schedule and significantly reducing general conditions costs. This strategic shift involved replacing long-span steel joists with glued laminated timber (glulam) and CLT decking. To further address long lead times for structural steel, precast concrete was also integrated into the exterior of the main building, contributing to the school’s LEED certification by enhancing thermal efficiency.
A Carbon-Conscious Campus
RASA isn't just embracing mass timber; it's setting a new benchmark for environmental responsibility. As the first all-electric school for DPS, it eliminates gas for heating, air conditioning, and even in its full-service kitchen, drastically reducing greenhouse gas emissions and improving indoor air quality.
Mass timber, inherently a carbon-negative product, played a pivotal role in this sustainable vision. With a volume of 300 cubic meters of wood products used, the project avoided greenhouse gas emissions of 103 metric tons of carbon dioxide, leading to a total potential carbon benefit of 368 metric tons of carbon dioxide. This deliberate design choice, coupled with sophisticated energy-efficient systems, has reduced the building’s energy use intensity by an impressive 50% compared to similar schools.
Designed to meet rigorous LEED standards, RASA incorporates a suite of green features, including electric vehicle charging stations, LED exterior lighting, low-water landscaping, artificial turf, low-flow water fixtures, and solar panels. Looking ahead, DPS aims to secure 70 to 80% of the school's power from carbon-neutral solar energy in its first year, with an ambitious goal to become the first carbon-neutral school in DPS, powered by 100% solar energy sources in the near future.
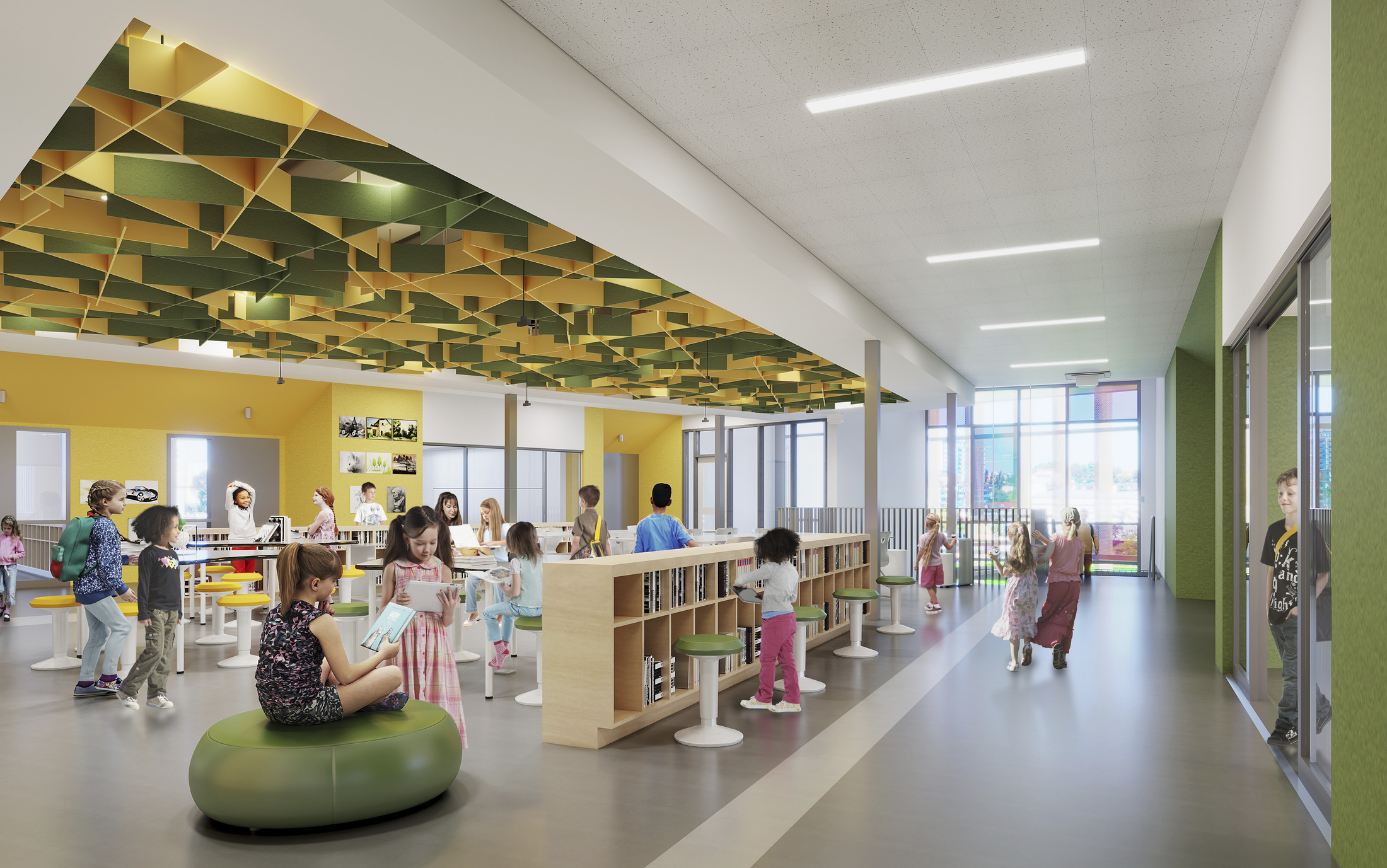
The Heart of the School
Beyond the technical marvels, what truly distinguishes RASA is the palpable feeling within its walls. "Without a doubt the mass timber component is my favorite," shares Jade Mercer. "The building is vibrant and feels alive. There is something about a mass timber school that feels very different from a traditional steel, concrete, and drywall covered building. I find myself stopping often to admire the gym and commons and it is where the students spend the most of their time as well."
The exposed glulam beams and CLT decking in the high-bay spaces, particularly the gymnasium and the commons/cafeteria, are more than structural elements; they are aesthetic statements, providing warmth and a unique tactile experience. As Molly Blakley, Senior Project Architect at DLR Group, describes, "In the early stages of design, there was a client-driven intent to make the building a welcoming space for the community, and the warmth and impact of wood in the commons space is a big part of that. Seeing the community and kids inhabit and enjoy this space is my favorite aspect."
Molly also notes the deliberate design philosophy: "What stood out to me was the intent from Denver Public Schools to manifest a school building that would exemplify their drive for innovation in education. There is flexibility, future-forward thinking, and student-centered ideology designed into every space." The final design features an exposed mass timber vaulted ceiling that gracefully spans an open two-story space, a true architectural highlight.
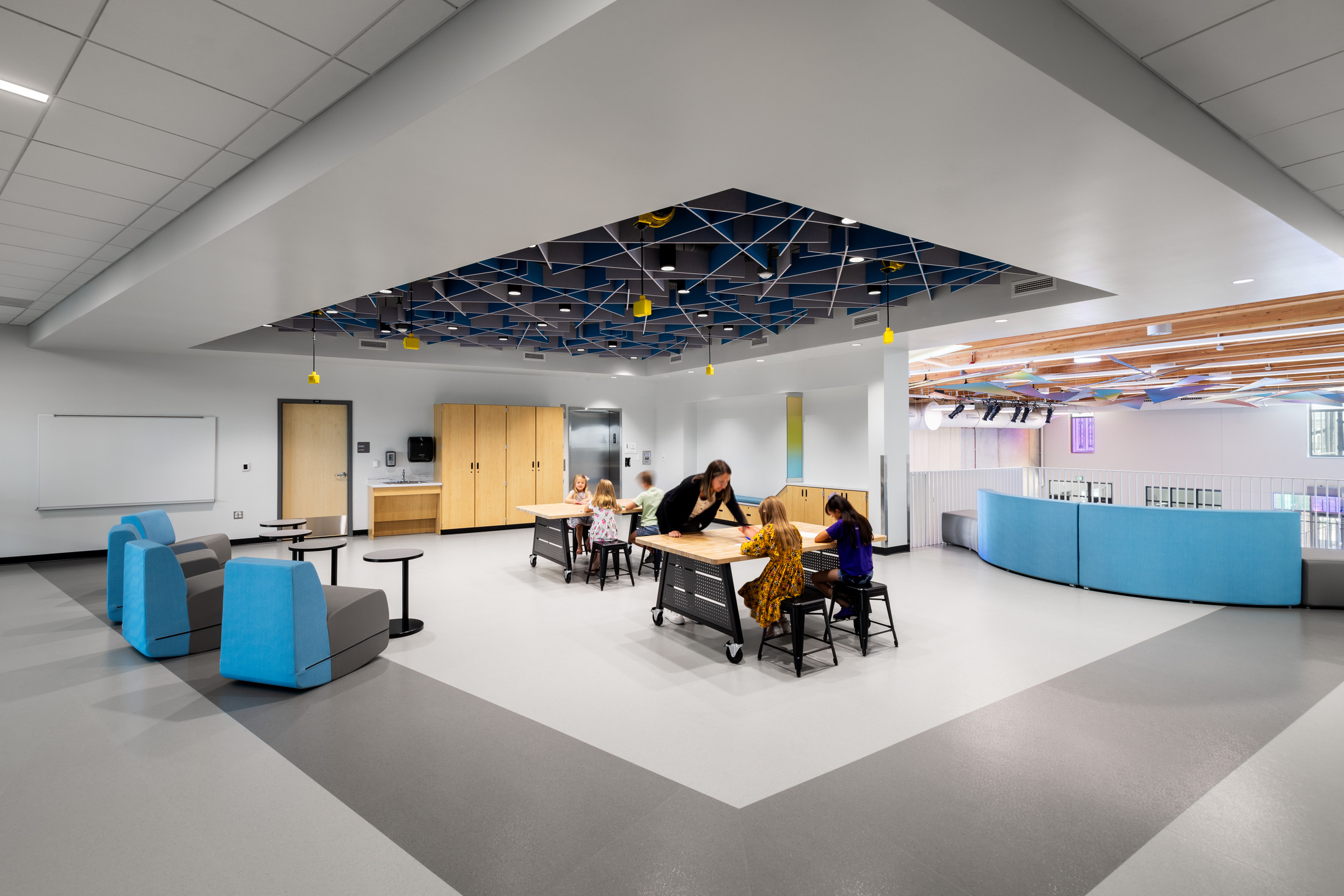
A Symphony of Collaboration and Expertise
The successful realization of RASA is a testament to extraordinary collaboration. Swinerton, serving as the general contractor, provided crucial design-assist services during preconstruction, offering invaluable insights on constructability, budget, and scheduling.
"There were challenges in how the precast and mass timber were detailed, and it took a lot of collaboration between DLR Group and Timberlab to make sure this was done correctly," explains Molly Blakley. "We could not have achieved this without the engagement of Swinerton early in the process who connected the team with Timberlab."
This intricate integration of diverse materials—precast, steel, and mass timber—required early and constant coordination between the design team, the district, and the contractor.
"Procurement timelines, detailing, and knowledge of construction tolerances all playing a part in how they come together," Molly adds.
DLR Group led the architectural design and management, also providing structural engineering and interior design services, with LT Engineering supporting structural engineering for specific elements. 360 Engineering, Inc., delivered mechanical and plumbing engineering expertise, instrumental in achieving the school's 100% electrification and energy efficiency goals. Swinerton's self-perform capabilities in areas like concrete slab-on-grade, drywall, framing, and firestopping further helped maintain schedule, maximize budget, and ensure high quality and safety.
RASA has already garnered recognition, receiving the A4LE Rocky Mountain Chapter 2022 Rockies Design Award and a 2025 PCI Design Awards Honorable Mention.
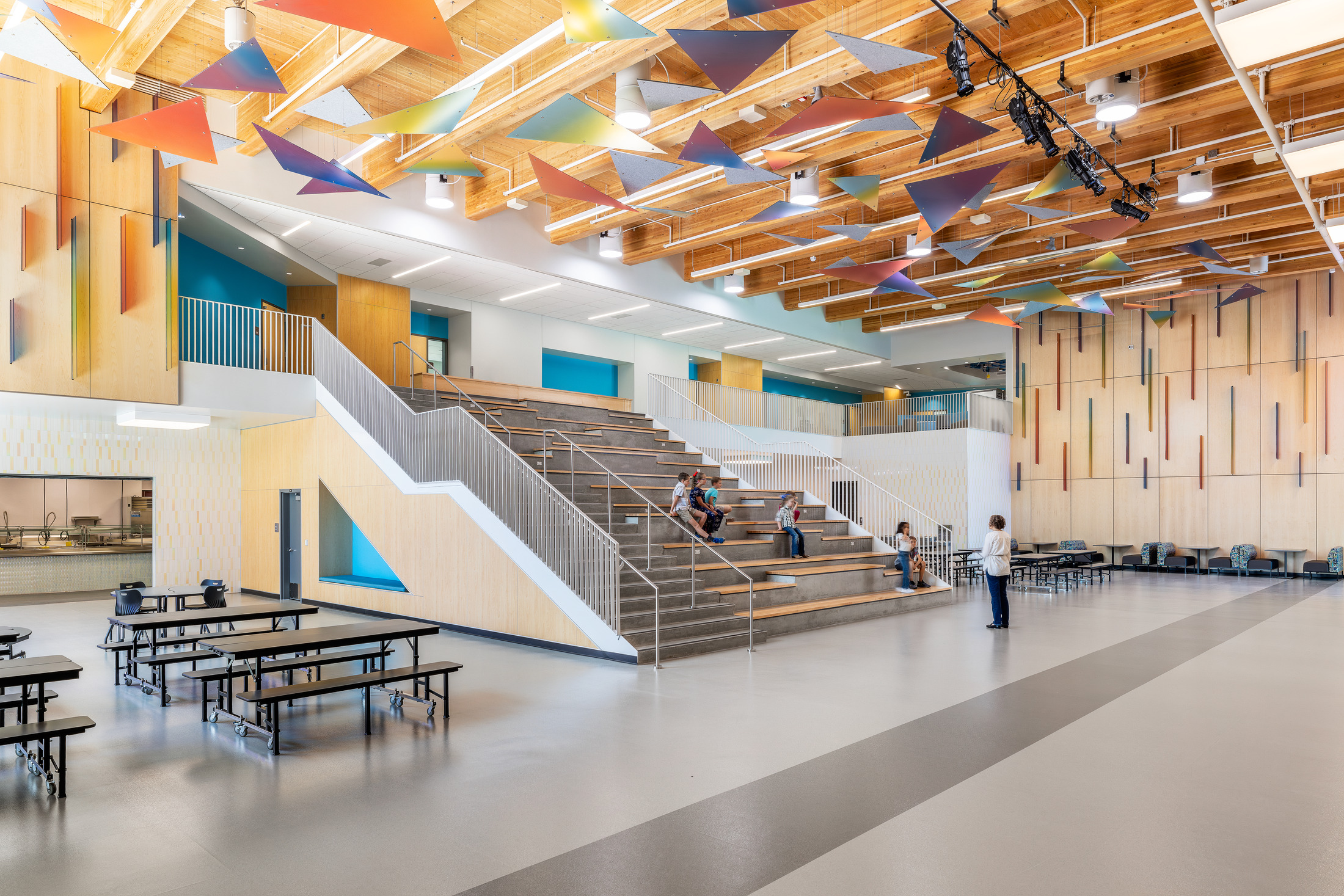
RASA: A Blueprint for a Brighter Tomorrow
The Responsive Arts & STEAM Academy embodies the future of educational infrastructure. It showcases how innovative construction methods, driven by environmental consciousness and collaborative spirit, can create spaces that are not only high-performing and sustainable but also deeply connected to the well-being and inspiration of their occupants. From overcoming procurement hurdles with intelligent material choices to embracing ambitious energy goals, RASA stands as a powerful model for future DPS facilities and indeed, for school districts nationwide. This project proves that with foresight, partnership, and a commitment to innovation, we can build educational environments that truly sustain ongoing learning – for both our students and our planet.
Contributing Teams and Individuals:
- Owner: Denver Public Schools (DPS)
- General Contractor: Swinerton
- Mass Timber Specialist: Timberlab
- Structural Engineering: LT Engineering (Stairs Only).
- Architect/Lead Structural/Interior Design: DLR Group
- Mechanical and Plumbing Engineering: 360 Engineering, Inc.
- Photographer Credit: The Unfound Door
- Photography is Courtesy of the DLR Group
FAQs about Responsive Arts & STEAM Academy:
- What makes RASA unique in terms of its construction materials? A: RASA is notable for being the first school in Colorado to utilize cross-laminated timber (CLT) construction, alongside glulam beams, particularly in exposed high-bay areas like the gymnasium and commons. It also integrated precast concrete for the exterior and some steel elements.
- How did the project team address challenges with long lead times for construction materials? A: Swinerton proactively suggested replacing long-span steel joists with mass timber (glulam and CLT) due to steel's nine-month lead time. This change, aided by Timberlab, reduced the schedule by two months and saved general conditions costs. Precast concrete was also used to mitigate steel procurement delays.
- What are RASA’s key sustainability achievements? A: RASA is the first all-electric school for DPS, eliminating gas use. It reduced its energy use intensity by 50% and leverages mass timber as a carbon-negative product, contributing to 368 metric tons of potential carbon benefit. It's designed to meet LEED standards and aims for 100% solar energy in the near future.
- What was the scope and timeline of the RASA project's phases? A: The project was divided into two phases. Phase 1 (84,385 sq ft) for PK-5 students was completed in July 2024 and opened in August 2024. Phase 2 (36,482 sq ft), a middle school addition, is scheduled for completion in August 2025, expanding RASA to a full PK-8 school.
- What did the project leaders enjoy most about working on RASA? A: Jade Mercer, Project Executive at Swinerton, loved the mass timber component, finding the building "vibrant and feels alive." Molly Blakley, Senior Project Architect at DLR Group, highlighted seeing the community and kids inhabit and enjoy the warm, impactful commons space as her favorite aspect.
.jpg)
From Pro Forma to Boarding Gate: Strategies for High-Stakes Mass Timber Projects
In Manitoba’s north, air travel isn’t optional—it’s life‑sustaining. Since 1960, Perimeter Aviation has connected 33 remote communities, two of which lack year‑round road access. When it came time to triple the size of their Winnipeg terminal at Richardson International Airport, the project team sought not just more square footage, but a more inclusive, human-centred experience. Enter mass timber: a structural backbone that stores carbon, accelerates construction, and introduces a sense of warmth often missing in airport design.
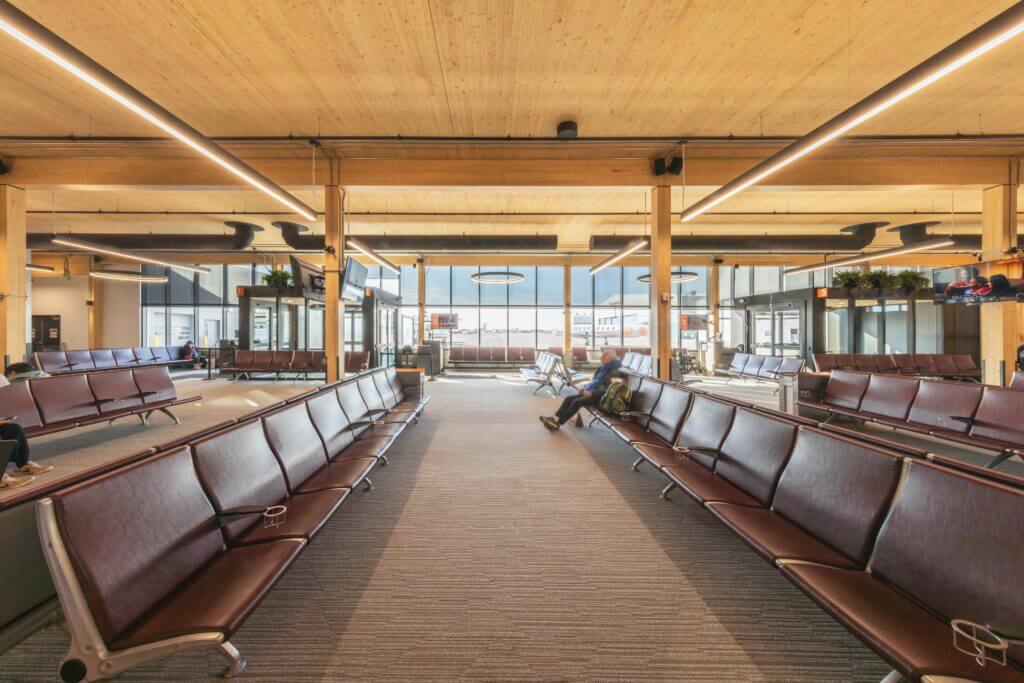
Making the Case for Mass Timber in Aviation
At first glance, timber and tarmac may seem at odds. But engineered wood products—specifically a 5‑ply CLT roof diaphragm paired with glulam post‑and‑beam framing—proved ideally suited for Perimeter’s needs. The numbers speak for themselves:
- 265 m³ of Forest Stewardship Council U.S. FSC‑certified mass timber
- 256,520 kg of CO₂ locked away—equivalent to removing 55 cars from the road for a year
- ±13,036 ft² of new mass‑timber structure within a ±21,743 ft² addition
That carbon‑storing capacity isn’t a footnote—it’s a headline benefit for airports aiming to reduce embodied emissions without sacrificing performance.
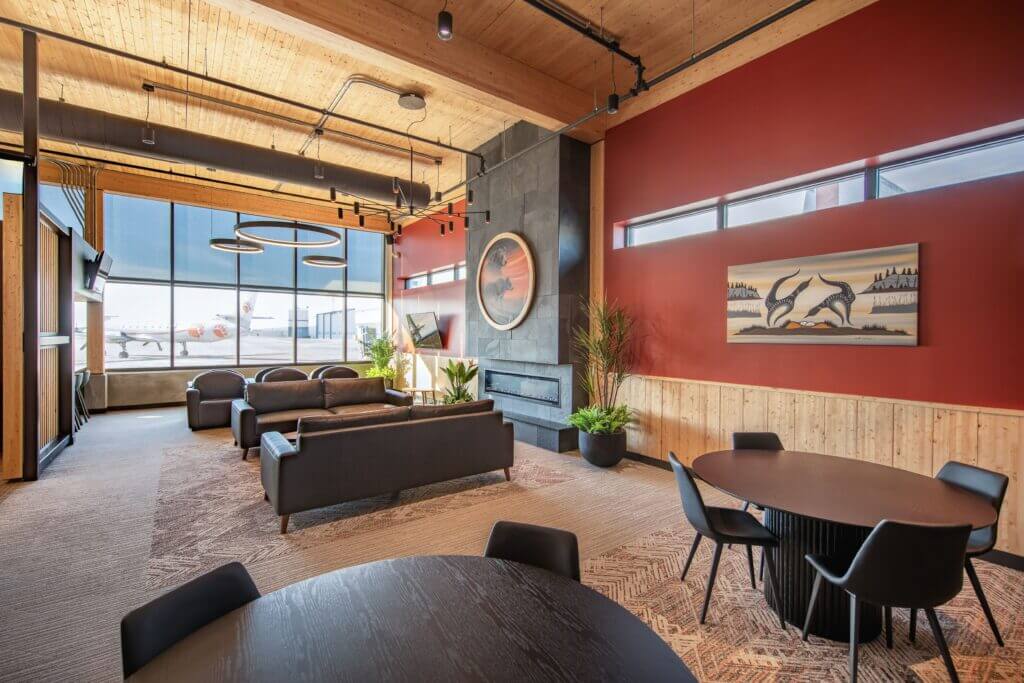
Timber as a Team Sport: Cornerstone’s Role
Mass timber demands more than just material—it requires choreography. That’s where Cornerstone Timberframes stepped in as the “orchestra conductor” for the timber scope.
Cornerstone handled all communication, design integration, and problem‑solving—keeping budget top of mind while squeezing maximum efficiency from every panel and beam. When MMP Architects requested a flush‑mount metal baseboard cap in common areas, Cornerstone collaborated on a recessed detail that aligned perfectly with corner protection. And when a reverse‑poured structural slab shifted sequencing on site, they re‑sequenced the CLT panels on the fly - twice - yet still hit the installation schedule.
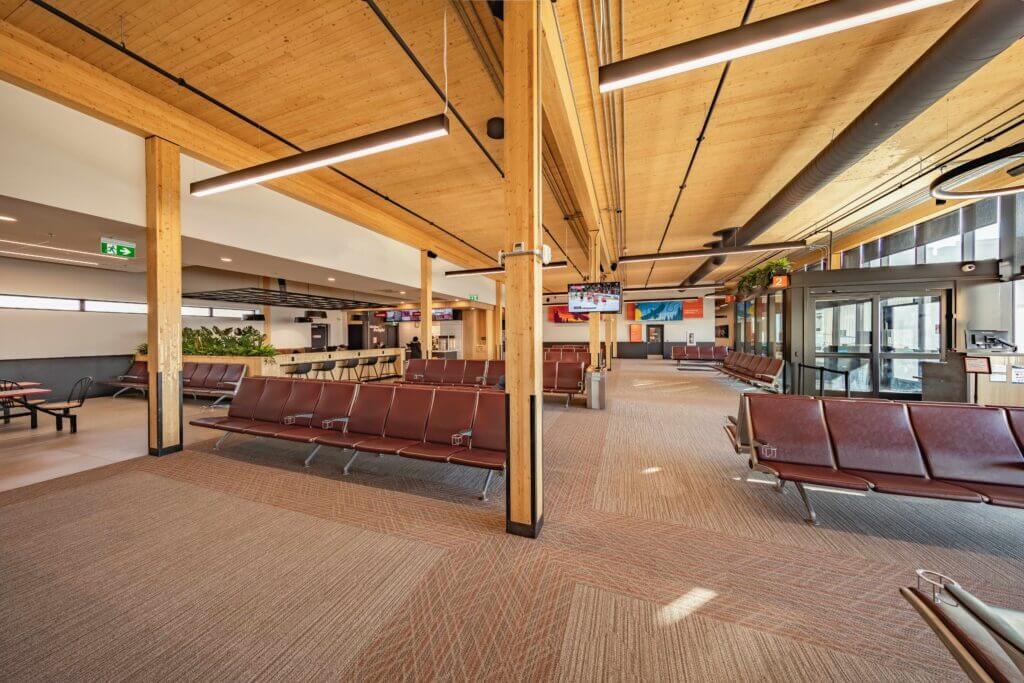
Designed with You in Mind
Step inside the new terminal and the timber speaks: exposed glulam columns, a warm CLT ceiling, and full‑height glazing along the apron side that floods the space with natural light. The result is a grounded, human‑scaled environment that caters to Indigenous travellers, families, and anyone seeking a calm transition from earth to sky.
Amenities include:
- Departures lounge for 250 passengers
- Children’s play area and elders’ lounge
- Enhanced accessibility features
- Expanded baggage handling and concessions
- Upgraded security screening
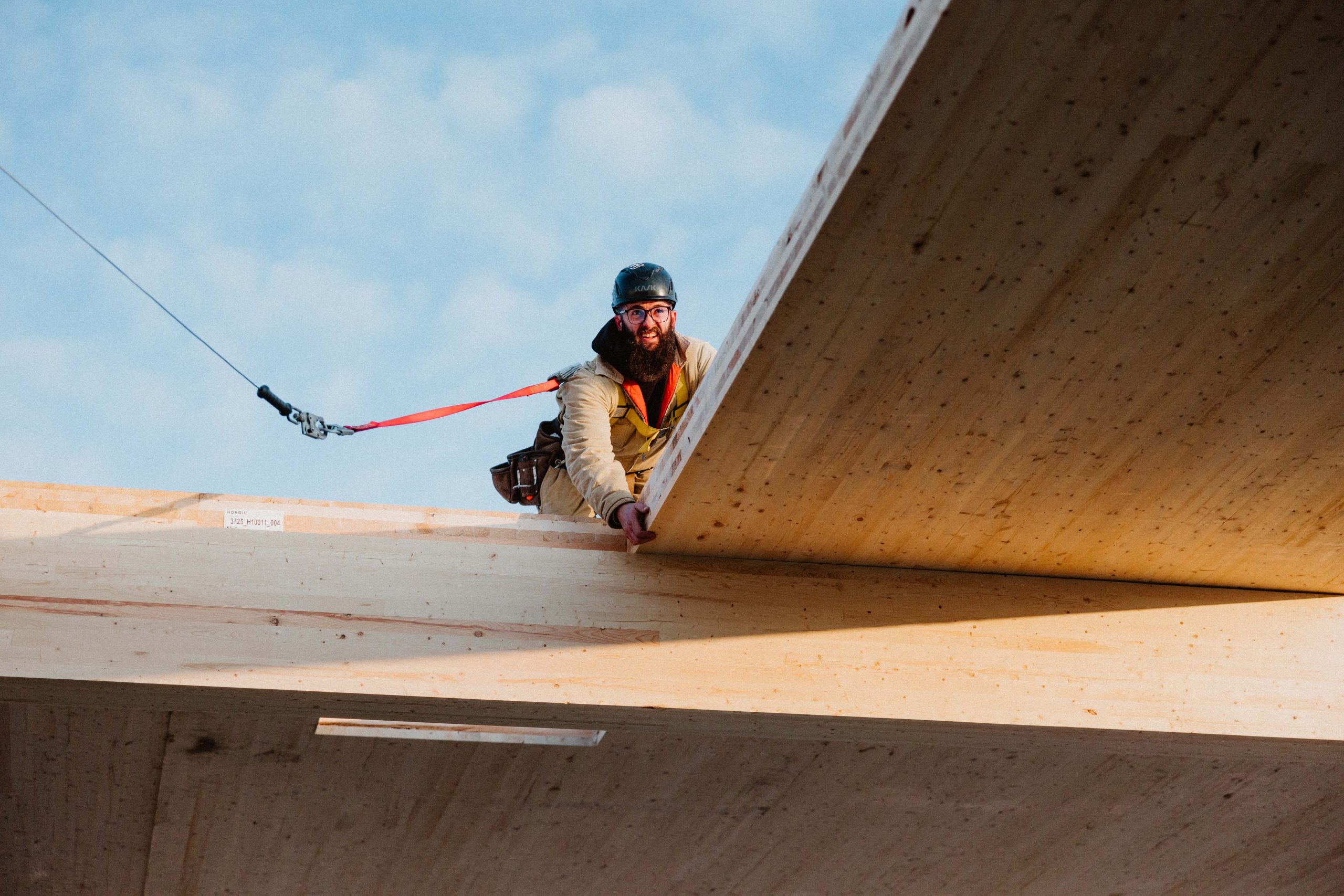
Keeping on Schedule Despite Flying Challenges
Few mass timber builds glide through without turbulence, but this expansion landed on time after roughly 30 months of design and construction. Key partners included:
- Government of Canada (NTCF funding)
- Exchange Income Corporation
- Winnipeg Airports Authority & Transport Canada (oversight on environmental and operational fronts)
Early and consistent involvement from Cornerstone ensured the timber scope remained viable through every iteration—proof that collaboration, not compromise, drives success.
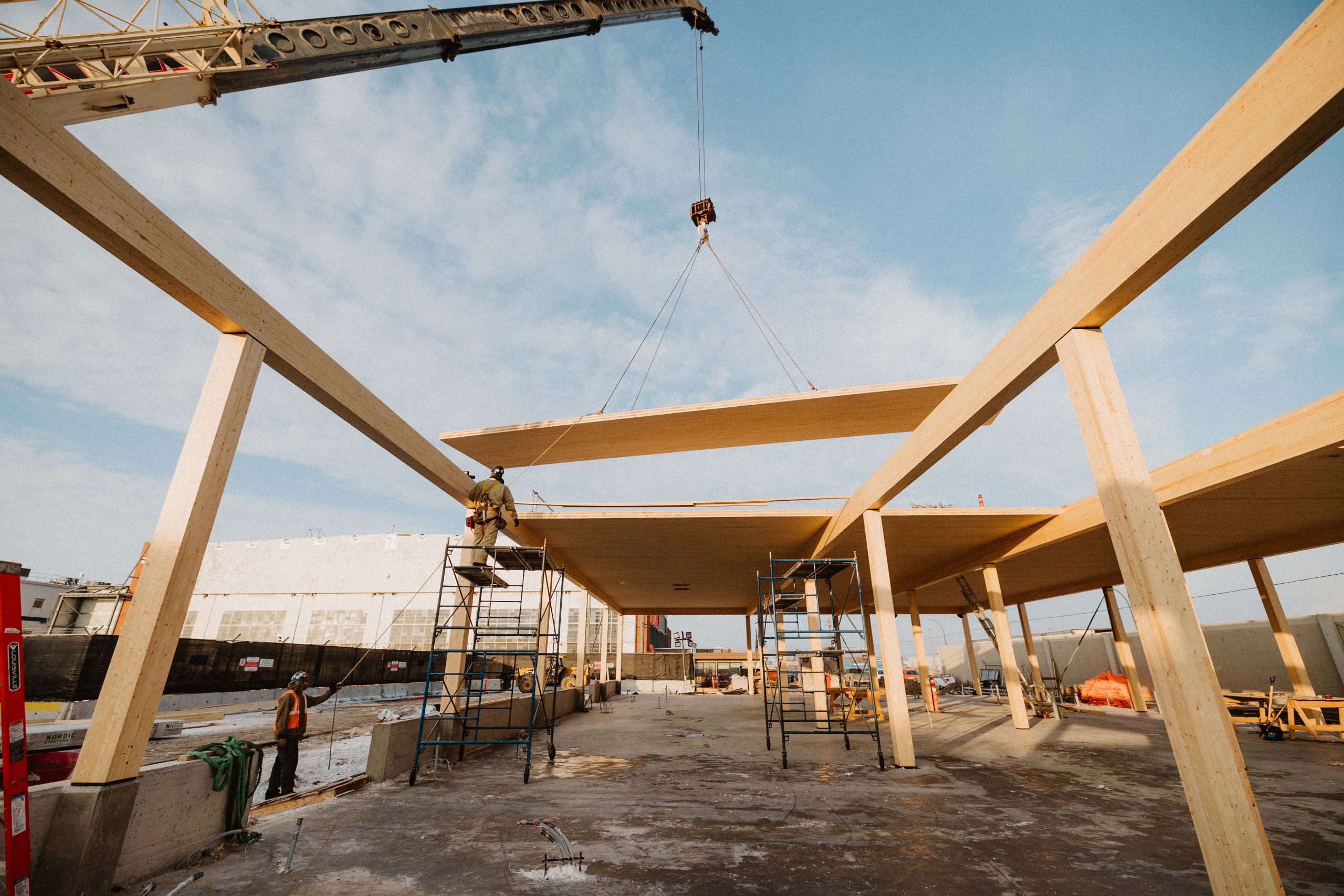
Key Takeaways for Mass Timber AEC Teams:
- Engage early, engage deeply. Involving a mass timber specialist like Cornerstone at concept phase unlocks design and cost efficiencies.
- Design for the material. Timber grids thrive when built around wood’s strengths, not shoehorned into steel logic.
- Detail with intent. Recessed metal caps honor the timber aesthetic while speeding installation.4.
- Adapt on site. A flexible sequencing strategy kept the CLT install on track despite unexpected slab pours driven by weather.
- Think beyond carbon. Mass timber elevates acoustics, light quality, and passenger well‑being alongside its sustainability credentials.
Project Team & Contributors:
Owner/Developer: Perimeter Aviation
Architect: MMP Architects
Structural Engineer: Crosier Kilgour
Mass Timber Engineer: Fast + Epp
Mass Timber Supplier: Nordic Structures
General Contractor: Penn-co Construction
Mass‑Timber Design: Cornerstone Timberframes
Frequently Asked Questions (FAQ):
1. Why mass timber for an airport terminal? Beyond carbon storage, it creates a biophilic, calming environment that supports passenger comfort and operational efficiency.
2. How much CO₂ does the terminal’s timber store? Approximately 256,520 kg, equivalent to removing 55 average cars from the road for one year.
3. Who managed the timber integration? Cornerstone Timberframes led the coordination of design, fabrication, and on‑site installation.
4. What was the project delivery timeline from design to completion? The terminal expansion, including design, fabrication, and mass timber installation, was completed in approximately 30 months with coordinated shop‑finished components integrating directly into the construction schedule.
5. How did the team handle sequencing challenges? By maintaining close communication and re‑sequencing panels in real time, Cornerstone ensured the project stayed on schedule.
Ready to Tackle Your Toughest Mass Timber Challenge?
Leverage Cornerstone Timberframes’ unmatched mass timber experience to turn complex, high‑stakes projects into smooth, cost‑effective successes. Schedule a 30‑minute “Mass Timber Strategy Session”—no slides, just your toughest questions and our proven roadmap for getting ambitious builds to pencil and rise on time.
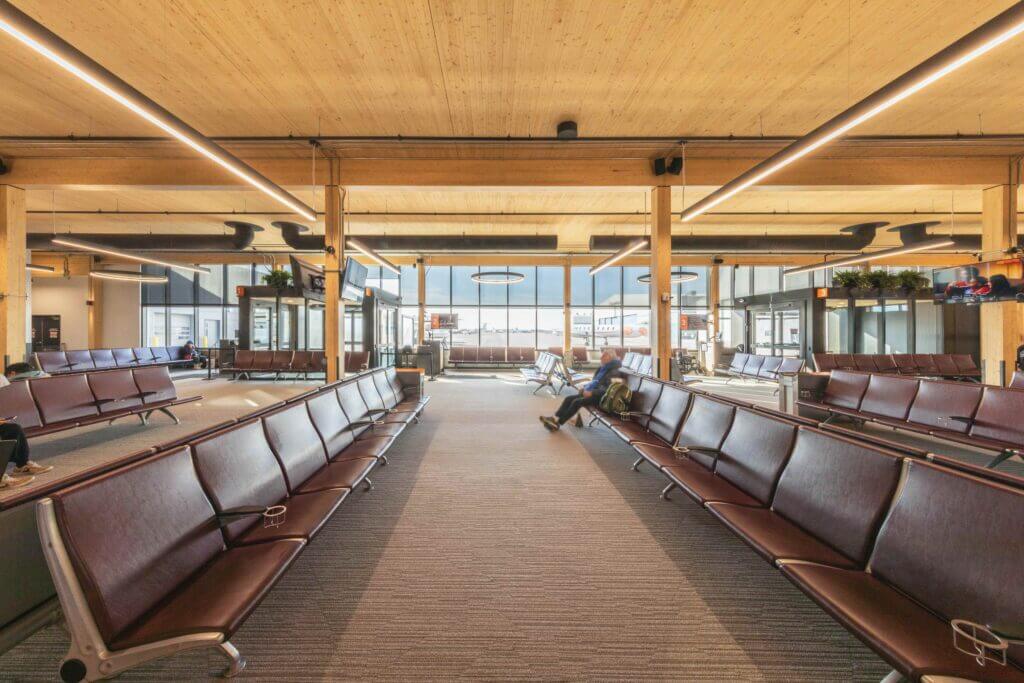
Mass Timber Changes The Game: The San Antonio Spurs’ Victory Capital Performance Center Redefines Professional Sports
Have you ever considered how the built environment impacts elite athletic performance? In a world where every competitive edge counts, the San Antonio Spurs, a franchise synonymous with championship success, have unveiled a groundbreaking answer: the Victory Capital Performance Center.
Completed in 2023, this state-of-the-art training facility isn't just a new home for the Spurs; it's a testament to revolutionary design and sustainable construction, setting new benchmarks in professional sports. As the largest mass timber training facility in U.S. professional sports, and at nearly 140,000 square feet, the largest mass timber structure in Texas upon its completion, this project is truly changing the game. This facility, a partnership between Spurs Sports & Entertainment and Lincoln Property Company, integrates cutting-edge features with a profound commitment to human wellness and environmental stewardship.
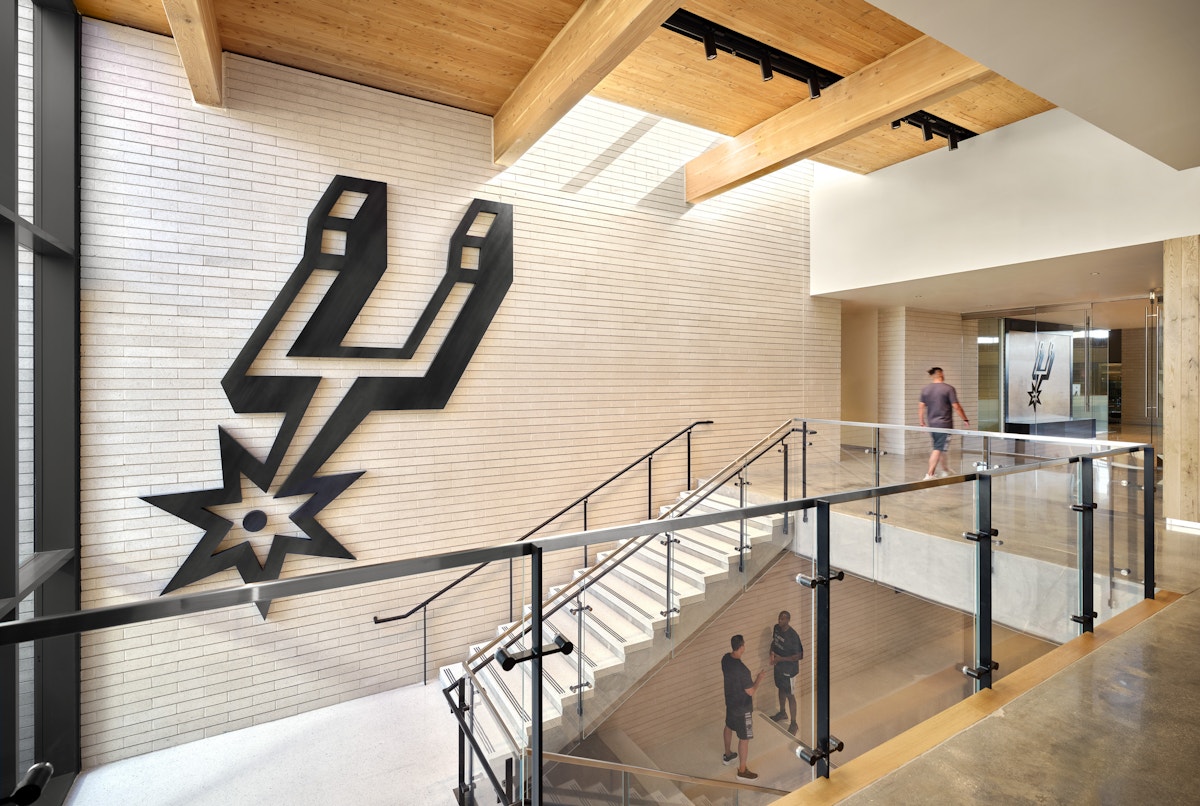
A Vision Crafted for Champions
What truly sets the Victory Capital Performance Center apart is its dedication to athlete well-being, both physical and mental. ZGF Architects, the project architect, embarked on a meticulous benchmarking process, studying facilities globally to understand the intricate needs of athletes.
What did they find?
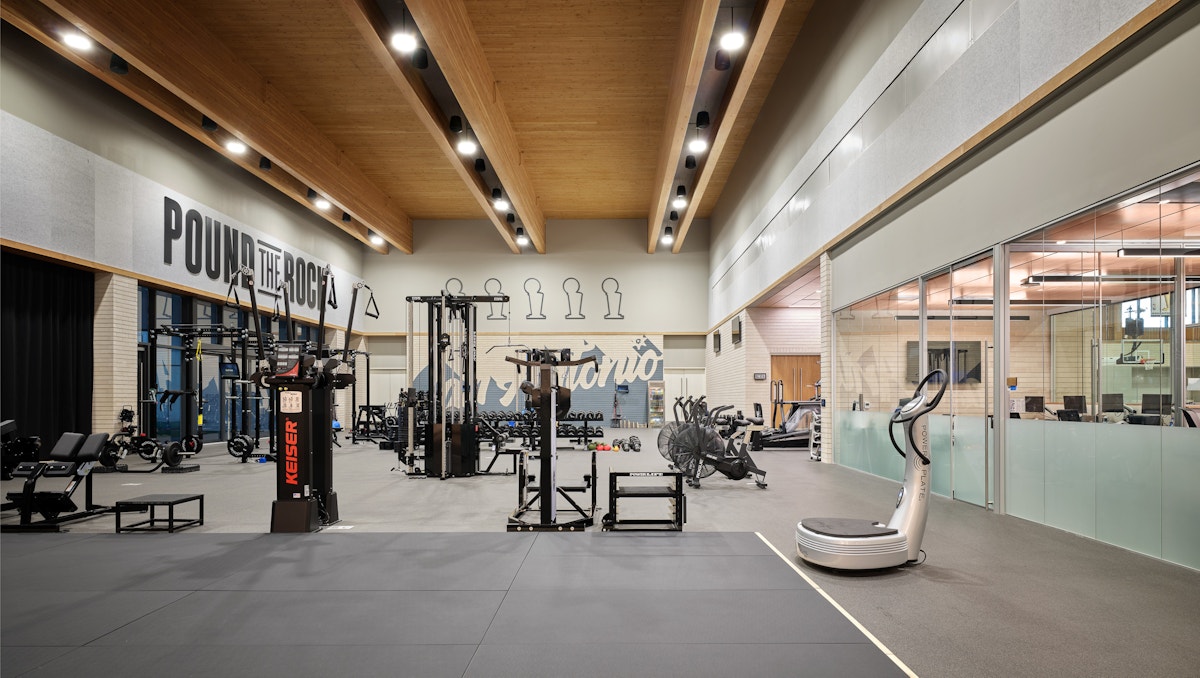
A critical insight: professional athletes often live in an endless cycle of travel with no time outside, disrupting their rhythm and recovery. This realization became a core design driver to infuse the facility with natural light, exposed wood, views, and spaces that prioritize circadian rhythms and rest as much as training.
This is a space where every element contributes to peak performance. The biophilic design approach meant consciously choosing materials and layouts that foster a connection to nature. For instance, mass timber, with its visible wood grain and lack of off-gassing, emerged as a standout material for its natural properties and ability to support athlete well-being under constant pressure.
Occupants can step outside from almost any primary space, from alfresco dining zones to garden recovery areas and balconies for outdoor calls. Even the practice courts, typically relegated to artificial light, are bathed in natural light through clerestory windows, with motorized sun shades to control glare. As Kathy Shaloo Berg, FAIA of ZGF Architects explains, "Focusing on athlete health means choosing materials carefully, with wood standing out for its natural properties and lack of off-gassing, enhanced by advancements in non-toxic glues," - ThinkWood.
The natural elements and connection to the outdoors helps players feel more grounded and supported, mitigating the stresses of constant travel.
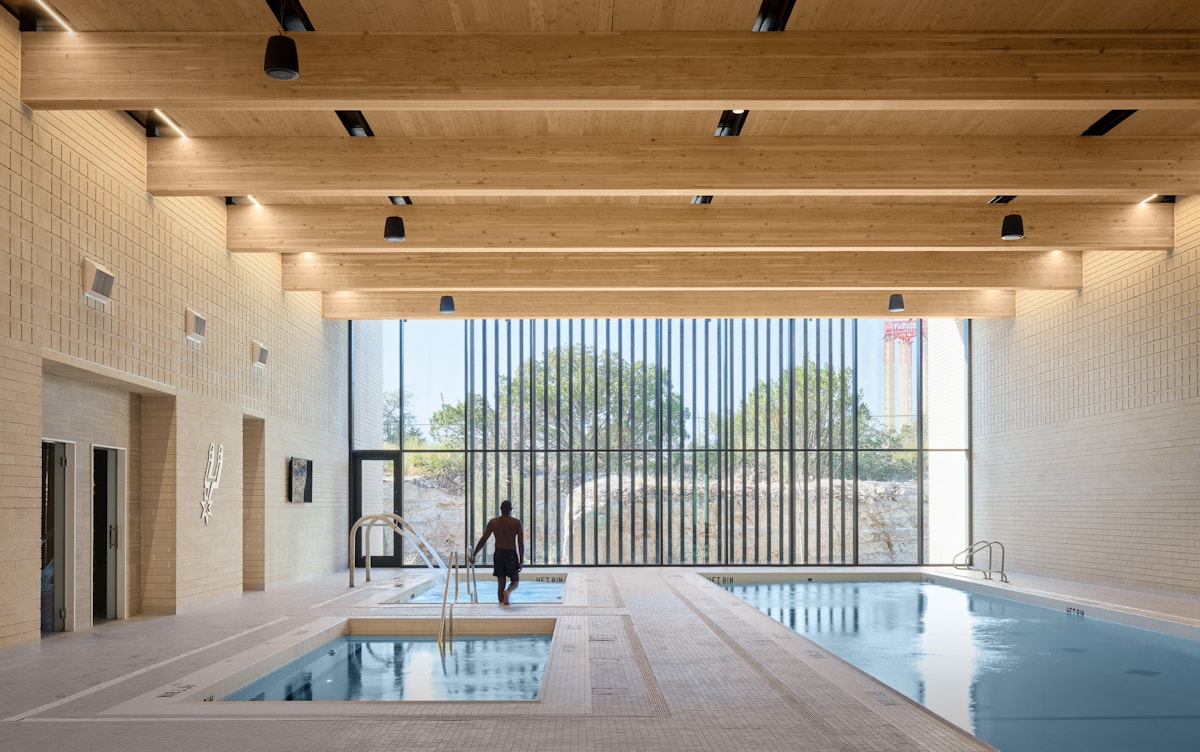
Rooted in Place: San Antonio's Architectural Narrative
Beyond performance, the facility tells a story—a story deeply rooted in San Antonio's rich confluence of culture, sports, and history. Rather than a generic sports venue, the team at ZGF aimed for a design "truly indicative of its setting".
The result?
A contemporary nod to the region’s iconic Mission-style architecture, characterized by masonry walls supporting heavy exposed timber beams and roofs, and an integration of courtyards and arcades.
Kristina Thompsen, Project Manager, ZGF Architects noted what stood out to her: “The intense desire from the Spurs to promote their culture and values of Grit, Respite, Work and Recovery. We incorporated these values with the choice of materials and particularly mass timber. The inherent nature of wood itself encompasses all of these values, and it turned out to be a cost savings over a traditional steel joist system.”
The facility's unadorned materiality, featuring exposed cross-laminated timber (CLT), glulam beams, and concrete masonry units (CMU), reflects this regional authenticity. The extensive use of colonnades provides shelter, shading, and intuitive navigation, while open courtyards seamlessly blend indoor and outdoor spaces—a practical adaptation for Texas's variable climate. The project's location on a 22-acre (or 25-acre) site, formerly a limestone quarry, also inspired its name, "The Rock at La Cantera". This name, and the design elements like repetitive columns and cloisters, draw from journalist Jacob Riis's quote on persistence and breakthrough—the Spurs' enduring slogan, "Pound the rock".
As Berg eloquently puts it, "The interplay of these repetitive structures with the unique San Antonio sunlight is quite beautiful and comes alive throughout the day—almost acting like a make-shift sundial". - Think Wood
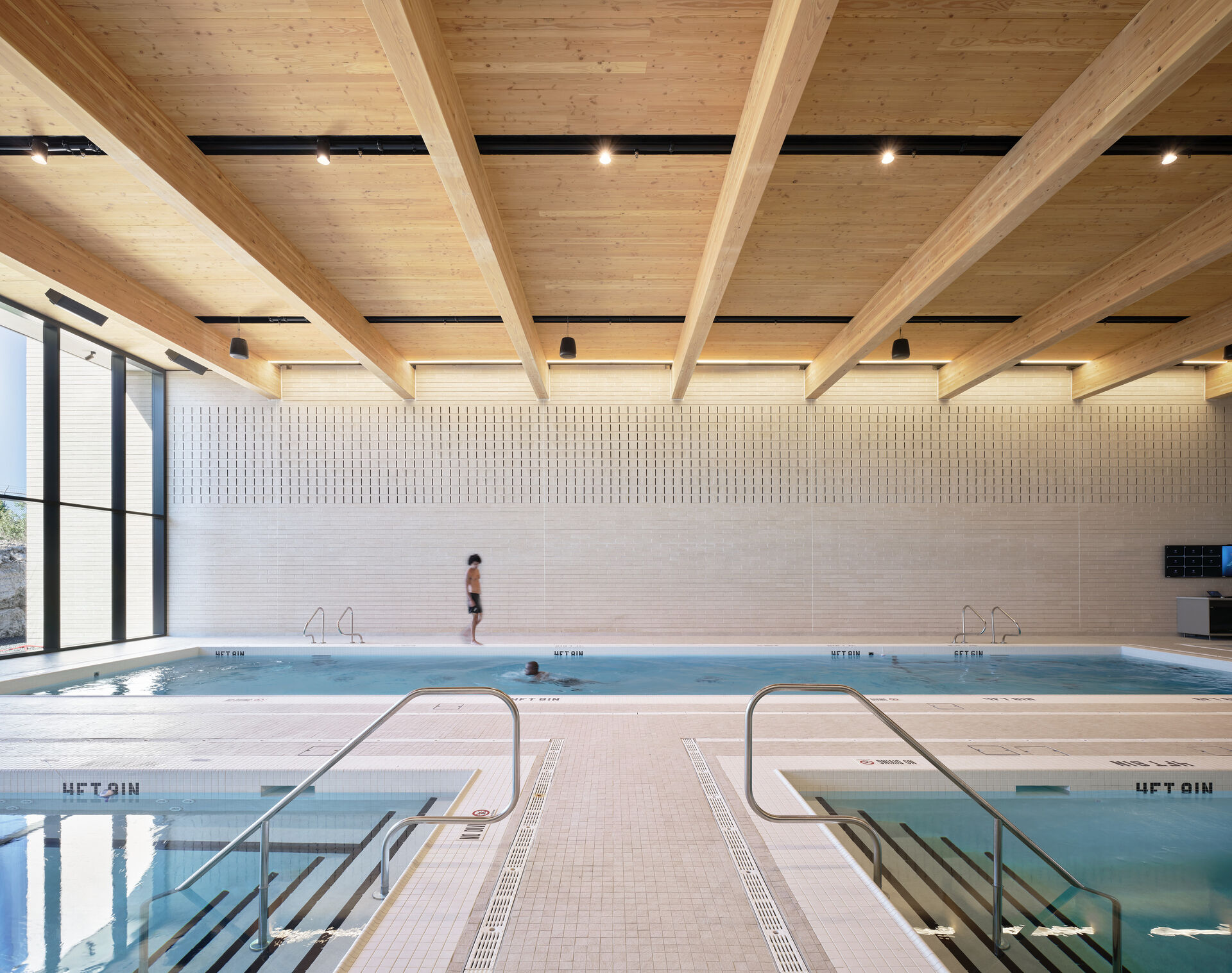
Putting Mass Timber to the Test
The choice of mass timber was not merely aesthetic or philosophical; it was a strategic decision driven by sustainability, performance, and efficiency. The facility's primary structure consists of glued-laminated timber (glulam) columns and beams spanned by cross-laminated timber (CLT) decking, supported by masonry shear walls. Arup, the structural engineer, played a vital role in guiding this design, recognizing mass timber's significantly lower carbon footprint compared to traditional concrete and steel.
This project pushed the boundaries of what's possible with long-span wood construction. It utilizes the largest continuous glulams on the market, with 20 beams, each an impressive 130 feet long and 75 inches deep (or 6.5 feet tall), to achieve its vast, column-free interior. The ingenuity extends to concealing steel knife plates and bolt connections behind at least two inches of wood, creating a clean, seamless aesthetic. The double glulam beams house fire suppression, and lighting conduits, while Douglas fir fins tuck away acoustic materials and return air louvers to reduce sound reverberation.
“One of the biggest challenges was getting a structural beam to span the length of a basketball court. The double beams that we have in the courts are the largest mass timber beams that are made. We also had the challenge of fitting our mechanical and electrical systems in the pockets between the beams, so the coordination between the various disciplines was critical.” - Kristina Thompsen, ZGF Architects.
The environmental benefits are equally compelling. The structural wood in the Victory Capital Performance Center sequesters the carbon equivalent of taking over 420 passenger cars off the road for a year, or approximately the amount of carbon sequestered by nearly 2,300 acres of U.S. forest in one year of growth. This makes mass timber a renewable, carbon-sequestering alternative that stands in stark contrast to carbon-intensive structural materials.
"This project proves mass timber isn't just sustainable: its innovation and suitability make it ready for high-profile spaces." - Eleonora Dalfovo, MTC Solutions
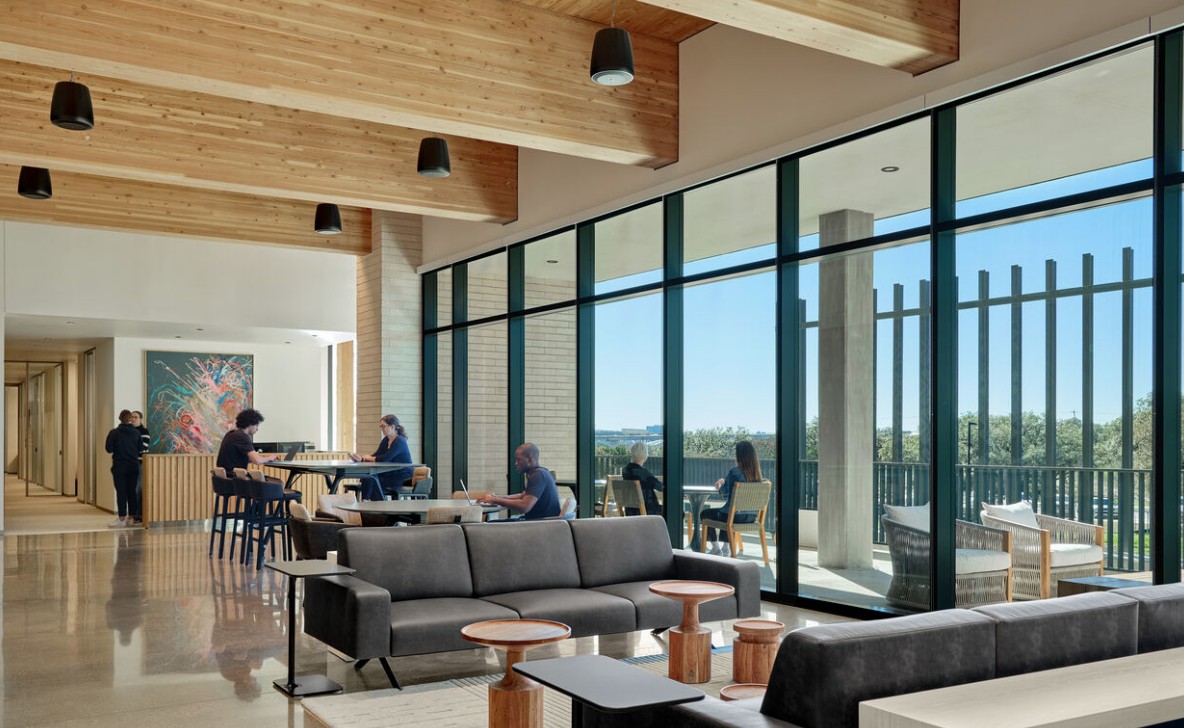
Precision Engineering and Overcoming Challenges
The journey to completion was not without its hurdles. Joeris, the general contractor, highlighted the challenges, including delays caused by the COVID-19 pandemic, necessitating a collaborative approach to manage budgetary constraints and material supply chain disruptions. Site-specific complexities, such as navigating a rock shelf, required customized foundation solutions. Furthermore, ensuring seamless communication was paramount, given that architects and engineers were located out-of-state.
Arup's engineering expertise was critical in navigating these complexities and achieving the ambitious design goals. They implemented an "energy-efficient overhead displacement ventilation system" in the practice courts and strength and conditioning spaces to maintain comfort and minimize exposed ductwork, while also conducting computational fluid dynamics (CFD) analyses to confirm performance. For the elevated court, Arup even analyzed the floor structure and column placement below to prevent undesirable vibration, ensuring optimal player performance. MTC Solutions contributed significantly by supplying structural hardware, with Eleonora Dalfovo emphasizing the importance of early communication with all parties to understand specific requirements and match them with the right product, ensuring timely on-site delivery and proper installation training. Her team successfully supported a product swap to meet precise requirements.
Beyond structural integrity, Arup's lighting design incorporated tuneable circadian lighting in player areas to improve mental and metabolic function, aligning with the project's biophilic goals. The integration of services with exposed structural elements was carefully planned to maximize visibility of the architecturally exposed mass timber.
“The result is absolutely stunning, with every mass timber element adding a sense of warmth and character that only this material can provide… We look forward to seeing how this project inspires other professional organizations to explore the potential of mass timber in the future.” - Trevor MacKay, SmartLam North America™
Beyond the Courts: A Community Hub
The Victory Capital Performance Center is more than just an exclusive training ground for professional athletes; it's envisioned as the heart of a larger 22-acre (or 25-acre) wellness hub, "The Rock at La Cantera". This development will include an events plaza, parks, a human performance research center, wellness centers, and a team store. The facility deliberately balances the players' need for private, restorative spaces with the public's desire to connect with their team. Joeris emphasized this community focus, noting the inclusion of outdoor public spaces like a splash pad, food truck area, and a large screen for fans to gather year-round, underscoring the belief that sports complex construction should serve the broader community. The Spurs Plaza at the front of the structure welcomes the community to gather, watch games on a large screen, and enjoy local cuisine.
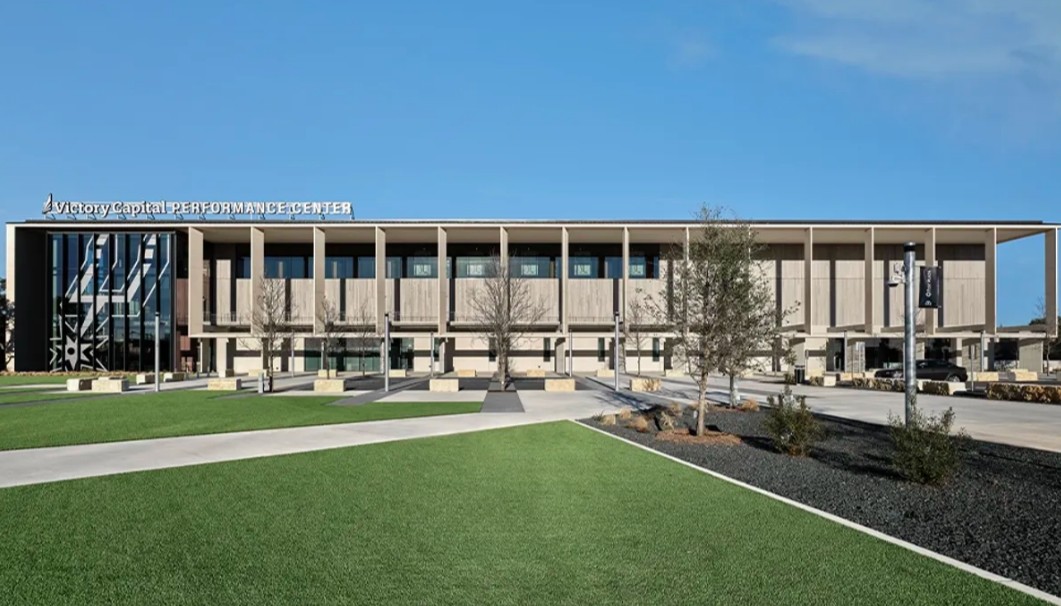
Conclusion: A New Era for Sports Facilities
The completion of the Victory Capital Performance Center marks a significant milestone, not just for the San Antonio Spurs, but for the entire professional sports and construction industries. Spurs CEO R.C. Buford lauded the facility, stating,
"As a result of ZGF’s ingenuity and eye for revolutionary and human-centered design, this facility gives us a competitive edge in sports technology and performance and an opportunity to leverage sustainable innovations such as mass timber and solar energy production to ensure a positive impact on the world around us". - Forbes
The overwhelming positive feedback from management and players alike, particularly regarding the quality of light, connection to the outdoors, and the feel of the timber-exposed interior, suggests a promising future.
As Berg concludes, "I think it can encourage new possibilities for using more wood in professional sport facilities in the future".
The Victory Capital Performance Center proves that mass timber is not just a sustainable alternative but a material choice ready for the highest-profile, performance-driven spaces. This project serves as an example for how to integrate advanced athletic needs with a strong sense of place and a deep commitment to human and environmental well-being.
Project Contributors:
- Spurs CEO: R.C. Buford
- Structural Engineer: Arup
- Architect: ZGF Architects
- CLT Supplier: SmartLam North America™
- Timber Installer: Timberlyne Group
- Hardware Supplier: MTC Solutions
- Construction Manager: Joeris General Contractors, LLC
- Glulam Supplier: American Laminators now known as Timberlab
- Photography Credit: Dror Baldinger
Project Specifications:
- Completed: 2023
- Project Name: Victory Capital Performance Center
- Location: San Antonio, Texas, United States of America
- Timber Products: CLT Decking, Glulam Columns, Glulam Beams
- Owner: Spurs Sports & Entertainment and Lincoln Property Company
- Size: 138,900 square feet (alternatively 138,898 sq ft or 134,000 sq ft)
Frequently Asked Questions (FAQs):
- What makes the Victory Capital Performance Center a "game changer" for professional sports facilities? It is the largest mass timber training facility in U.S. professional sports and the largest mass timber structure in Texas upon its completion, showcasing how sustainable materials can meet the rigorous demands of high-performance athletic environments while prioritizing athlete well-being and a connection to nature.
- How does the facility incorporate "biophilic design" to support athletes? The design integrates natural elements such as exposed mass timber, ample natural light, and direct access to outdoor spaces from primary areas to support circadian rhythms, reduce stress, improve mood, and enhance focus, ultimately promoting overall human performance and wellness.
- What specific types of mass timber were used and what was their impact? The facility extensively uses cross-laminated timber (CLT) for decking and glue-laminated timber (glulam) for columns and beams, including twenty record-setting 130-foot long glulam beams. This structural wood sequesters carbon equivalent to removing over 420 passenger cars from the road for a year, demonstrating significant environmental benefits.
- Were there any notable challenges during the construction of this pioneering facility? Yes, the project faced challenges including delays due to the COVID-19 pandemic, budgetary constraints, material supply chain disruptions, and the need for customized foundation solutions due to a rock shelf on site. Collaboration and precise communication were key to overcoming these hurdles.
- How does the facility connect to the local San Antonio community? Beyond its primary use for the Spurs, the facility is part of "The Rock at La Cantera" wellness hub development, which includes public spaces like a plaza, parks, and areas for community gatherings. Its design also draws inspiration from San Antonio's historic Mission-style architecture, rooting it deeply in the local culture and landscape.
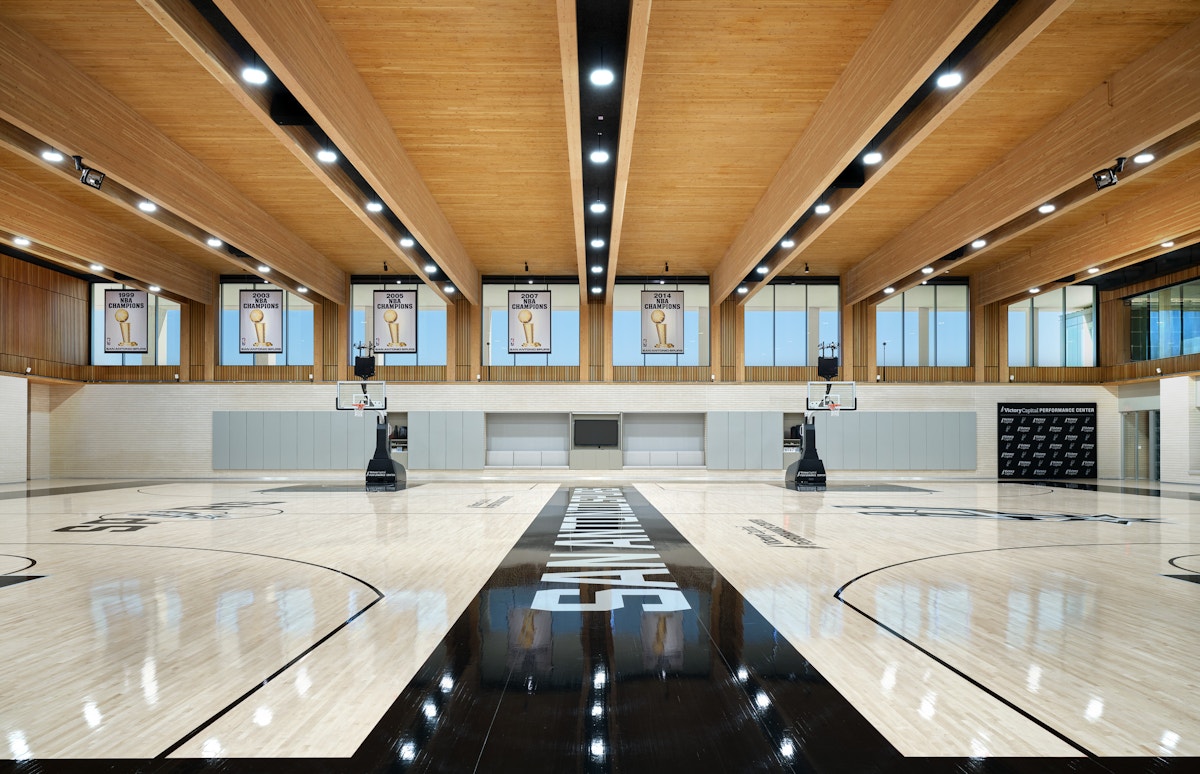
L'Angolo Estate: A Masterclass in Mass Timber Construction Rooted in Oregon's Wine Country
In the heart of Oregon's Willamette Valley wine country, L'Angolo Estate has emerged as a testament to thoughtful design, seamlessly blending winemaking philosophy with innovative architecture. Just west of Newberg, nestled within the north Dundee Hills on a 23-acre vineyard, this family-owned winery has captured attention with its stunning new tasting room, a structure not merely built, but crafted to be a direct expression of its Oregon roots.
Completed in 2016, the 2,200 square foot facility stands as a shining example of mass timber construction and modern design principles. Its story is not just about a building, but about a philosophy, echoing the broader trend in Pacific Northwest architecture to re-embrace the region's rich timber heritage.
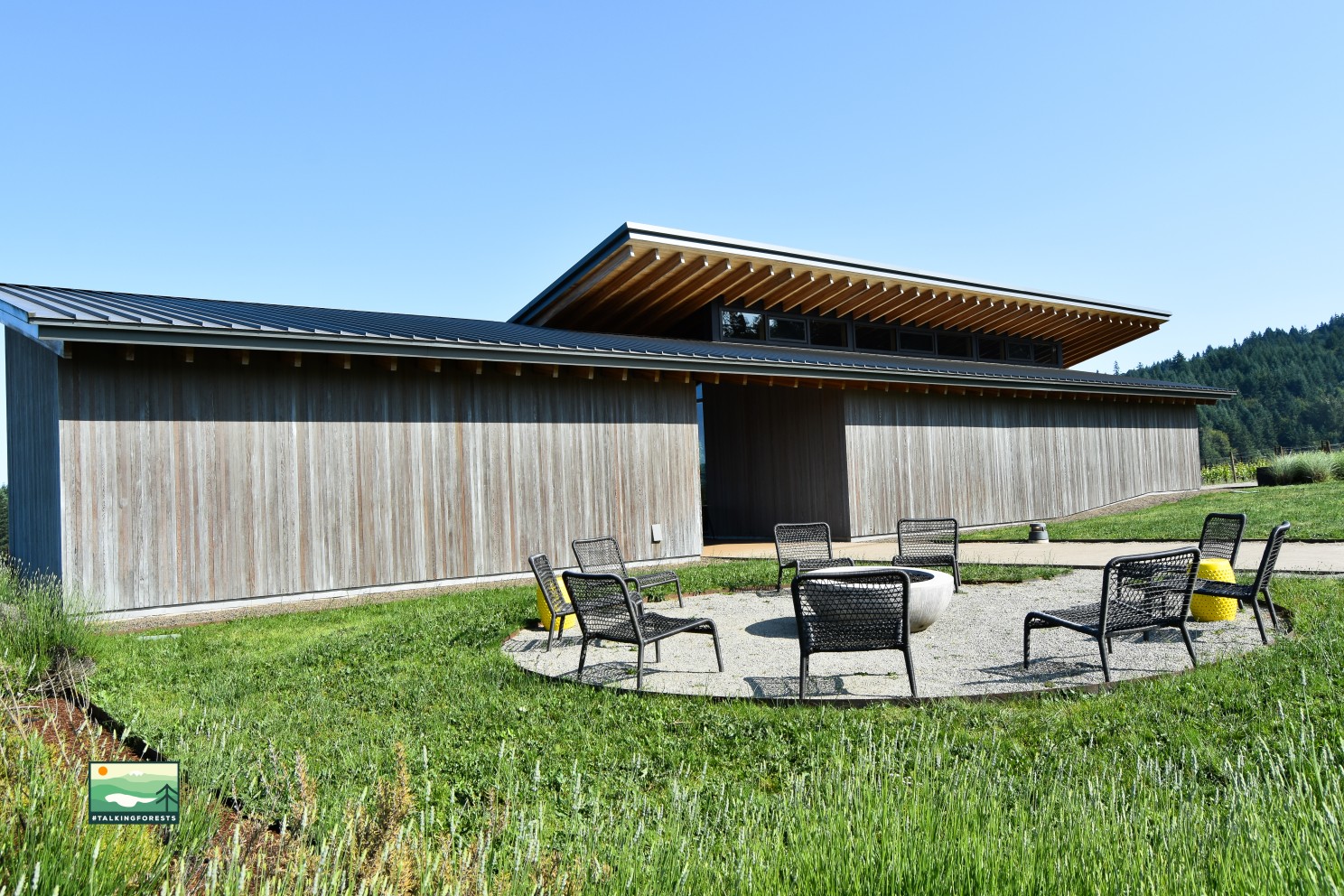
The Vision Behind the Vines
At the core of L'Angolo Estate's identity is a profound commitment to authenticity. Winemaker and owner, Chase Renton, articulates this ethos clearly: "We make and grow everything ourselves and we don’t buy or sell any fruit," highlighting a hands-on approach that extends from the vineyard to the bottle. This dedication to unembellished, direct expression of the Oregon soils and climate was the guiding principle for the tasting room's design. As Renton shared, the shared goal with the architects was to "replicate the wine" itself. "We aimed for simplicity and for natural beauty. Just like our wine, we wanted the tasting room to be elegant without being too grandiose," he explains, a sentiment that resonates through every element of the new structure. It was paramount, Renton adds, for them to "know the people who walk through our doors," ensuring that "those who visit will get the best hospitality" within this carefully conceived space.” - PDX Monthly
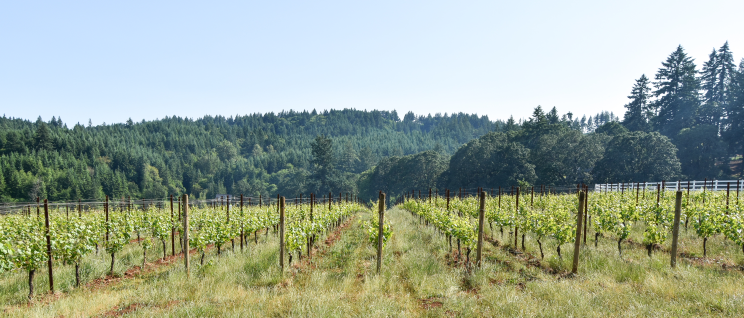
Timber and Light: Architectural Innovation in Wood
LEVER Architecture, the acclaimed firm behind the design, took this philosophy to heart, creating a structure that is both sophisticated and deeply connected to its environment. The design was inspired by the broad, canopied native Oregon oak trees that dot the valley, and also drew cues from traditional pole barns and other vernacular structures found in the Willamette Valley, anchoring it firmly in its regional context. This blend of natural inspiration and local architectural precedent creates a design that is both innovative and intimately familiar.
The defining characteristic of the L'Angolo Estate tasting room is its innovative use of timber, a material choice that positions it squarely on the "timber train" of contemporary Pacific Northwest architecture. The space is literally "bathed in light and redolent of Oregon timber," creating an immediate sensory connection for visitors upon entry. This isn't just any timber; it features Oregon-milled Douglas fir ceilings, sourced from a mill in Drain, Oregon, signifying a commitment to regional resources and craftsmanship. The exterior is clad in durable Western red cedar siding and sleek dark anodized aluminum, forming a refined yet robust material palette that speaks to both natural beauty and modern elegance. A concrete bar grounds the interior, providing a striking, cool contrast to the warmth of the wood, further enhancing the material dialogue within the space.
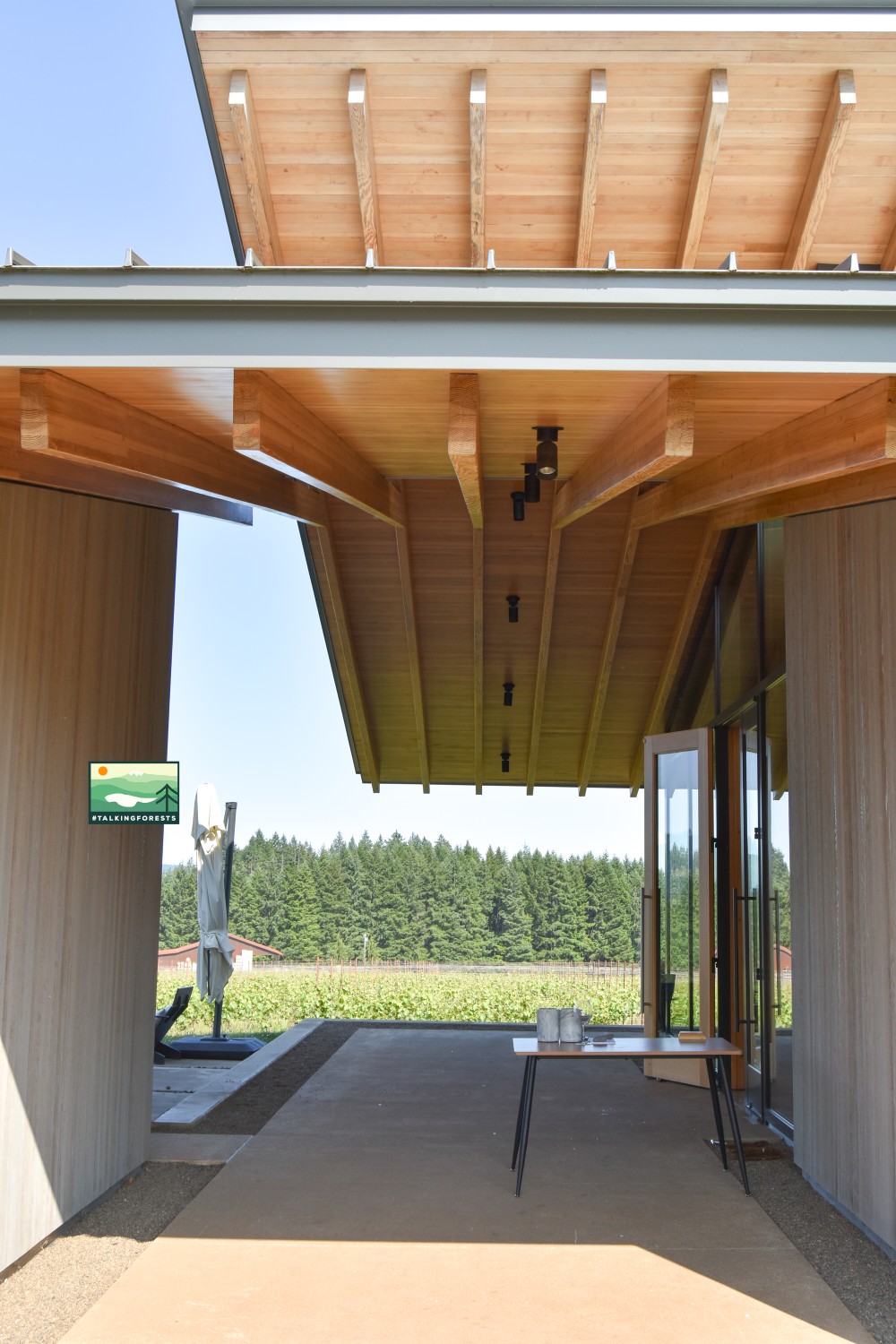
What truly sets this project apart in the realm of mass timber construction is its unique structural approach. LEVER Architecture implemented an "inverted roof structure," a clever design where "glulam joists are hung from hidden steel beams within the roof cavity." This ingenious technique allows for the dramatic effect of "floating timber roof planes," giving the impression of lightness and expanse, defying the inherent mass of the material itself. The project incorporates 86 glulam beams, each meticulously hung from a concealed steel structure. To achieve this precise and visually striking design, the team collaborated closely with fabricators, refining a "commodity glulam product into an iconic expression for the winery" and ensuring the exact beam specifications were met for this ambitious vision.
Integrating with Nature: A Seamless Indoor-Outdoor Experience
Beyond its structural ingenuity, the tasting room's design fosters an intimate connection with the surrounding vineyard and valley. Two cantilevered roof structures interlock at the point of arrival, creating a welcoming and expansive entry that immediately draws the eye towards the breathtaking landscape. How does one truly experience the terroir of a wine without feeling the very air from which its grapes draw life? The architects answered this by thoughtfully opening the public space to the north, south, and east, utilizing a structural wood glazing system that frames the panoramic views of the vineyard and the expansive Oregon sky.
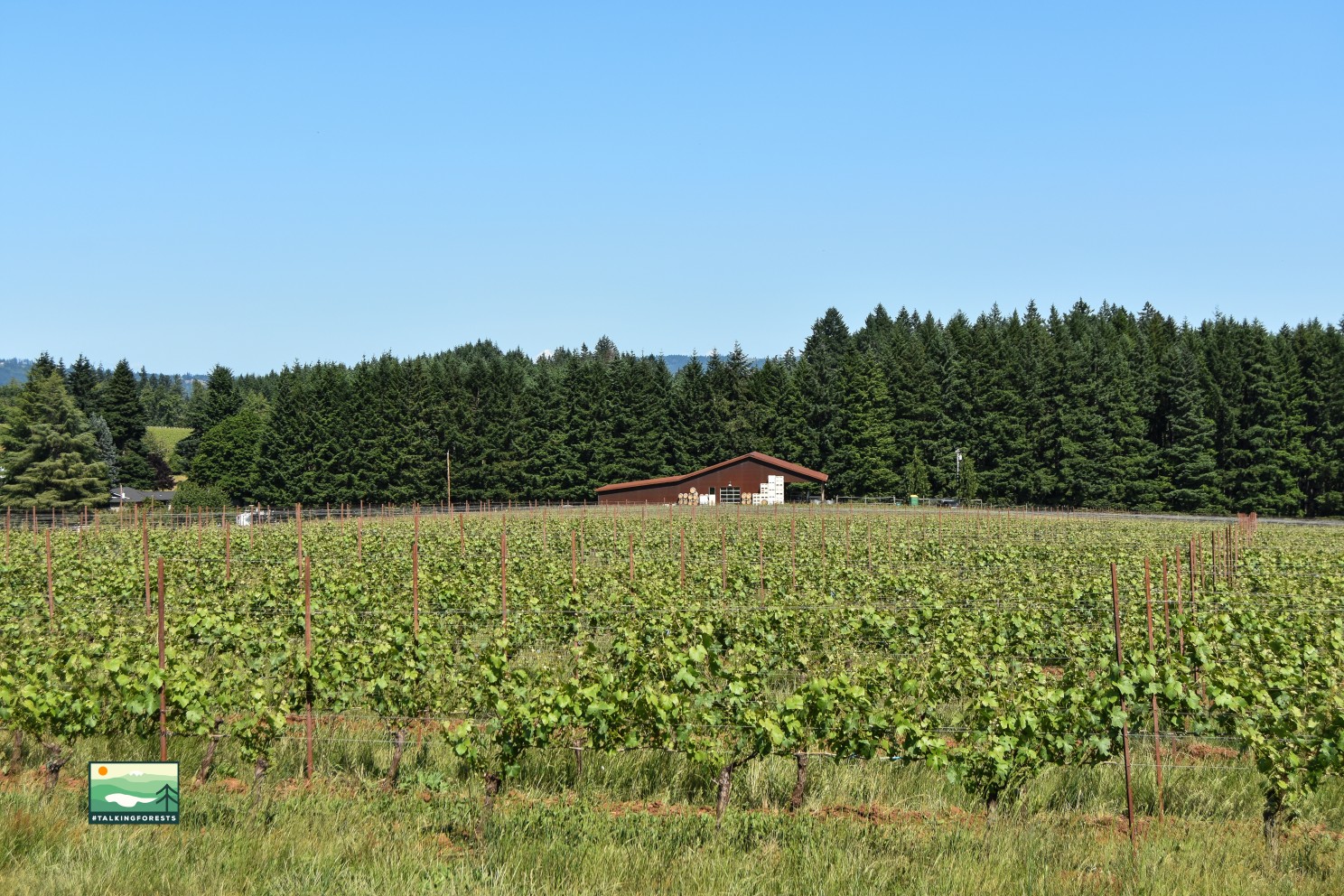
This connection isn't merely visual; it's profoundly functional and experiential. Two large sliding doors, centrally positioned at the tasting room bar, seamlessly merge the indoor and outdoor spaces, effectively bringing the vineyard into the heart of the building. These expansive doors, along with upper clerestory windows, are integral to the building's environmental strategy, serving as a highly effective passive cooling system during warmer summer months. This thoughtful integration of natural ventilation underscores the winery's commitment to reflecting the climate without embellishment, allowing the building to breathe with its surroundings.
Sustainability at its Core
L'Angolo Estate’s commitment to its environment extends to its operational sustainability, marking another significant aspect of this mass timber construction project. The building has been designed with future environmental goals in mind & forward-thinking practices that align with the broader green building movement.
"The award-winning architecture of our tasting room creates an atmosphere of understated elegance that perfectly complements our wine experience. When guests walk into this space, they immediately feel the harmony between our modern design and the natural beauty of the Willamette Valley. The warm wood elements and clean lines enhance our wines, creating an environment where visitors can truly appreciate both the craftsmanship in our bottles and the thoughtful design that surrounds them. It's remarkable how the architecture itself has become part of our brand story, drawing guests who appreciate exceptional wine and exceptional design." - Galen Hagerty, VP of Sales for L'Angolo Estate
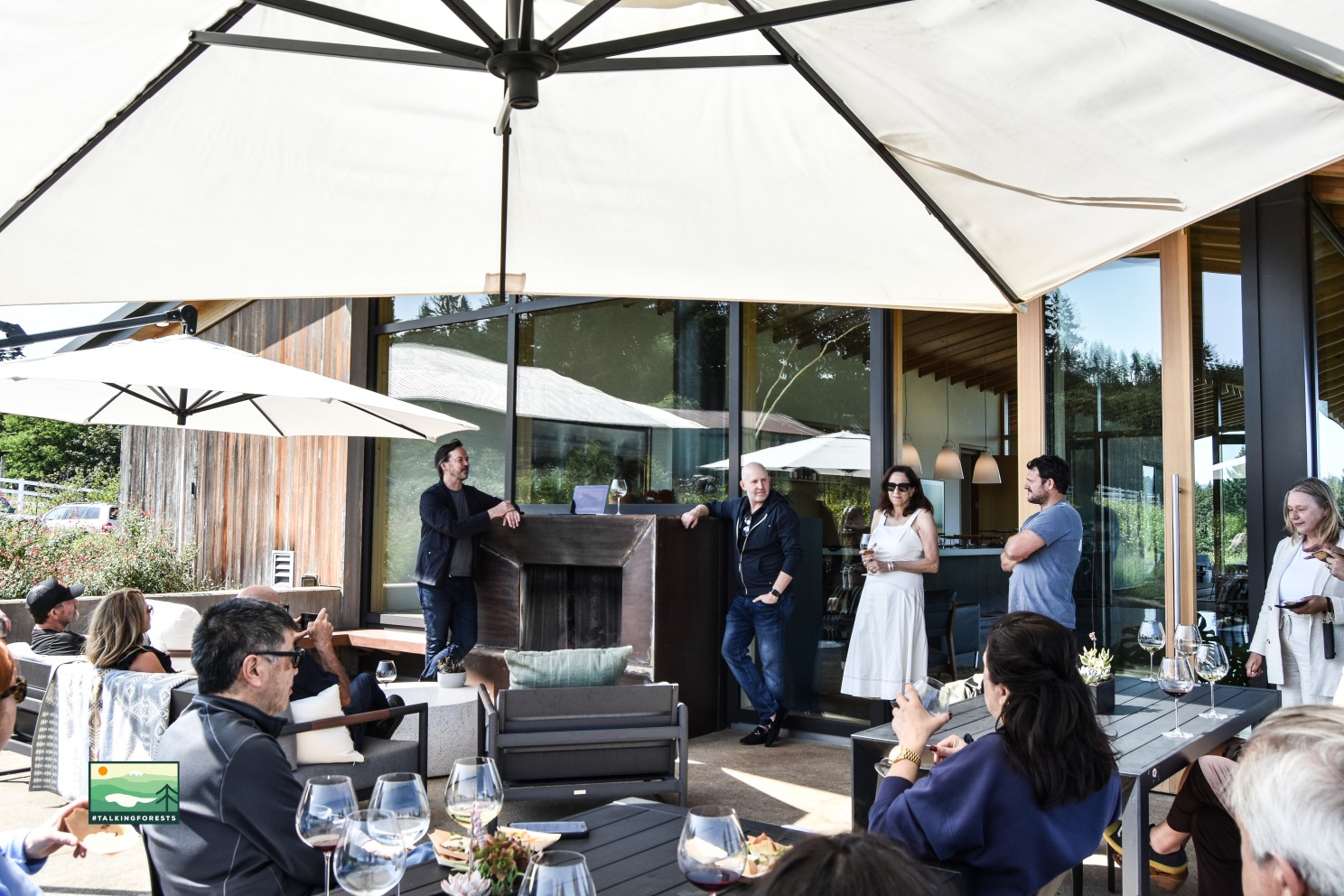
Thomas Robinson, FAIA from LEVER Architecture, Galen Hagerty from L'Angolo Estate Winery, James Leasure, 2025 PDX Modern Home Tour Producer seen above talking to guests.
Recognition and Impact
The innovative design and successful execution of the L'Angolo Estate tasting room have garnered significant recognition within the architectural and design communities, cementing its status as a notable achievement in mass timber construction. The project has received numerous accolades, including a prestigious Merit Award from AIA Portland, a Special Mention at the Architizer A+ Awards, and was a Finalist for the Gray Awards. Furthermore, WoodWorks, a leading advocate for wood products in construction, honored the project with a Regional Excellence Award in 2018, underscoring its contribution to excellence in wood building design. Its striking aesthetics and thoughtful integration with the landscape have also led to features in prominent publications such as Sunset Magazine (specifically in its 2022 Wine Issue), Dezeen, and Dwell, reaching a wide audience interested in architectural innovation and wine country experiences.
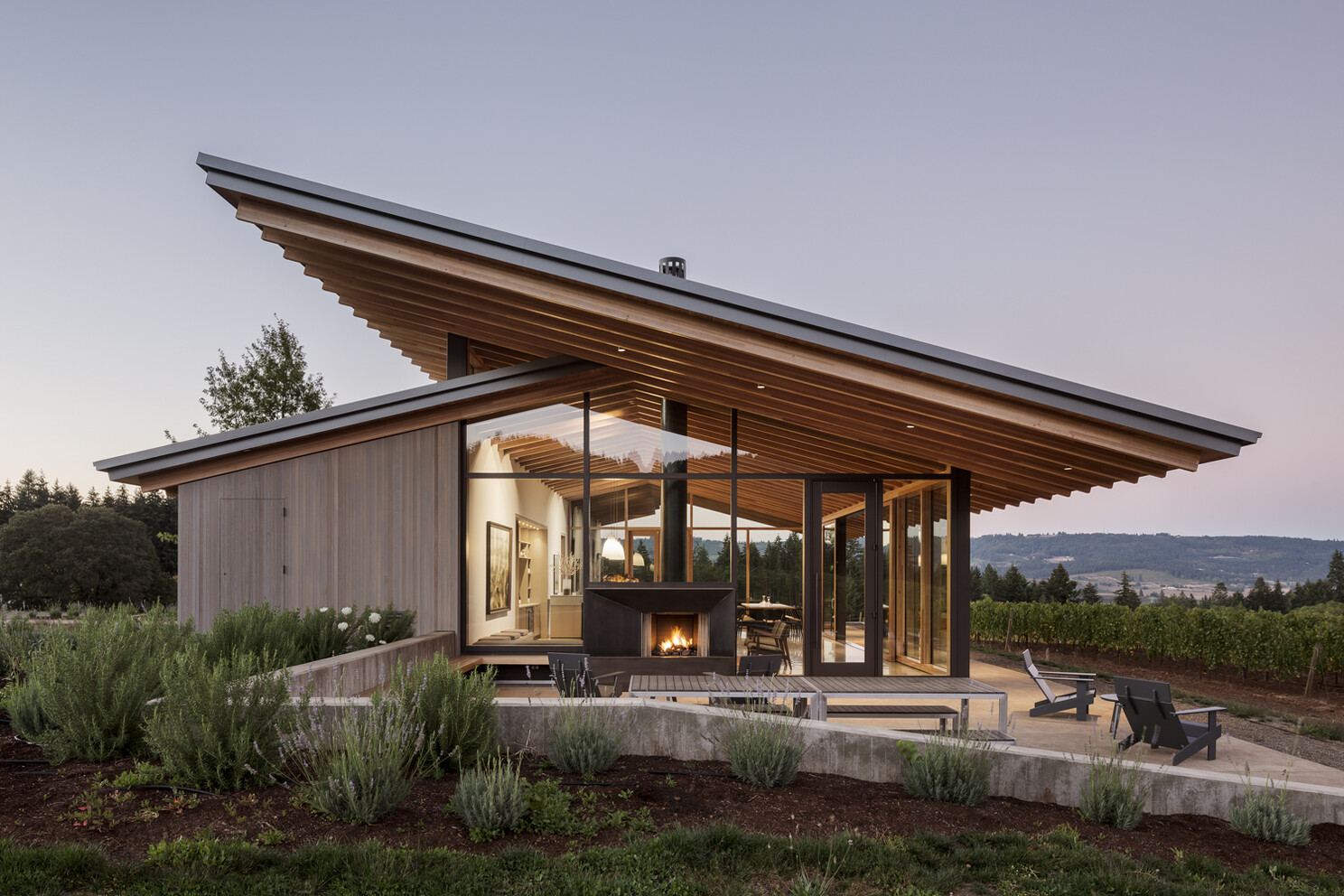
Conclusion
The L'Angolo Estate tasting room stands as a compelling case study for Mass Timber Construction, demonstrating how architecture can profoundly express a brand's core values while pushing the boundaries of design. By leveraging the natural beauty and structural capabilities of Oregon-milled timber, LEVER Architecture has created a space that is both a "perfect expression of the soil and the wine," as described by Chase Renton, and a destination that offers visitors an authentic, immersive, and elegantly simple wine tasting experience, truly rooted in the spirit of the Willamette Valley.
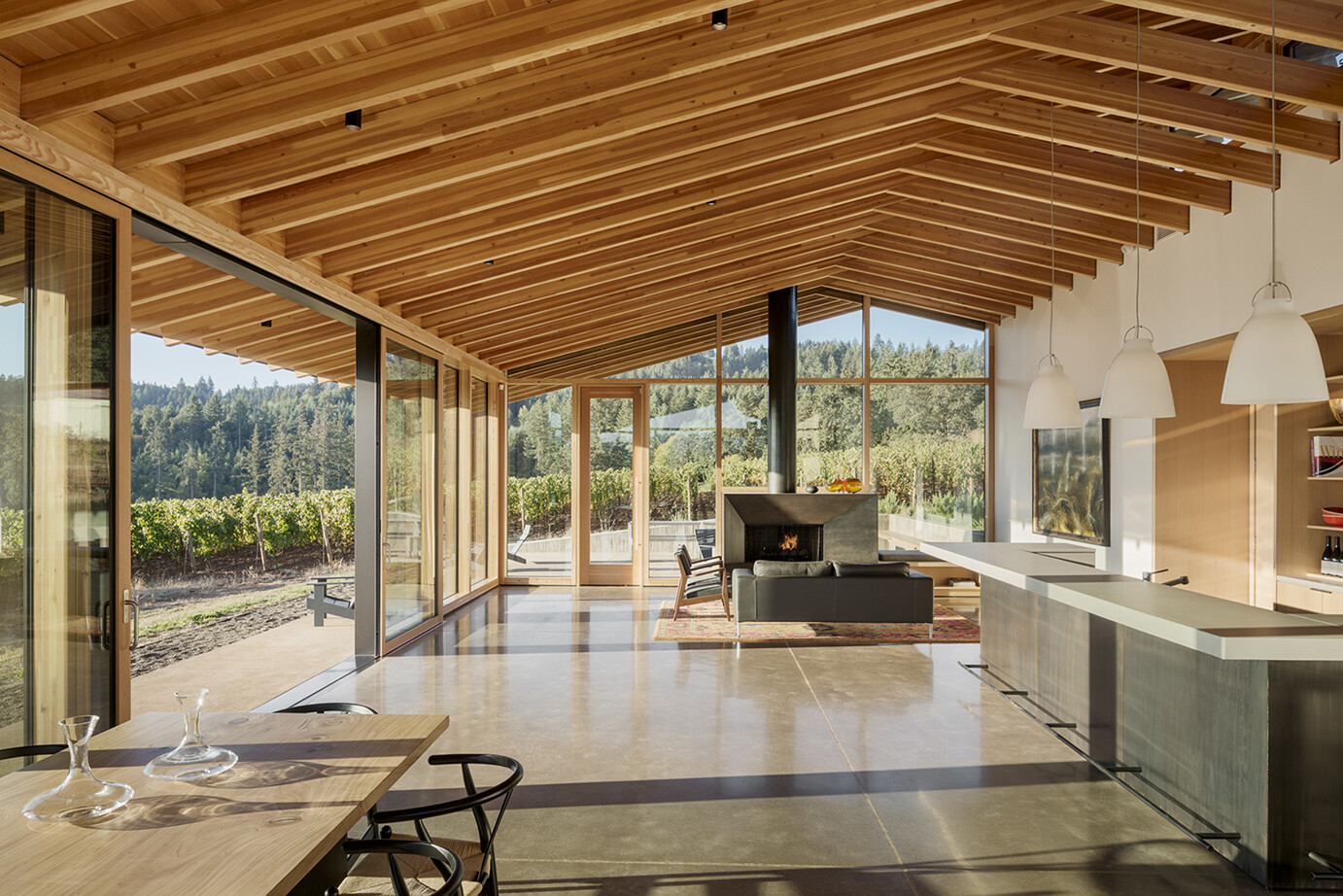
The L'Angolo Estate Winery Project Team:
- Owner: L’Angolo Estate
- Architect: LEVER Architecture
- Energy Modeling: Glumac
- Contractor: A.C. Schommer & Sons, Inc.
- Structural Engineer: Schutte Consulting Engineers
- Manufacturers: Timberlab now known as American Laminators, Creative Woodworking NW, Sierra Pacific Windows
- Photography: Jeremy Bittermann and Candra Burns
Candra's Editor Note: Being 1 hour away from Portland is nice when you get Portland Modern Home Tour Tickets from James Leasure and then walk around until you get a chance to see Willamette Valley Winery scenes to cap the night. This was a chance to soak in the Oregon timber scene with wonderful wine and people. I was taken aback by the architecture and class of this estate. Seeing everyone felt warm and welcoming and I did not want to go home, yet. Writing this gave me a way to preserve the moment and share it with you!
Frequently Asked Questions (FAQs)
- What is the core design philosophy behind the L'Angolo Estate tasting room? The design philosophy was to create a space that is a direct, unembellished expression of Oregon's soils and climate, reflecting the winery owner's straightforward approach to winemaking. Winemaker Chase Renton aimed for simplicity and natural beauty, desiring the tasting room to be elegant without being too grandiose, much like their wine.
- How does the L'Angolo Estate tasting room incorporate mass timber elements? The tasting room extensively uses Oregon-milled timber, specifically Douglas fir for its ceilings, and Western red cedar siding for the exterior. A key innovation is the "inverted roof structure" where 86 glulam beams are hung from concealed steel beams within the roof cavity, creating the unique appearance of "floating timber roof planes".
- What sustainable features are integrated into the tasting room's design? The design incorporates passive cooling through two large sliding doors and upper clerestory windows, which bring the vineyard's air into the space during summer. Furthermore, the building is designed to meet Oregon's Path to Net Zero program criteria once a planned solar array is installed on the roof, demonstrating a commitment to environmental responsibility.
- What is the significance of the cantilevered roof structures in the design? The two cantilevered roof structures interlock at the point of arrival and were inspired by the broad canopies of native Oregon oak trees, helping to frame the landscape and connect the architecture to the natural environment and local vernacular traditions.
- When is the L'Angolo Estate tasting room open for visitors? The tasting room is open Fridays to Sundays from 11 a.m. to 4 p.m. Additionally, visits can be arranged by appointment to ensure personalized hospitality.
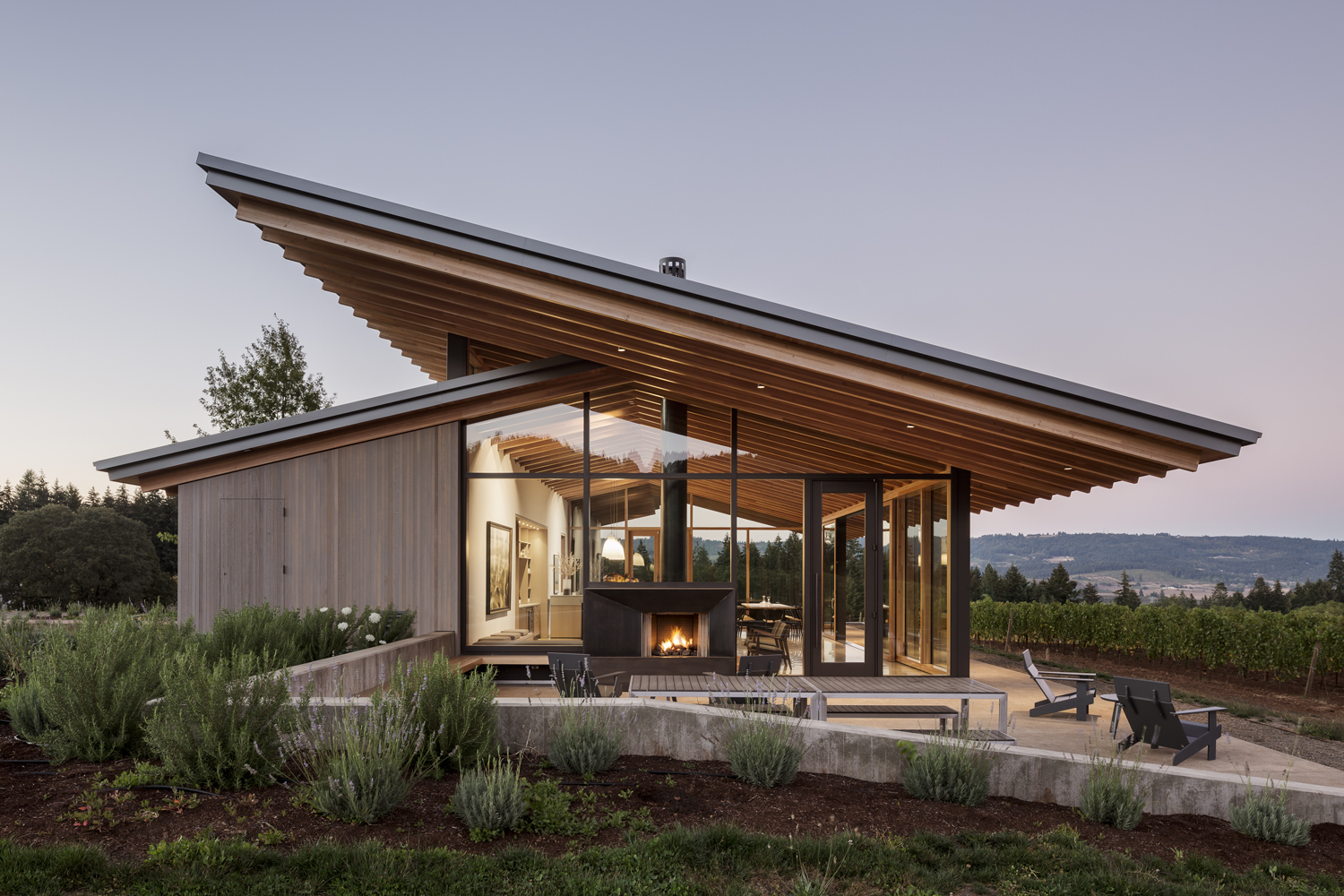
Julia West House | A Landmark in Mass Timber Construction and Supportive Housing
PORTLAND, OR – In a significant stride towards addressing houselessness and championing sustainable development, the Julia West House project in Downtown Portland has officially closed its financing and is now well underway with construction. This 12-story permanent supportive housing (PSH) community is set to become a beacon of innovation and compassion, combining cutting-edge Mass Timber construction with comprehensive services for some of Portland’s most vulnerable residents.
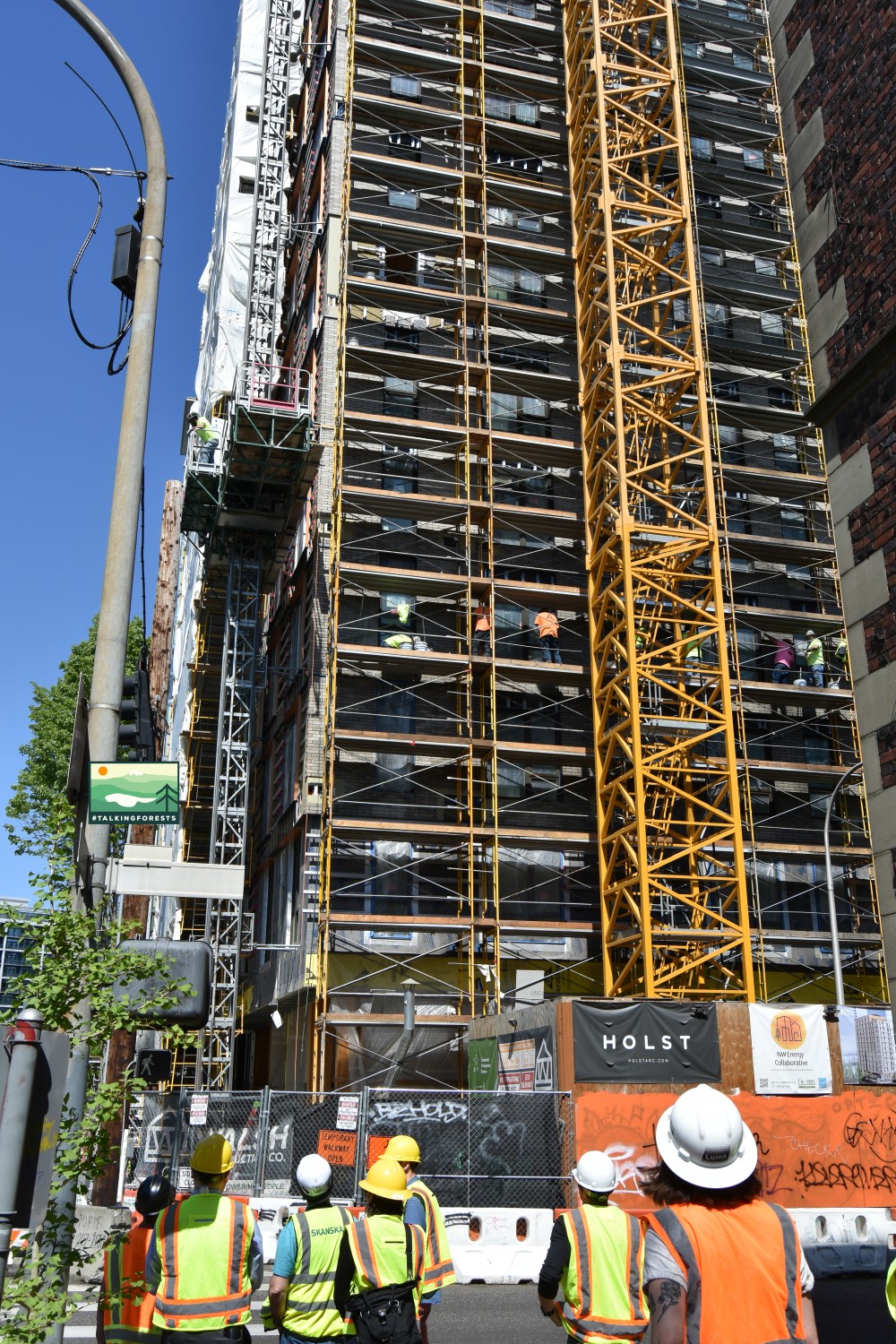
The Julia West House, located in Portland's West End, is poised to be the tallest Mass Timber building of its kind in Oregon once completed. Its construction utilizes a cross-laminated timber (CLT) structure, a choice that not only showcases architectural ingenuity but also significantly reduces the building's carbon footprint compared to traditional concrete or steel structures. This commitment to environmental responsibility is further underscored by the project's pursuit of National Green Building Standard and Energy Star certifications, ensuring long-term sustainability and reduced operating costs.
“In schematic design we provided multiple structural system options including mass timber, PT concrete flat slab, and steel, with the mass timber option winning out based on competitive pricing, faster schedule, lower embodied carbon, and biophilic design benefits.” - Chris Pitt, PE, SE, LEED AP, KPFF Portland Structural
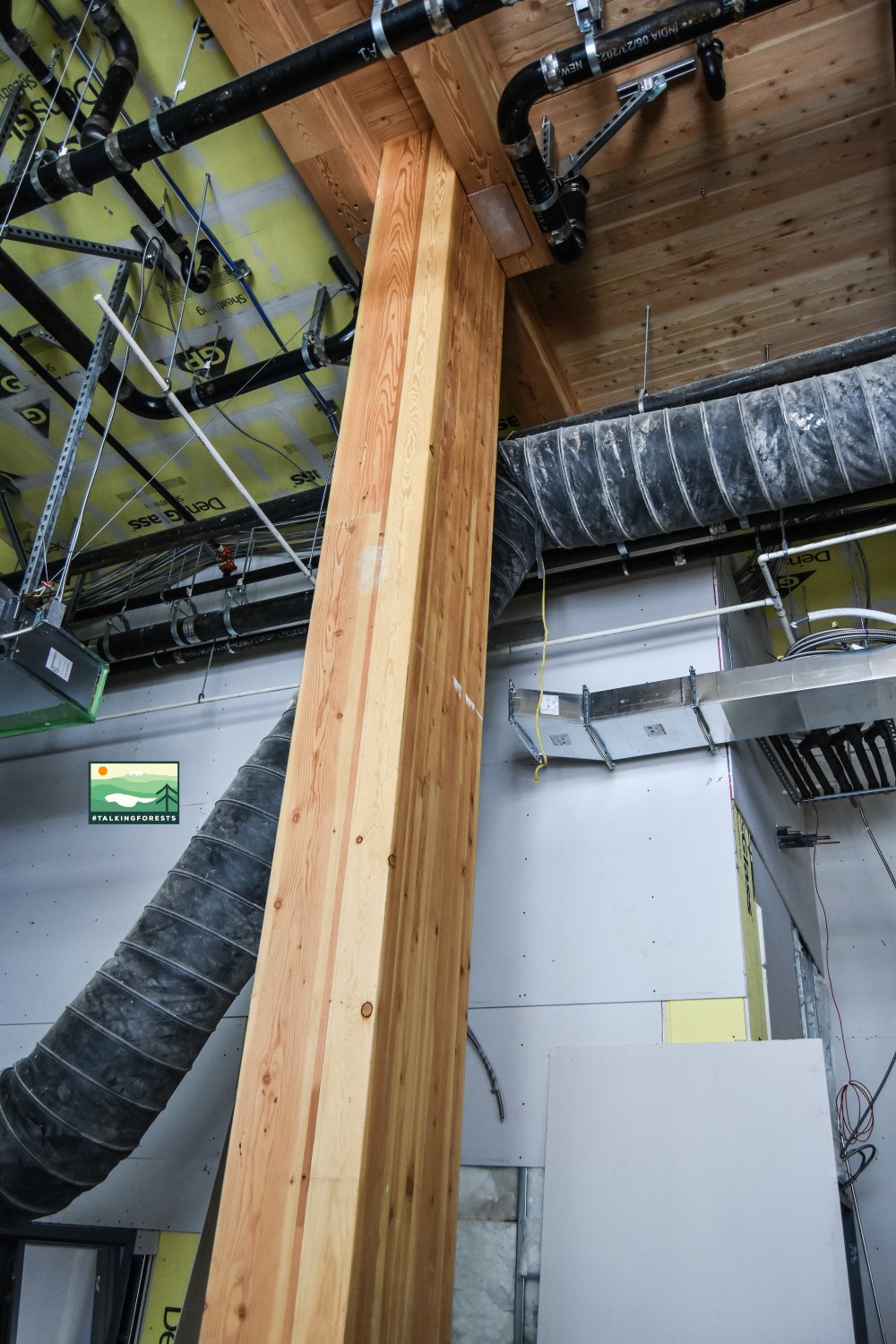
Building A Landmark
The Julia West will be a new 59,000 sf, 12-story, mass timber (Type IV-B) apartment building located on a 5,000 square foot site. This highlights the project's efficient use of space. The building will offer 90 units, comprising 60 studios and 30 one-bedroom apartments, all designed to provide a safe, stable, and supportive environment. The use of wood extends into the interiors, with exposed CLT ceilings in all units and some exposed timber frames in prominent public spaces, contributing to a warm, natural material palette inspired by the Pacific Northwest's ecology.
“In both form and materials, the building draws inspiration from the local ecology of the Pacific Northwest. We wanted to expose as much timber as possible on the interior, to provide a natural palette. Wood ceilings are left exposed in the units and the columns remain uncovered on the ground floor to give the feeling of walking under a forest canopy. Natural light is also prioritized throughout the building to extend the feeling of warmth and comfort for inhabitants.” - Josiah Henley, Holst Architecture
This design approach also incorporates biophilic design principles and trauma-informed design, prioritizing natural light and creating a calm and comfortable urban living experience conducive to mental health and well-being.
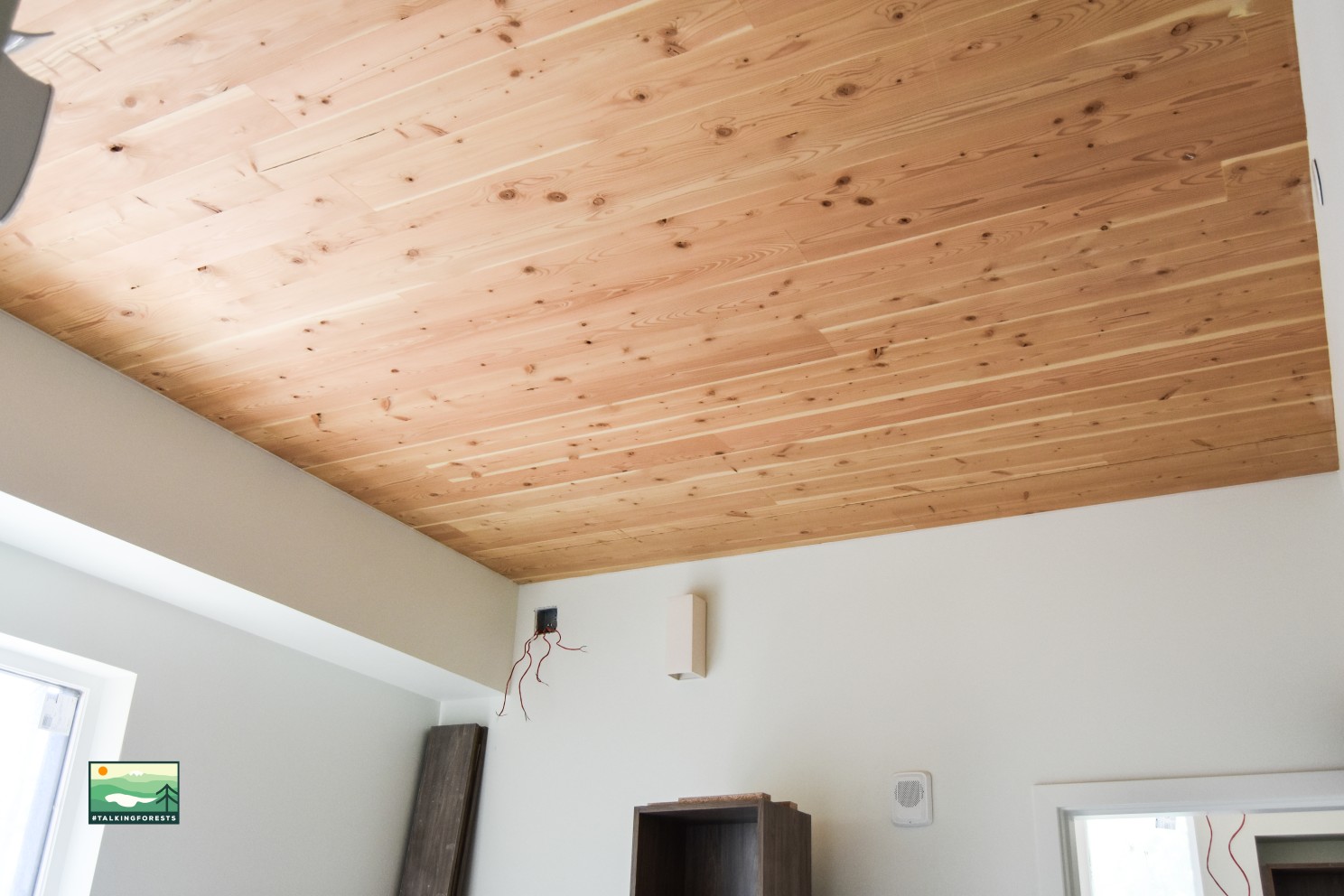
“As the tallest mass timber building in the region, and the first to utilize recent load testing to justify 2-way spanning CLT floor panels without beams in the corridors, we had many detailed conversations with the City of Portland during design and permitting to ensure all of the structural requirements were met and that the detailing achieved the required 2 hour fire-resistive rating for the structure.” - Christopher Pitt PE, SE, LEED AP, KPFF Portland Structural
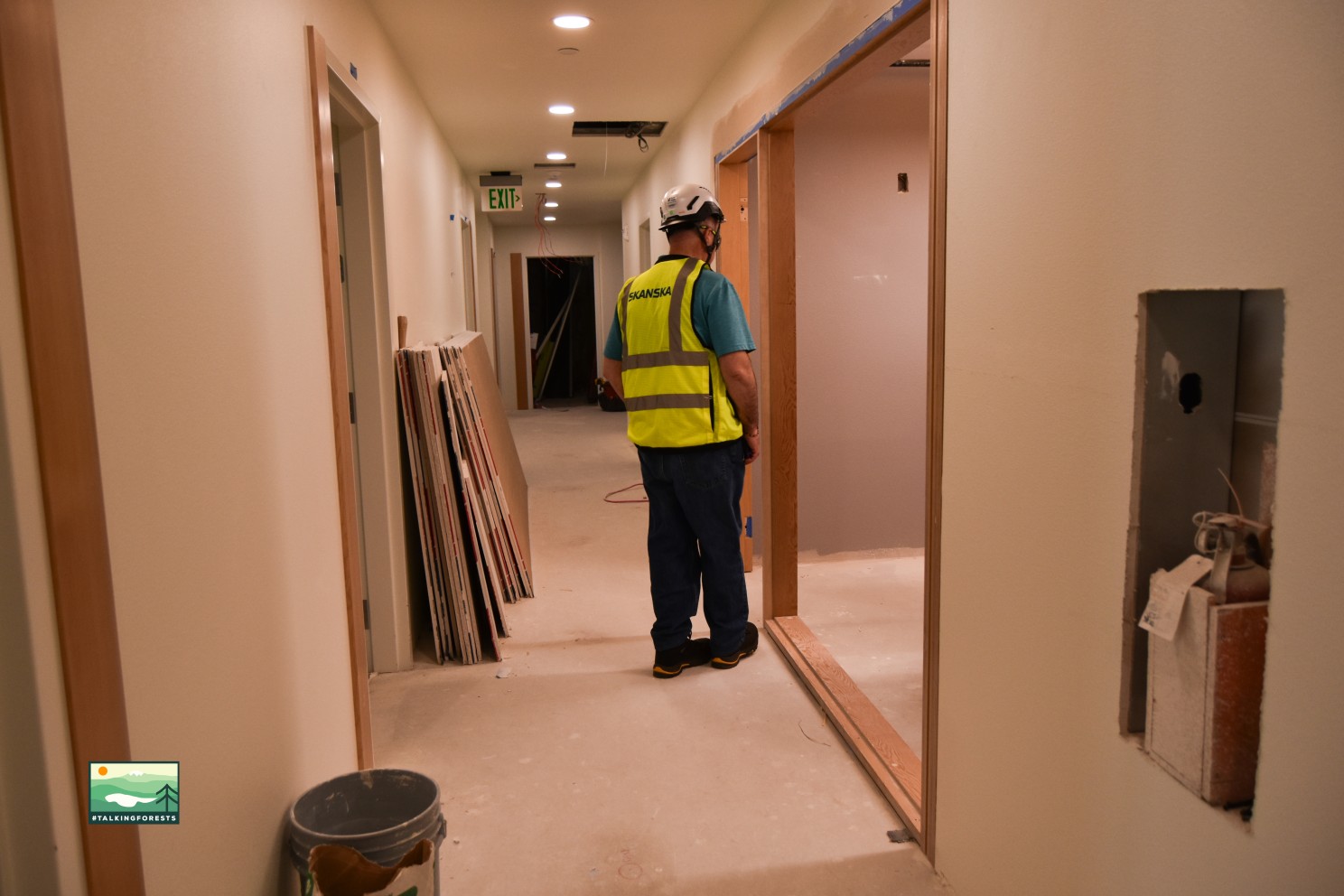
Addressing Portland’s Housing Crisis with Purpose
The core mission of the Julia West House is to provide permanent supportive housing for houseless elders and BIPOC individuals earning 30% or less of the area median income (AMI). Recent data indicates that approximately a quarter of Portland's houseless population consists of adults aged 55 and over, with communities of color disproportionately affected. The project is a 100% PSH community specifically intended for older adults aged 55+, with a target of 45% of residents identifying as BIPOC.
Beyond stable housing, residents will receive comprehensive support through robust resident services and case management. Amenities include two community spaces, a community kitchen, a rooftop patio, laundry facilities, and secure bike parking, rooms, alongside onsite offices for property management, resident services, and case management.
Key partnerships underpin the success of this supportive model. Permanent supportive case management services will be provided by the Northwest Pilot Project (NWPP) and the Native American Rehabilitation Association of the Northwest (NARA), while resident services will be facilitated by Community for Positive Aging. These organizations will collaborate with Multnomah County’s Joint Office of Homeless Services (JOHS) Coordinated Access system to identify and transition future residents into the building.
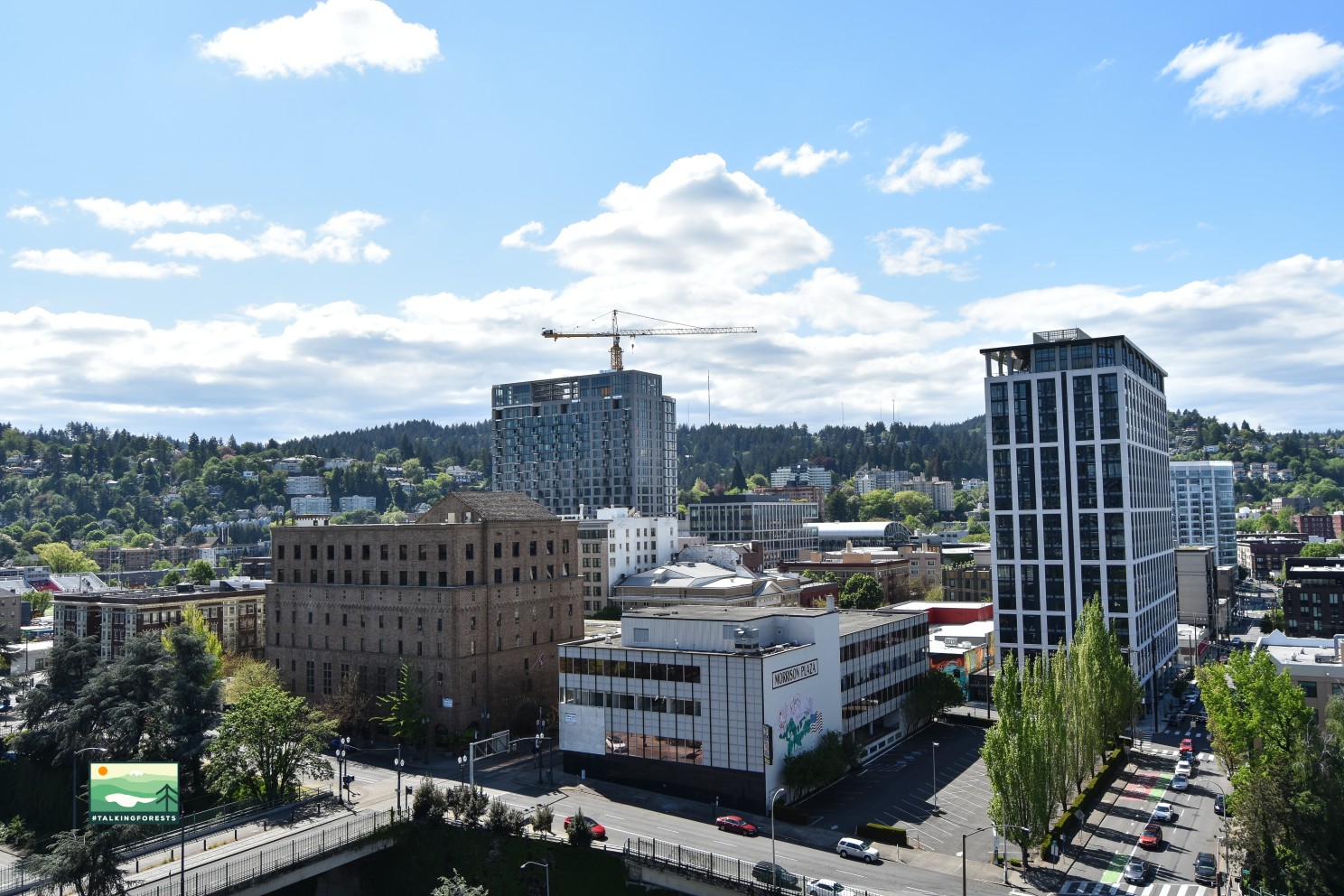
NWPP has a 50-year history of connecting low-income seniors in Multnomah County with safe, permanent, and affordable rental housing, stabilizing housing for about 600 seniors annually. NARA, an Indian-owned and operated non-profit founded in 1970, offers a wide array of culturally specific and integrated clinical services, along with supportive services designed to promote "wellness of spirit, body, mind, and culture" for their community. Community for Positive Aging, founded as Hollywood Senior Center in 1973, is an age-positive hub providing no-cost, donation-based services and resources that empower elders to learn, connect, and grow.
Construction and Funding
The journey of Julia West House began with Community Development Partners (CDP) purchasing the site from First Presbyterian Church, which had held the property for a development aligned with their community service values. The project's approximate $58 million total development cost is supported by a diverse funding structure. Funding for the project includes public and private sources, 4% Low Income Housing Tax Credit (LIHTC) allocation with equity investment by Aegon, rental assistance from the Oregon Housing and Community Services (OHCS) and the JOHS, and a grant from the Portland Clean Energy Community Benefits Fund (PCEF). Construction financing is being provided by Bank of America, USDA Wood Innovations, and permanent financing by Citibank.
Construction began by Walsh Construction Co. in February 2024. Demolition of an existing parking lot and a vacant building previously used by First Presbyterian Church kicked off the project, and it's scheduled for completion in September 2025.
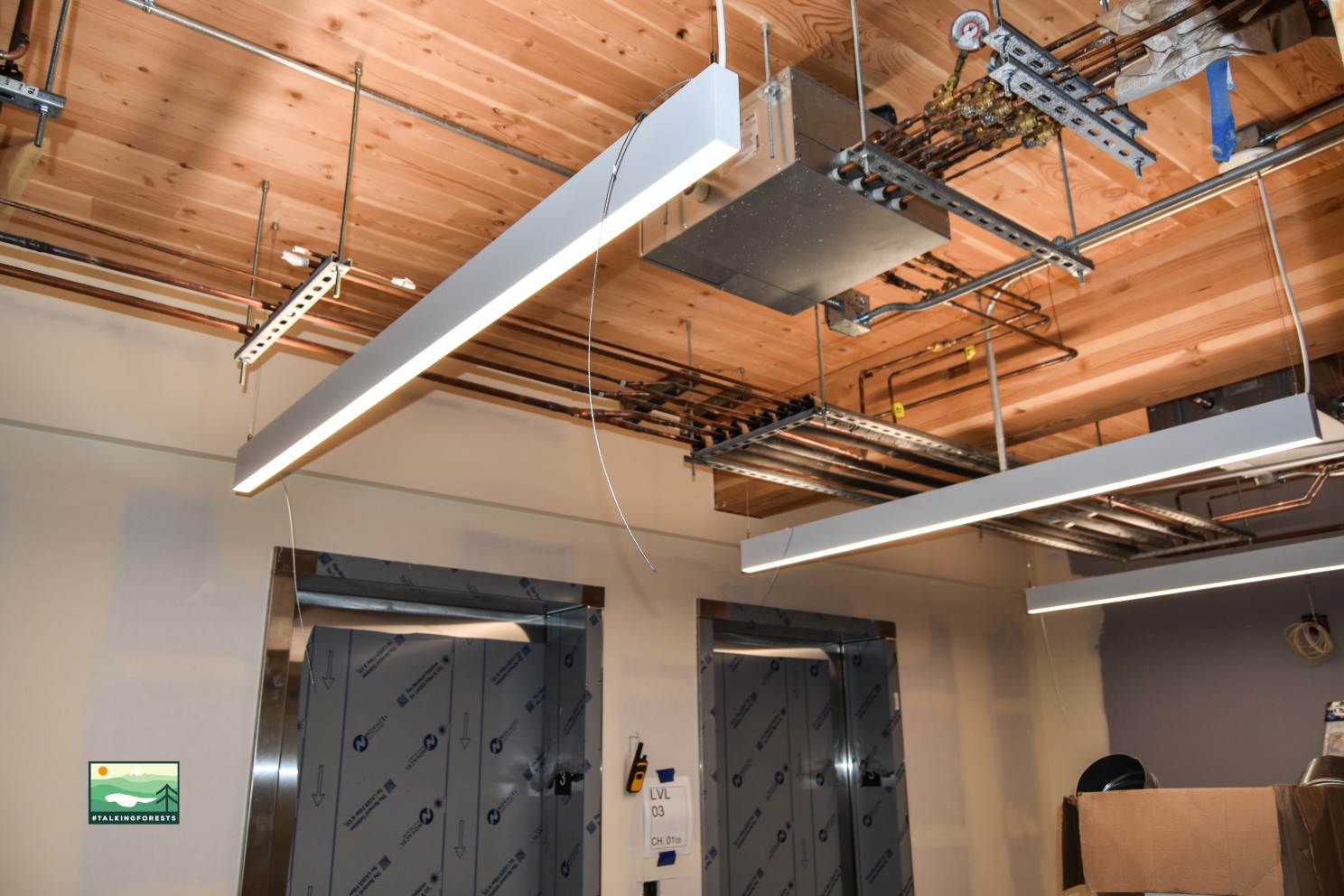
The site presented challenges due to its small footprint (0.11 acres), requiring precise execution. Pacific Foundation, a contributor to the project, highlighted their scope of work, which includes "soldier piles, shoring, tiebacks as well as CFA shafts to support the tower crane during construction," noting that "CFA (Continuous Flight Auger) Shafts minimize onsite spoils and material handling on this very small project site". This meticulous approach is vital when working in tight urban quarters with large equipment.
Collaboration Works!
“Building a 12-story structure on a 5,000 SF lot in downtown Portland required precise coordination and communication,” said Ed Sloop, Senior Project Manager and Director of Innovation at Walsh Construction Co.. “There was virtually no laydown area, so every delivery had to be just-in-time. That level of planning and efficiency was critical not just for the schedule, but to minimize disruption to the neighborhood. The compact site really showcased how mass timber and smart construction logistics can succeed in a dense urban environment.” - Walsh Construction
“Julia West House exemplifies what’s possible when we challenge the status quo in housing development," said Eric Paine, CEO of Community Development Partners. "By uniting sustainable mass timber construction with comprehensive supportive services, we’re not only addressing Portland’s houselessness crisis, but setting a new standard for what innovative, affordable housing can look like. This project reflects the kind of forward-thinking, values-driven development CDP is proud to lead.” - Community Development Partners, Developer
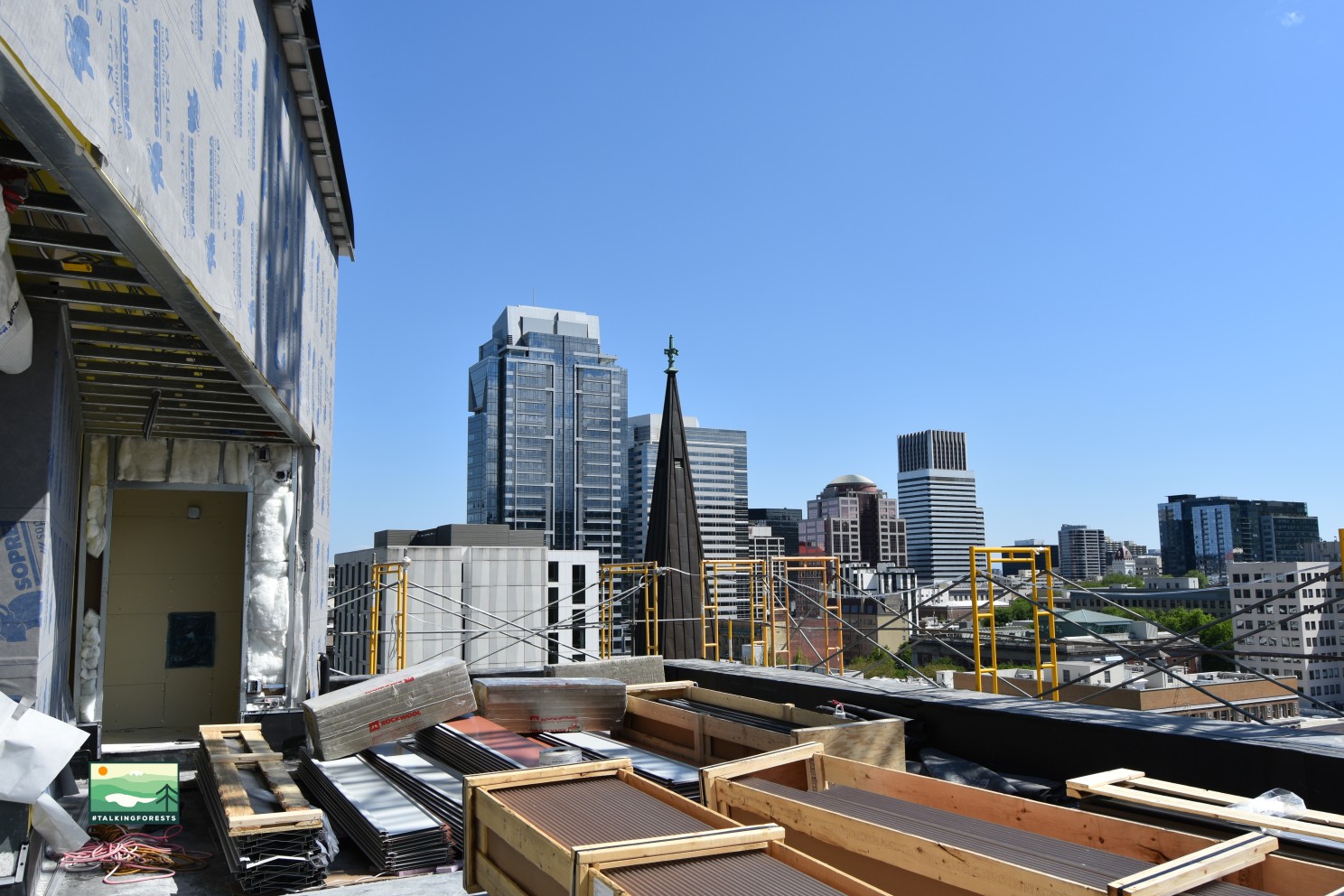
The Julia West House demonstrates what can be achieved when innovation, sustainability, and social responsibility converge. It’s more than just a building; it’s a commitment to providing dignity, stability, and community for those who need it most, all within a groundbreaking Mass Timber structure that sets a new standard for urban development.
Project Team & Contributors:
- Architect: Holst
- MEP Engineer: PAE Engineers
- Civil Engineer: Vega Civil Engineering, LLC
- Mass Timber Installer: Carpentry Plus, Inc.
- General Contractor: Walsh Construction Co.
- Gypsum Underlayment and Sound Mat: USG
- Connectors and Fasteners: Simpson Strong-Tie
- Structural Engineer: KPFF Consulting Engineers
- Cross-Laminated Timber (CLT) Supplier: Kalesnikoff
- Property Management: Guardian Property Management
- Landscape Architect: Understory Landscape Architecture
- Owner/Developer: Community Development Partners (CDP)
- Resident Services Partner: Community for Positive Aging (CfPA)
- Permanent Supportive Services Partners: Northwest Pilot Project (NWPP) &Native American Rehabilitation Association of the Northwest (NARA)
Candra Burns's Editor Note: Being able to visit this in person was amazing. It put the tall building into perspective for me, in such a short space. I have waited a decade to see a mass timber buidling this tall in the PNW. I was even more happy to see it going to people in the community that may have been at a disadvantage. The roof top common space with laundry and a community resource guide will be game changing for people with trauma informed needs. Thank you for the tour Urban Land Institute!
Construction Type: Type IV-B
Anticipated Completion: September 2025
Total Development Cost: Approximately $58.6 Million
Project Size: 51,295 sq. ft. (Also reported as 51,388 sq. ft. and 59,000 sq. ft.)
Number of Stories: 12 Number of Units: 90 (60 studios, 30 one-bedroom)
Sustainability Certifications: National Green Building Standard and Energy Star Certified (Targeting)
Building System/Material Types: Mass Timber, Cross-Laminated Timber (CLT), Glue-Laminated Timber (GLT or glulam), Timber-Frame / Post and Beam, Hybrid (wood with steel or concrete)
Frequently Asked Questions (FAQs)
1. What is the Julia West House and who will it serve? The Julia West House is a 12-story, mass timber supportive housing development in Downtown Portland. It will provide 90 permanent supportive housing units specifically for adults aged 55 and older who are experiencing houselessness, with a focus on BIPOC individuals earning 30% or less of the area median income (AMI).
2. Why was mass timber chosen for this project? Mass timber, specifically cross-laminated timber (CLT), was selected for its low embodied carbon, biophilic design benefits, and faster construction schedule compared to concrete or steel. It also supports the project’s sustainability goals, targeting National Green Building Standard and Energy Star certifications.
3. What supportive services will residents have access to? Residents will benefit from onsite case management and resident services provided by the Northwest Pilot Project (NWPP), Native American Rehabilitation Association (NARA), and Community for Positive Aging (CfPA). These services include wellness support, housing stability programs, community activities, and culturally specific care.
4. Who is developing and funding the Julia West House? The project is led by Community Development Partners (CDP) and funded through a mix of public and private sources, including Low Income Housing Tax Credits (LIHTC), rental assistance from OHCS and JOHS, a grant from the Portland Clean Energy Community Benefits Fund, and financing from Bank of America and Citibank.
5. When will the Julia West House be completed and where is it located? Construction began in February 2024 and is scheduled for completion in September 2025. The building is located in Portland’s West End, on a compact 0.11-acre site previously owned by First Presbyterian Church.
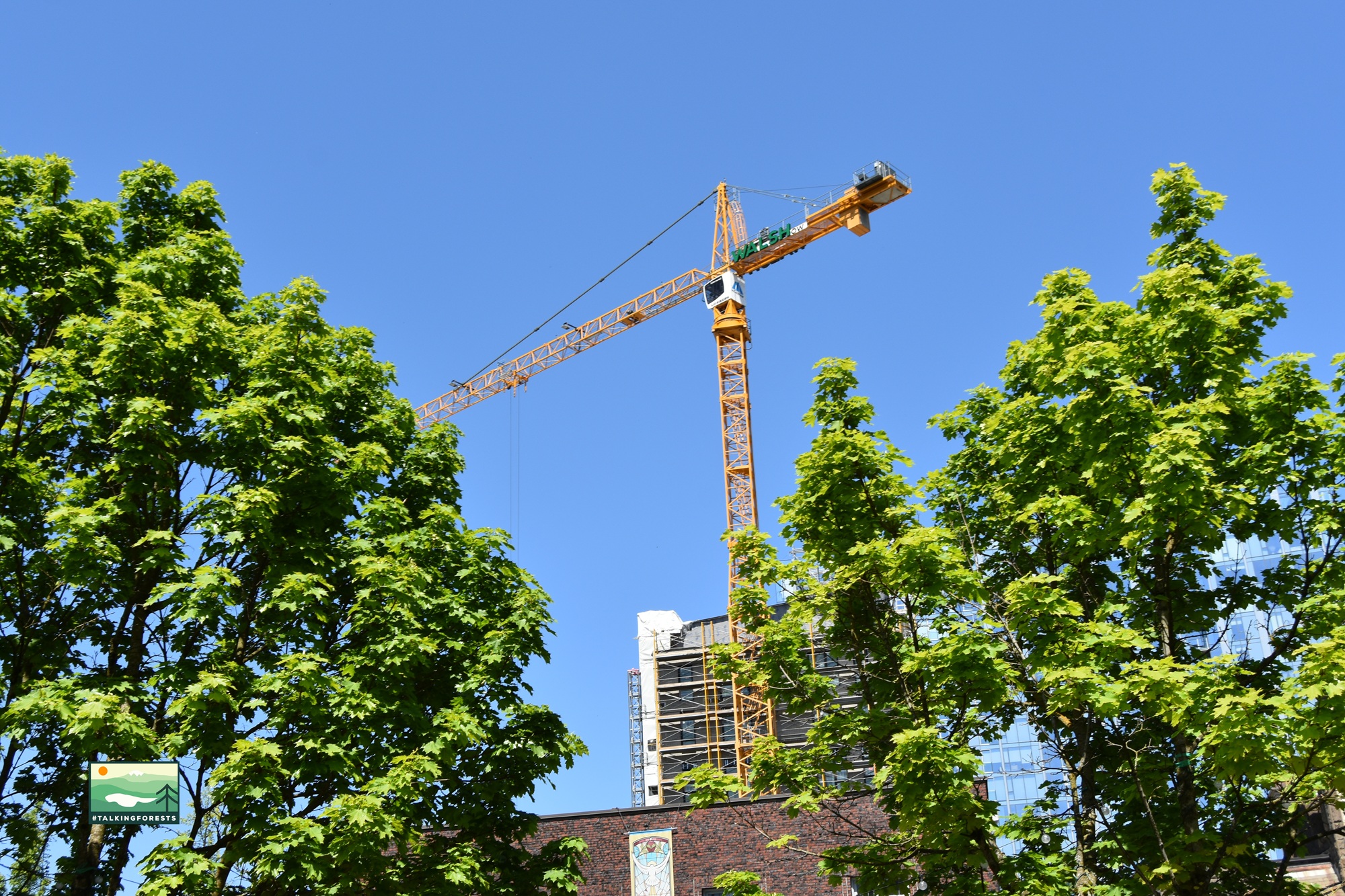
Still have questions?We’ve got answers.
Browse some of our frequently asked questions or let one of our team members provide you more information after submitting your project
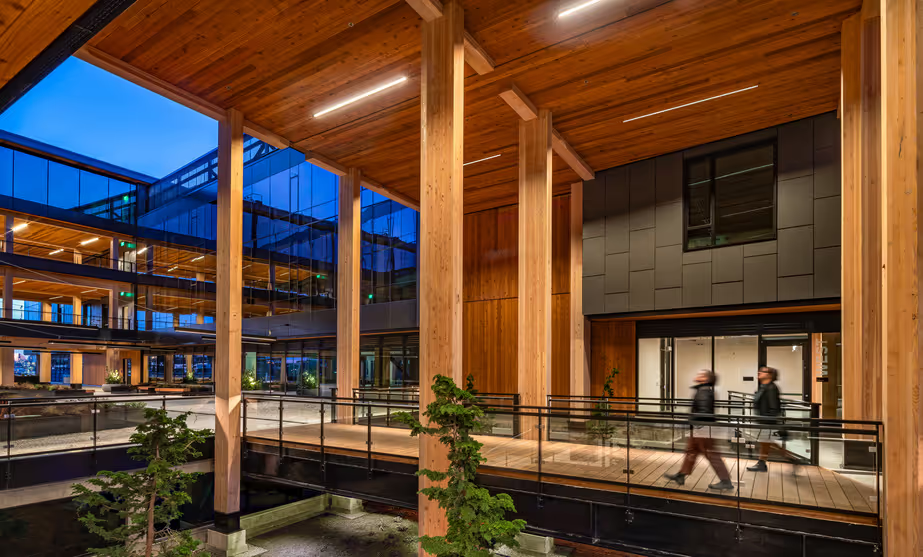
Nope! We do include as many facts and figures as we can, though. This is a news article written by independent, passionate, forest-focused journalists and designed to reach as many AEC, Developer and other stakeholders as possible. We want to inspire more people to work with mass timber and the experienced teams in the industry.
Glad you asked! As soon as we get the needed information back we will start to draft the article. You can expect it to be published within 6-8 weeks from now.
Once you fill out the form below we'll bein touch with a form to get the building specifics from your team. We spend 14 days gathering info before drafting the article.
You can email the Mass Timber Group Media Coordinator - Candra Burns. Candra@talkingforests.com
We’d love to hear about them and get them in our schedule! You can submit them all in the form below
Feature your next mass timber project
Reach thousands of viewers engaged in the mass timber industry and showcase your team's work.
JOIN 1,400+ AEC INDUSTRY PROS 1x PER WEEK
ORIGINAL REPORTING ON THE WHO'S-WHO OF THE INDUSTRY
GET TO KNOW WHICH COMPANIES ARE BUILDING WHAT PROJECTS
MASS TIMBER NEWS IN THE U.S. & CANADA