Level up your mass timber IQ & stay up-to-date on industry trends
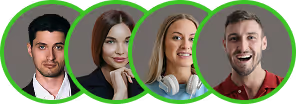
Have you ever walked through a building and felt an undeniable connection to the natural world? That's the feeling The Hive project in Vancouver, British Columbia, aims to capture and, indeed, amplify. This isn't just another office building; it's a groundbreaking 10-story mass-timber structure, standing as North America's tallest timber-braced frame building, pushing the boundaries of what's possible in modern construction, especially in a high seismic zone like Vancouver.
The Hive, located at 2150 Keith Drive in Vancouver's False Creek Flats neighborhood, is an office building designed for a unique client. Originally envisioned as a company headquarters, the anchor tenant plan shifted during the pandemic, leading to ICBC ultimately leasing the entire 164,000 sq ft of office space. The project's design mandate from the start was the use of mass timber. It totals 15,096 m² (162,491 ft²).
The design team, including DIALOG and Fast + Epp, the structural engineer, didn't settle for the typical concrete core approach often seen in taller mass timber buildings. Instead, they pursued a unique structural system. Above the level two concrete base, which deals with the sloping site and houses back-of-house facilities, the building utilizes an all-wood gravity and lateral system. This innovative lateral system features a perimeter timber braced frame system combined with four discrete internal CLT shear walls. The timber-braced frame creates a striking façade expression and eliminates the need for conventional cast-in-place concrete cores, reducing the building's environmental impact.
Designing in a high seismic zone presented a significant challenge. Robert Jackson, Principal at Fast + Epp, noted that building a 10-story mass timber structure in such an area hadn't been done extensively before. Fast + Epp, considered leaders in the space with deep expertise, were immensely grateful to be involved. Their creative design led to exploring different lateral system options, eventually settling on the perimeter braced frames and CLT shear walls.
To address the seismic demands, the design team incorporated Tectonus supplementary energy dissipating devices at each braced frame member and within the CLT shear walls. These devices act like springs, dissipating force during an earthquake. Ryan McClanaghan, the project architect with Dialog, noted that these devices were identified as a pathway to achieve the necessary structural values when early design thinking wasn't quite getting there.
They took the building "from seismically acceptable to seismically resilient," performing "well above" what code requires in a high earthquake zone. The design employed perforated plate technology where energy dissipates within the frame members and shear walls.
Extensive testing was crucial for validating this approach. The timber-braced frame and CLT shear wall systems underwent small-scale and full-scale testing at the University of Alberta and the University of Queens, providing valuable engineering information for future projects. This testing program was supported by innovation funding from the Canadian government through the Green Construction Through Wood (GCWood) Program, as well as the province of British Columbia through the Mass Timber Demonstration Program (MTDP). This governmental support means the learned information will be shared, contributing to an open-source philosophy that helps the industry improve together. Additionally, testing was done on the Megant concealed beam hangers to ensure their rotational capacity could withstand movement in a seismic event.
The building's distinctive honeycomb shape on the exterior is a direct reflection of this structural system. The diagonally oriented glulam braces create a cellular pattern. What's fascinating is how this structural expression was integrated with the building's aesthetic and function. The client desired access to outdoor space and fresh air, so the team took the unique geometry of the façade and extruded it into a network of balconies that cascade along the east, south, and west faces. These balconies are located between the brace bays, offering alternating outdoor spaces on each floor. Stepping out onto them, you feel sheltered and enveloped by the warm, exposed wood surfaces, creating a space you'd genuinely want to spend time in.
Building these balconies on a mass timber structure presented its own set of challenges. As Ryan McClanaghan explained, you can't just cantilever a CLT slab in the traditional way and make the buildup work. The mindset shift required in mass timber design involves anticipating construction and understanding how different criteria interact. The solution for The Hive's balconies involved a multi-step process informed by the pre-construction team. HSS stubouts extend through the unitized curtain wall system, allowing the prefabbed balconies to be bolted on from the outside. These balconies consist of steel outriggers with CLT panels doing the structural work. To manage drainage and create a flush surface with the interior floor, the balcony structure is dropped slightly lower than the main floor finish. Importantly, the outside wood structure is treated as its own separate element from the inside, with a good envelope break between the two.
This kit-of-parts prefabrication approach was fundamental to facilitating rapid on-site construction. Jonathan Leder, Construction Director at Supreme Steel, the subcontractor for mass timber and steel erection, shared his experience:
"This was Supreme’s first time working with mass timber—and we jumped right into one of the more complex buildings to construct. What really stood out was how efficient the process was. This was a challenging building throughout and utilizing Local 97's resources and having a few team members with mass timber training from BCIT, Supreme was able to accomplish the tasks large or small. Another interesting aspect was the site stayed incredibly clean and organized throughout. It was a great introduction to the potential of mass timber."
Even the roofing for the balconies was done offsite in a warehouse, contributing to a rapid installation time from the Supreme team in just 14 days.
Since this was Supreme’s first mass timber build - they teamed up with MTC Solutions, who provided the rigging devices, beam hangers, and structural screws used in the project, to get their team up to speed quickly on the nuances.
MTC’s Eleonora Dalfavo noted, “We offered a customized training to have the team work with confidence with the new material,"underscoring the importance of education and collaboration needed to succeed in the industry.
The project prioritizes sustainability, aligning with the owners', Arran and Ratan Stephens', mantra of sustainability and environmental stewardship.
The Hive is targeting a minimum LEED Gold certification. It features 100% electric mechanical systems, natural thermal insulators, and a biophilic design for the interior spaces. Plus, eliminating the concrete core in lieu of mass timber contributes to a reduced environmental impact.
Ryan McClanaghan emphasized the use of Life Cycle Analysis (LCA) not just for reporting, but as a design tool to make good choices. It helped the team realize where the significant carbon impact lies in a tall timber structure – largely in the floor plates. He also shared a compelling analogy often used to communicate the sustainability story: using the Canadian Wood Council app to show how quickly North American forests can regrow the volume of mass timber used in the building. The idea that a 10-story, 164,000 sq ft building could be "grown" in under an hour is a powerful way to convey the material's renewability.
Ryan emphasized the collaborative spirit required for mass timber projects, where the design, owner, and construction teams must work together to solve problems. He believes this collective team problem-solving is irreplaceable. Sharing knowledge and giving credit to the entire project team, from designers to suppliers and trades, is crucial. As Eleonora Dalfovo from MTC Solutions put it, The Hive has "naturally caught a lot of attention", becoming a notable landmark in the city.
The Hive is expected to reach completion later in 2025. ICBC will take possession then, with staff expected to begin using the office space in early 2027 after interior configuration. The location adjacent to SkyTrain's VCC-Clark Station is highly optimal, and its accessibility will improve significantly with the Broadway extension completion in 2027.
In summary, The Hive is a pioneering mass timber project that demonstrates how innovative design and collaborative problem-solving can overcome complex challenges, particularly in seismic regions. By utilizing a unique perimeter timber braced frame and CLT shear wall system, incorporating advanced seismic dampeners validated through extensive testing, and designing prefabbed balcony elements, the team has created a seismically resilient, highly sustainable, and visually striking building. The project serves as a valuable case study for the evolving mass timber industry, highlighting the potential for hybrid timber structures and the importance of cross-disciplinary collaboration and knowledge sharing.
It embodies the idea of making the "revolution irresistible" by building beautiful, sustainable spaces that inspire.
Frequently Asked Questions (FAQ's)
Lead mass timber projects with confidence — and leave delays, redesigns, and budget blowups behind.
✅ Solve early-stage design, sourcing, insurance, permitting, code & cost hurdles before they derail your project.
✅ Find technical answers on design, detailing, procurement, embodied carbon ROI, hybrid systems & more.
✅ Build relationships with developers, GCs, architects, and engineers shaping mass timber’s future.
Get your ticket— and get the insights, skills, and network to deliver mass timber projects successfully.