This 10-Story Timber Build Broke the Rules—The Hive w/Ryan McClanaghan
If you had asked a room of architects a decade ago whether a 10-story timber building could stand tall in a seismic hotspot, most would have dismissed the idea as fanciful—if not outright reckless. Yet today, Vancouver’s Hive rises as a striking counterpoint, its honeycomb exoskeleton and timber braced frame system challenging both convention and gravity. What changed? And how did a material once relegated to low-rise construction become the centerpiece of one of North America’s most ambitious urban projects?
For Ryan McClanaghan of DIALOG , the answer is as much about community as it is about engineering. “There’s something about this material and this way of thinking about a project that really captured my imagination,” he recalls of his early exposure to mass timber in Europe. That initial spark—fueled by open collaboration and a willingness to rethink the fundamentals—set him on a path from novice to innovator, culminating in a project that demonstrates what can happen when design, sustainability, and resilience converge.
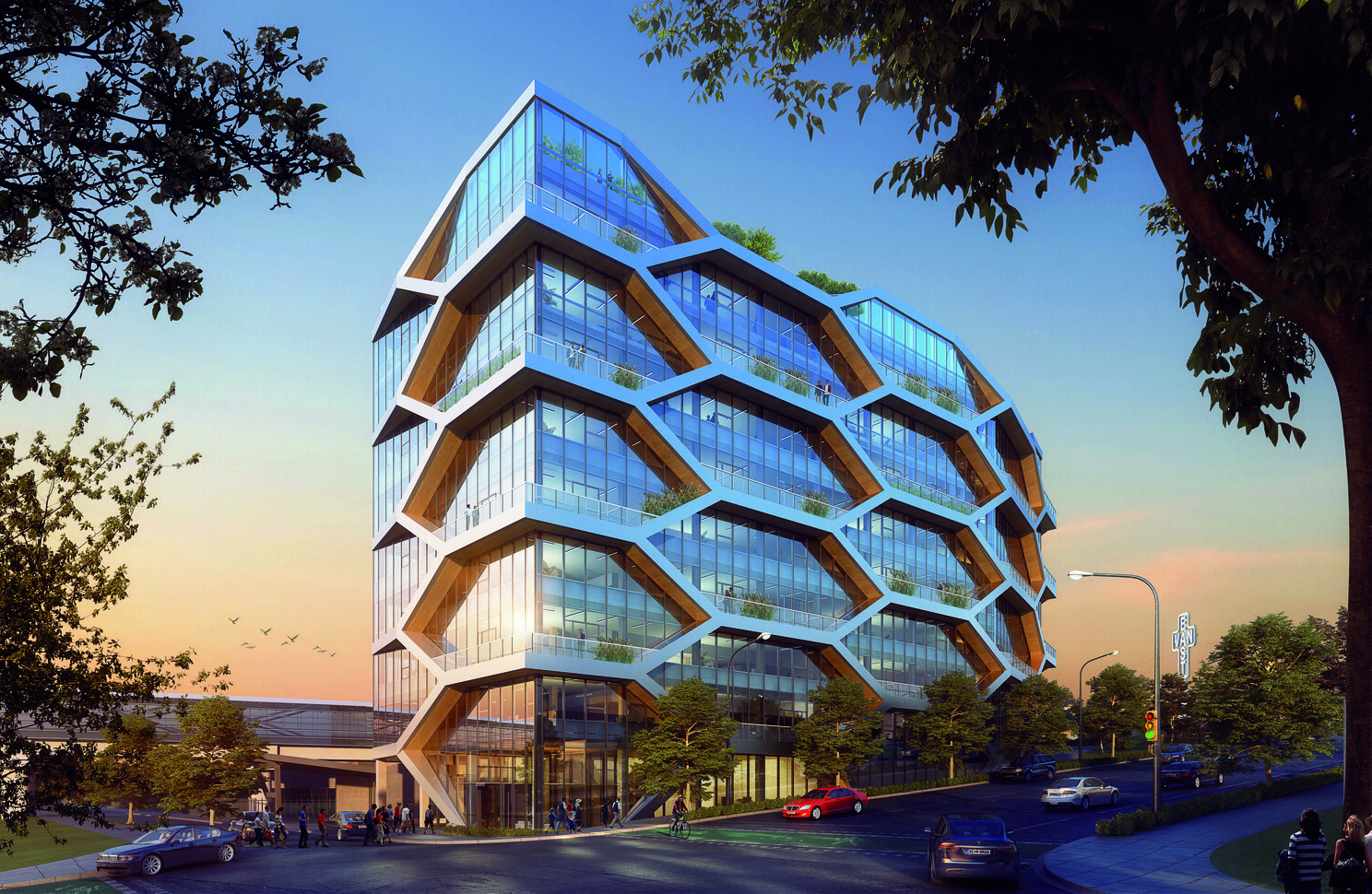
From Novice to Innovator: Ryan McClanaghan's Journey into Mass Timber
A single encounter with a new material can redirect an entire career. For Ryan McClanaghan, that moment arrived during his studies at the University of Toronto, where early exposure to mass timber set the stage for a transformative path. His formative work term in Berlin, immersed in the European timber scene, catalyzed a fascination that would later position him as a leader in North American mass timber design with The Hive.
“There’s something about this material and this way of thinking about a project that really captured my imagination.” Ryan’s early intrigue was fueled by witnessing projects like a mass timber office building in Helsinki—examples that demonstrated both the technical and cultural momentum of timber in Europe. Returning to Canada with Dialogue, his growing expertise soon converged with the opportunity to lead the design of The Hive.
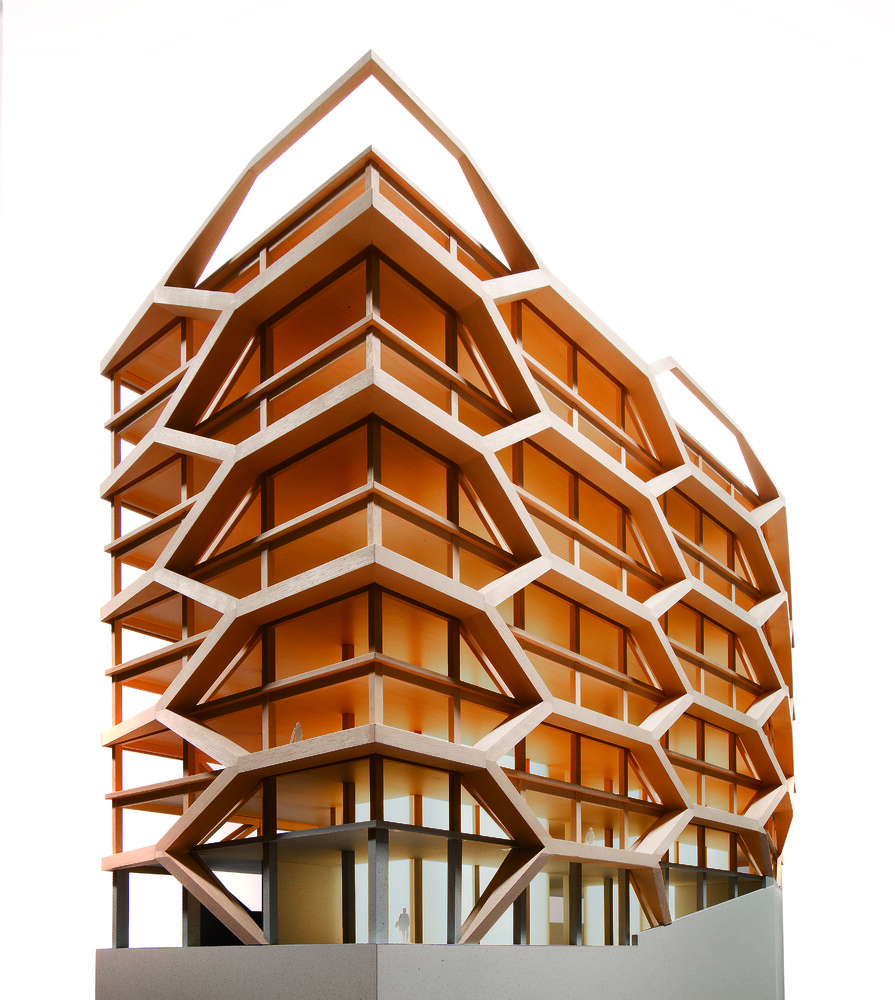
Rethinking Structure: The Hive’s Perimeter-Driven Timber System
Few North American projects have so thoroughly reimagined the structural logic of mass timber as The Hive. Rather than defaulting to a concrete core, the design team shifted the primary structural elements to the building’s perimeter, unlocking new architectural and engineering possibilities.
“What if we did an all-wood structure above L2?” This question reframed the project’s ambitions, resulting in a 10-story Vancouver building whose cellular exoskeleton and timber braced frame system serve both as expressive façade and as the backbone of its seismic resilience. The integration of timber shear walls and buckling restraint braces demonstrates how mass timber can perform at scale—not just as a material of warmth, but as a robust structural solution.
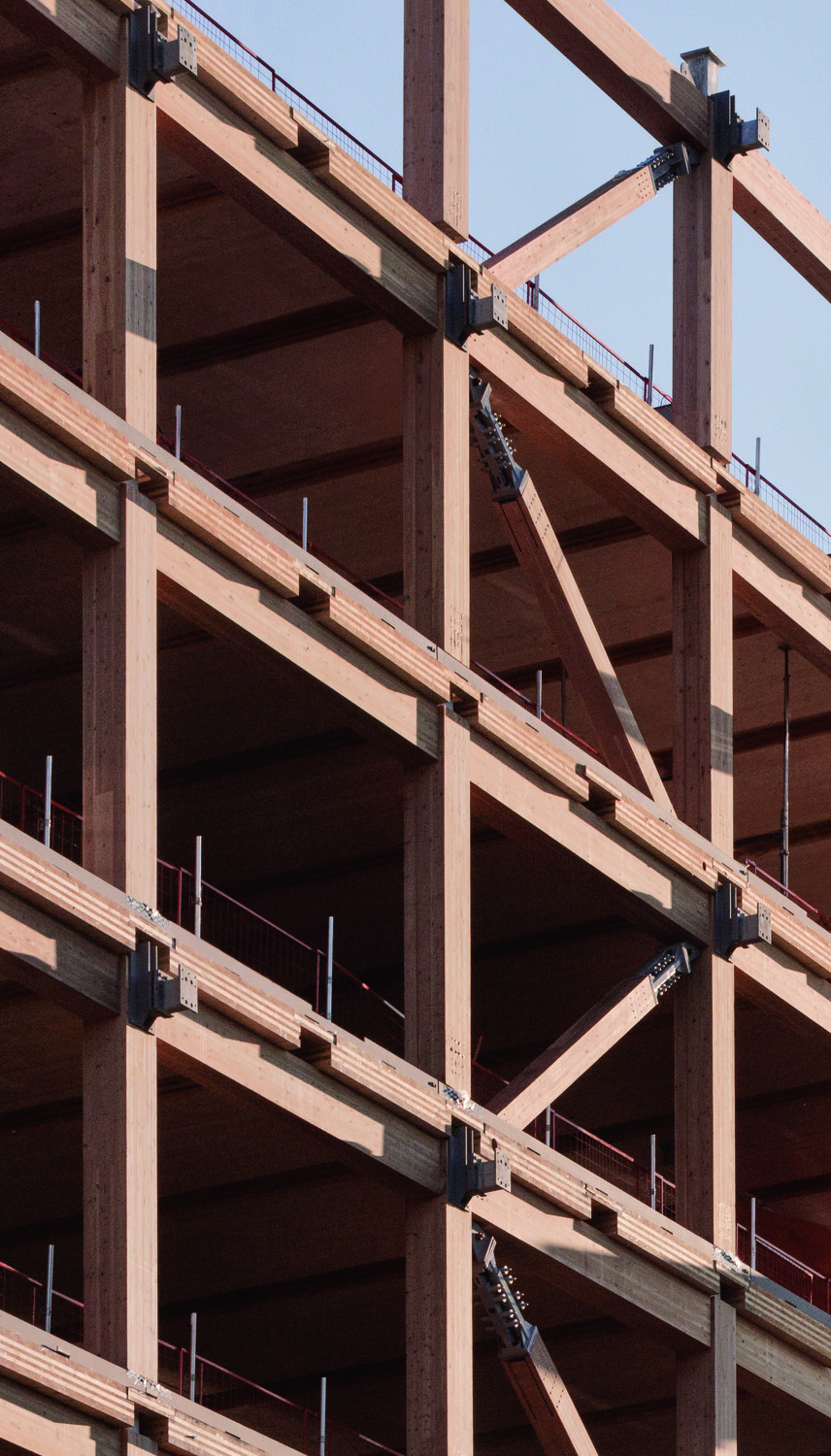
The Hive’s biophilic strategies—from cascading balconies to generous daylighting—are not mere aesthetic gestures. They are embedded in the building’s structural DNA, with the unique geometry of the façade channeling forces efficiently while fostering occupant well-being. As Ryan notes, “The unique geometry of the building facade carries the forces that act on it, creating a harmonious relationship between form and function.”
This perimeter-driven approach set the stage for the project’s next major challenge: seismic performance in a demanding context.
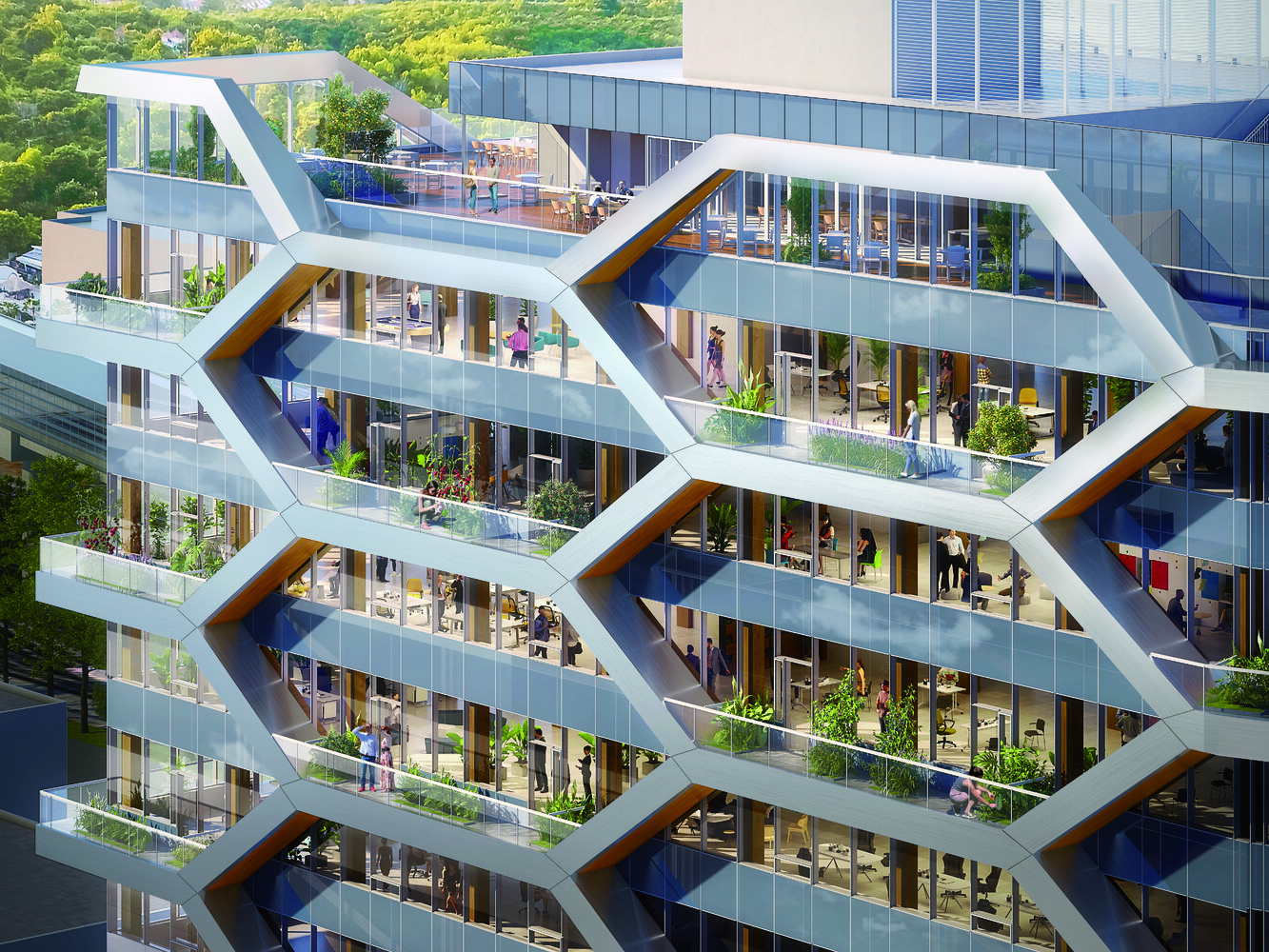
Navigating Seismic Challenges: Engineering Resilience
Vancouver’s seismic profile demands more than conventional solutions, especially for mass timber structures. The Hive’s design team confronted this directly, seeking to minimize concrete use while meeting stringent performance criteria.
“We only wanted to use concrete as much as we needed to get out of the ground.” This guiding principle led to a predominantly timber superstructure above the second level. The team’s close collaboration with structural engineers yielded a lateral system built around timber buckling restraint braces—an approach that satisfied seismic codes and reinforced the building’s architectural identity.
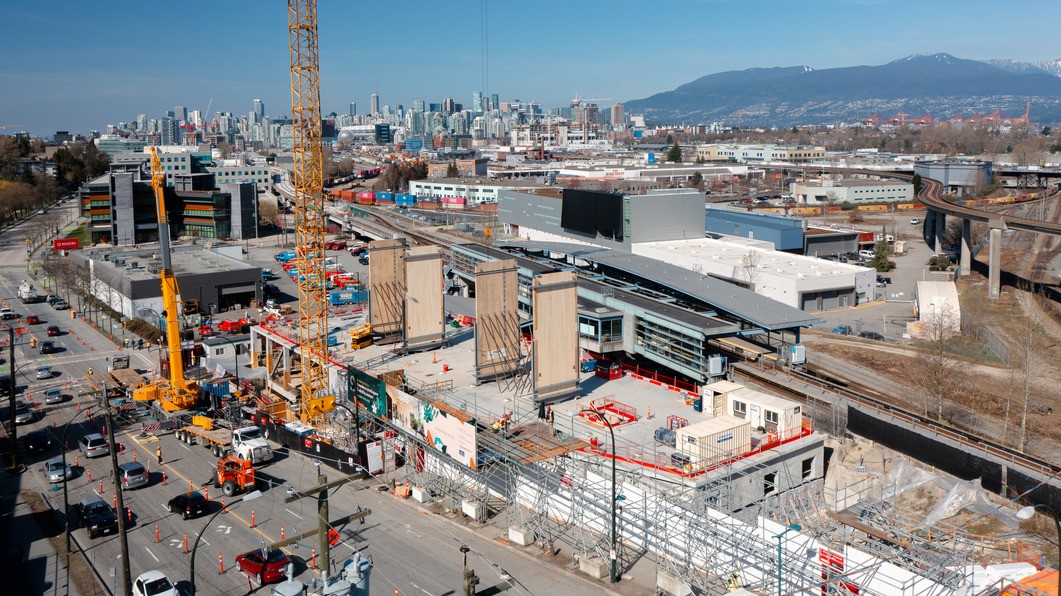
“We are well above what the performance needs to be,” Ryan explains, underscoring the project’s commitment to both safety and technical rigor. The integration of seismic resilience into the building’s visual language exemplifies how engineering and design ambition can reinforce one another.
The complexity of these challenges required a project culture built on trust and shared expertise—a theme that would define the next phase of The Hive’s development.
Collaboration: The Heart of Successful Mass Timber Projects
When technical ambition meets construction reality, the difference between success and failure often lies in the quality of collaboration. The Hive’s progress depended on a tightly integrated team of architects, engineers, and builders, each contributing specialized knowledge to solve unprecedented problems.
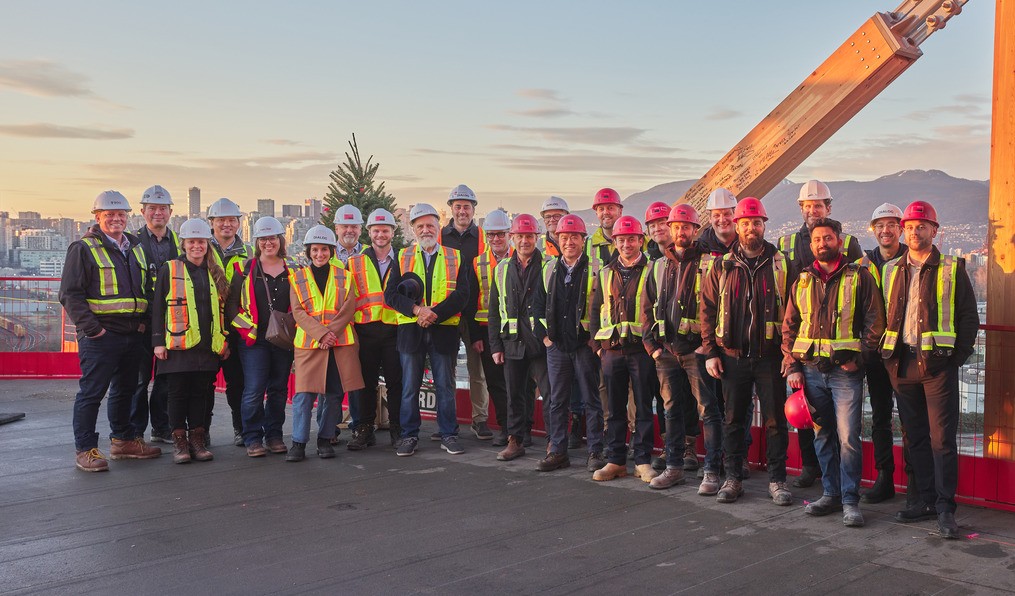
“Teams make projects go,” Ryan emphasizes, reflecting on the necessity of open communication and mutual respect. The project’s unique features—perimeter bracing, exposed timber, and complex connections—demanded iterative problem-solving and a willingness to adapt as new challenges emerged.
“How you solve problems together collaboratively is important,” he notes, highlighting the value of collective intelligence over individual heroics. This ethos extended beyond the core team, as Ryan actively sought input from peers across the industry, reinforcing a culture where knowledge-sharing accelerates progress.
The collaborative momentum built on The Hive would soon propel Ryan into a broader network of mass timber innovators, both locally and abroad.
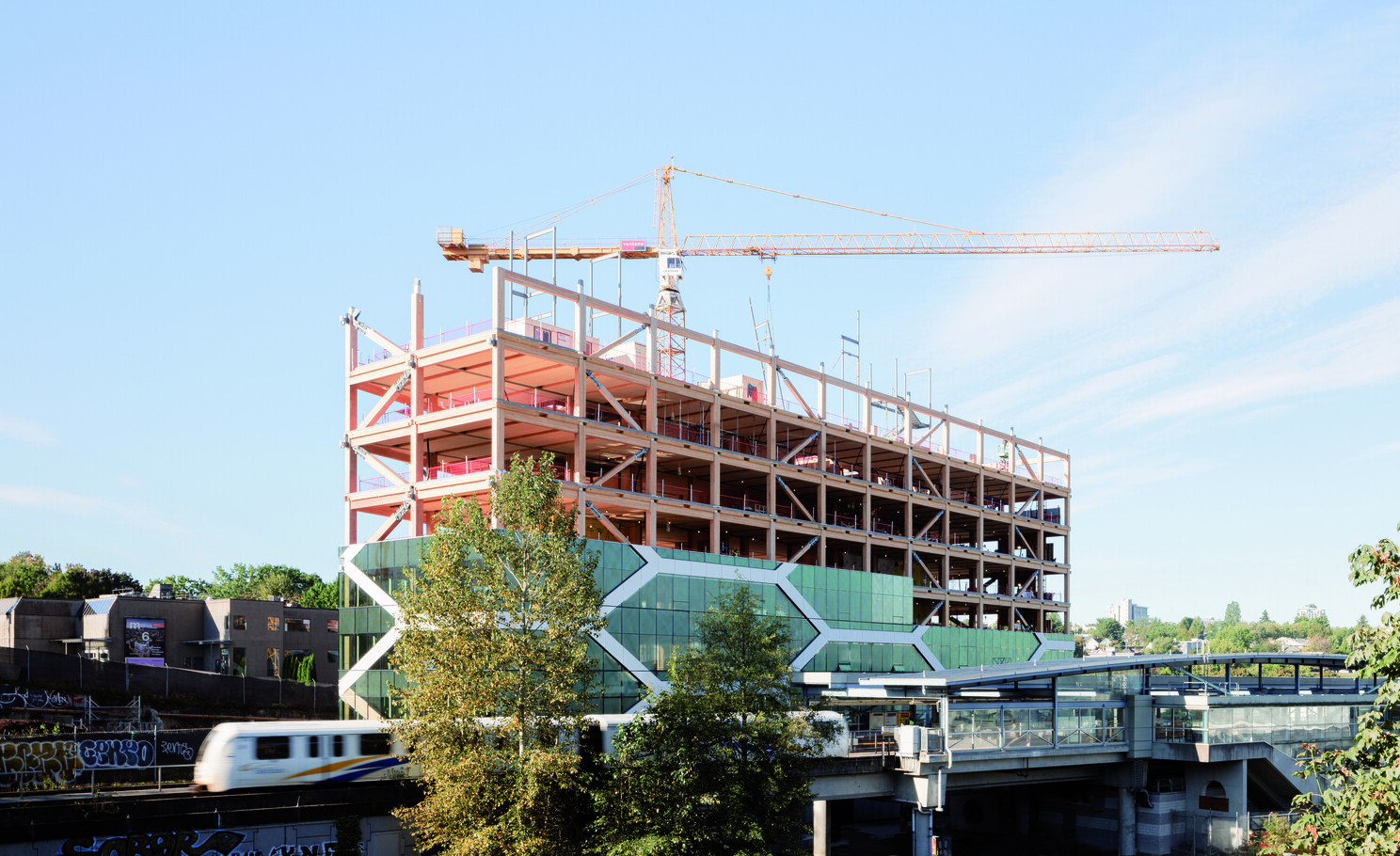
Learning from the Best: A Journey of Knowledge and Networking
Access to global expertise can accelerate innovation far beyond what’s possible in isolation. Ryan’s deliberate outreach to leaders in mass timber—through site visits, conferences, and direct conversations—provided a foundation of technical insight and professional relationships that shaped his approach to The Hive and beyond.
“I was amazed by the number of doors that opened, the people I met, and the meaningful connections I made.” These experiences not only expanded his technical repertoire but also embedded him in a community where ideas and lessons circulate freely. Ryan encourages peers to seek out these opportunities: “If you can do it, get out in the world and visit some timber projects.”
By immersing himself in the international mass timber community, Ryan gained a nuanced understanding of both the material’s potential and its limitations—knowledge that would inform his approach to hybrid systems and sustainability.
The Future of Mass Timber: Hybrid Approaches and Sustainability
As mass timber matures, the conversation is shifting from material purity to strategic integration. The next frontier lies in hybrid systems that combine timber, concrete, and steel, each deployed where it performs best.
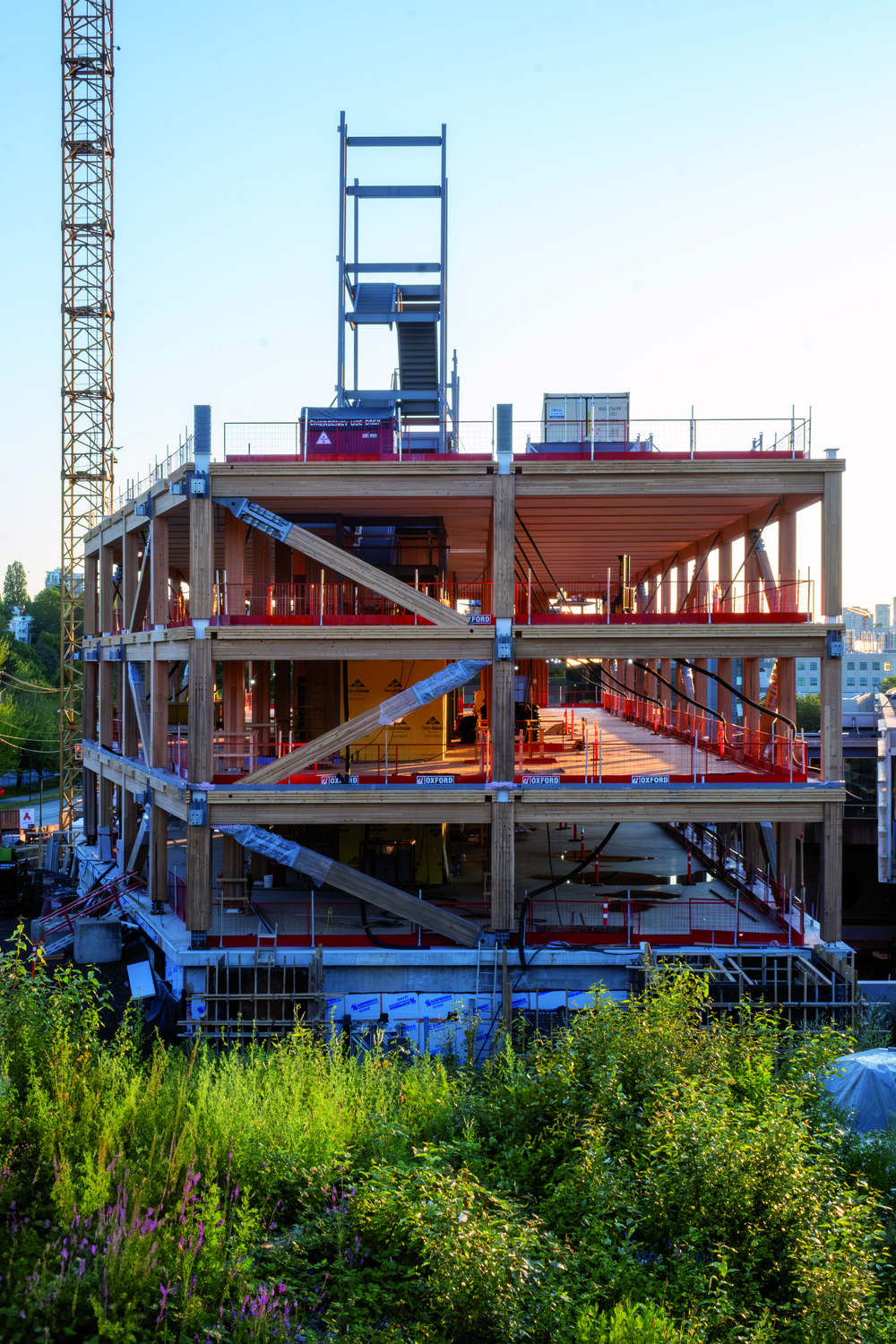
“We love timber and we want to use it in the right places and as much as possible.” This pragmatic philosophy underpins projects like the 19-story hybrid mass timber tower now underway in Vancouver, where timber’s strengths are complemented by other materials to achieve both performance and cost targets.
The adoption of life cycle analysis (LCA) as a design tool—not just a reporting requirement—enables teams to make evidence-based decisions about material selection and environmental impact. “I’m excited about this LCA process not as reporting but as a design tool to make good choices along the way,” Ryan explains, pointing to a future where sustainability is embedded in the earliest design moves, not appended at the end.
This evolution in practice is inseparable from the networks and communities that sustain it—a point Ryan returns to as he considers the broader movement.
Building Momentum: Community, Knowledge, and the Next Chapter
The rapid advancement of mass timber is not the result of isolated breakthroughs, but of a growing community committed to rigorous exchange and shared ambition. Ryan’s experience demonstrates that the most significant progress occurs when expertise is pooled and lessons are openly shared.
“If you’re curious about it, if you’re interested, you’re asking good questions. People love to talk about what they’re up to,” he observes, underscoring the accessibility of the mass timber community to those willing to engage.
As the industry moves toward more complex hybrid systems and deeper sustainability metrics, the need for robust professional networks and transparent dialogue will only intensify. The future of mass timber will be shaped not just by technical innovation, but by the willingness of practitioners to collaborate across disciplines and geographies.
In the end, The Hive stands as a case study in how seismic innovation, collaborative culture, and a commitment to sustainable hybrid systems can converge in a single project. The real measure of progress lies not in isolated achievements, but in the capacity of the field to continually integrate new knowledge, challenge assumptions, and build structures—and communities—that endure.
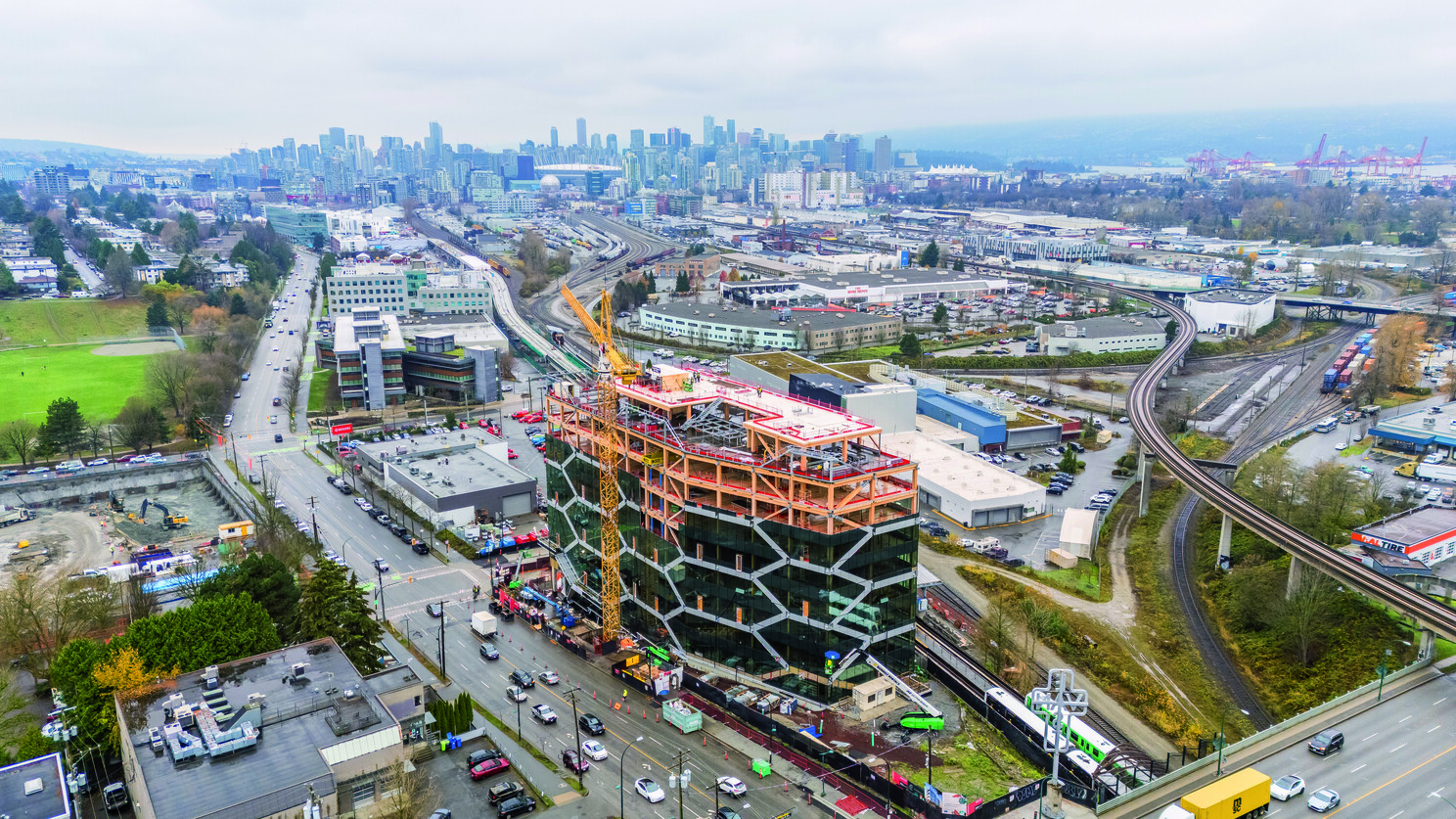
Frequently Asked Questions
How did The Hive’s structural system differ from typical North American mass timber projects? The Hive moved primary structural elements to the building’s perimeter, using a cellular exoskeleton and timber braced frame system rather than a conventional concrete core.
What strategies were used to address Vancouver’s seismic requirements with minimal concrete? The design team created a predominantly timber superstructure above level two, incorporating timber buckling restraint braces and shear walls to meet and exceed seismic performance standards.
How did collaboration influence the project’s technical and construction outcomes? A tightly integrated team of architects, engineers, and builders engaged in open communication and iterative problem-solving, enabling solutions to unique challenges like perimeter bracing and complex connections.
What role did international knowledge exchange play in shaping The Hive’s design approach? Ryan McClanaghan’s outreach to European mass timber experts through site visits and direct conversations provided technical insights and professional relationships that informed the project’s structural strategies and hybrid system integration.
How is sustainability addressed in The Hive and subsequent projects?The team uses life cycle analysis (LCA) as a design tool to guide material selection and environmental impact, and embraces hybrid systems that combine timber, concrete, and steel to optimize both performance and sustainability.
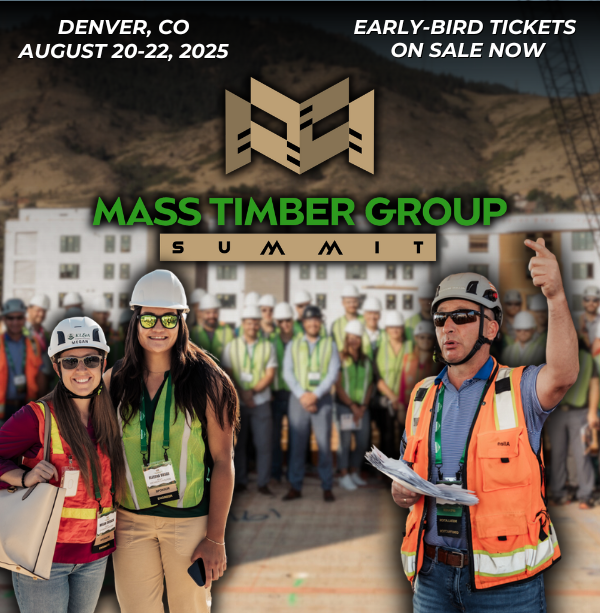
Tired of Mass Timber Challenges Derailing Your Projects? Learn How to De-Risk & Deliver Them.
Lead mass timber projects with confidence — and leave delays, redesigns, and budget blowups behind.
✅ Solve early-stage design, sourcing, insurance, permitting, code & cost hurdles before they derail your project.
✅ Find technical answers on design, detailing, procurement, embodied carbon ROI, hybrid systems & more.
✅ Build relationships with developers, GCs, architects, and engineers shaping mass timber’s future.
Get your ticket— and get the insights, skills, and network to deliver mass timber projects successfully.
Latest episodes
.png)
3 Months Faster, Lower Costs, Better Performance: The Case for Mass Timber Warehouses
What if the real breakthrough in industrial construction isn’t about carbon at all?
For decades, developers have tolerated persistent headaches—inefficient insulation, fire hazards, and inflexible layouts—accepting them as the cost of building with steel and concrete. But a new material is quietly rewriting those rules, not by chasing green credentials, but by addressing the design failures owners are most frustrated by.
As Kyle Freres puts it, “If you think the case for mass timber industrial buildings is just carbon, you’re missing the real opportunity.” This isn’t about making warehouses prettier or ticking a sustainability box. It’s about rethinking the fundamentals: faster builds, smarter grids, and structures that perform better for both people and the bottom line. The story of Freres Wood’s 58,000-square-foot mass timber warehouse isn’t just a case study—it signals that the industrial sector’s old assumptions are up for revision.

Rethinking Industrial Design: The Case for Mass Timber
When industrial buildings fall short of operational needs, the issue often runs deeper than material choice—it’s embedded in the logic of their design. As Kyle Freres, and John Bradford - Director of Engineering at Crow Engineering Inc., argue, mass timber is not simply a lower-carbon substitute for steel or concrete; it directly addresses the inefficiencies and inflexibilities of conventional industrial construction.
“If you think the case for mass timber industrial buildings is just carbon, you're missing the real opportunity,” Freres contends. This reframing moves the discussion beyond environmental metrics, prompting a closer look at how mass timber can resolve longstanding issues of speed, adaptability, and lifecycle performance in industrial projects.
By leveraging mass timber, project teams can achieve faster construction, greater design flexibility, and improved long-term value—outcomes that steel and concrete often struggle to deliver. As the industry confronts the constraints of legacy systems, mass timber offers a practical, systems-level alternative.
A Case Study in Material Disruption: Building a Mass Timber Warehouse
Few projects illustrate this shift as clearly as Freres Engineered Wood’s 58,000-square-foot mass timber warehouse, conceived not as a showcase, but as a proof of concept for the broader market. The facility’s performance and cost profile directly challenge the assumption that mass timber is a premium option reserved for signature projects.
“We wanted to provide a case study to demonstrate that it can be done,” Freres explains. The project’s financials revealed that mass timber can compete head-to-head with pre-engineered metal buildings and concrete tilt-ups, dispelling the notion that sustainability must come at a premium.
Most notable was the construction timeline: the team completed the structure three months faster than comparable projects. Freres notes, “We shaved three months off of this project.” In a sector where every week of delay carries real financial consequences, this acceleration is a decisive advantage.
This case study sets the stage for a deeper examination of the technical and regulatory hurdles that mass timber must clear to become a mainstream industrial solution.
Technical Hurdles and Hidden Advantages: Mass Timber’s Performance Profile
Concerns about fire safety, insulation, and structural reliability have long shaped the industrial sector’s material choices. Yet, mass timber’s performance in these domains is not only competitive—it often surpasses expectations.
“Our mass ply product has been tested for fire rating just like any other mass timber product,” Freres notes, citing successful two-hour fire rating tests. This level of protection directly addresses regulatory and insurance concerns, positioning mass timber as a robust alternative to steel and concrete.
Thermal performance is another area where mass timber distinguishes itself. Bradford points out, “If you have four inches or more in thickness on that panel wall, we can show that it meets the mass criterion for energy.” Unlike metal buildings, which often require complex insulation assemblies, mass timber panels inherently provide both structure and thermal mass, streamlining the envelope and reducing operational energy demands.
These technical attributes not only satisfy code requirements but also open new possibilities for industrial design—enabling simpler, more integrated building systems. As regulatory frameworks evolve, these advantages are likely to become even more pronounced.

Market Dynamics: Economic and Regulatory Pressures Favoring Mass Timber
Rising tariffs, volatile supply chains, and tightening sustainability mandates are converging to reshape material selection in industrial construction. For many developers, these pressures are no longer abstract—they are immediate constraints on project feasibility.
“People are looking local as a way to potentially hedge these tariff issues,” Freres observes. Sourcing mass timber domestically not only insulates projects from global price shocks but also aligns with emerging ESG requirements by reducing transportation emissions.
Bradford adds, “There’s been a lot of attention on residential and office applications, but industrial warehouses are built in much larger square footage each year.” This scale represents a significant opportunity: as industrial clients seek to decarbonize their portfolios, mass timber offers a credible path to both compliance and differentiation.
The interplay of economic and regulatory forces is accelerating the adoption of mass timber, but realizing its full potential requires a rethinking of project delivery and design collaboration.
Integrated Delivery: Collaboration as a Catalyst for Innovation
The Freres-Bradford partnership demonstrates that material innovation is inseparable from process innovation. Their approach—prioritizing simplicity, reducing waste, and streamlining assembly—translates directly into improved project outcomes.
“Can we really lean into mass timber? Can we trust in the process?” Freres recalls from early design meetings. The team’s commitment to minimizing the number of unique components and connections led to faster, more reliable construction.
Bradford elaborates, “We looked at different options of what we can do.” Through iterative engineering, they arrived at a post-and-beam system that balanced efficiency with structural rigor. This collaborative, systems-based approach is essential for unlocking the full value of mass timber—reducing risk, controlling costs, and delivering higher-performing buildings.
The lessons from this project extend beyond material choice, offering a template for integrated project delivery in a sector that has long been fragmented.
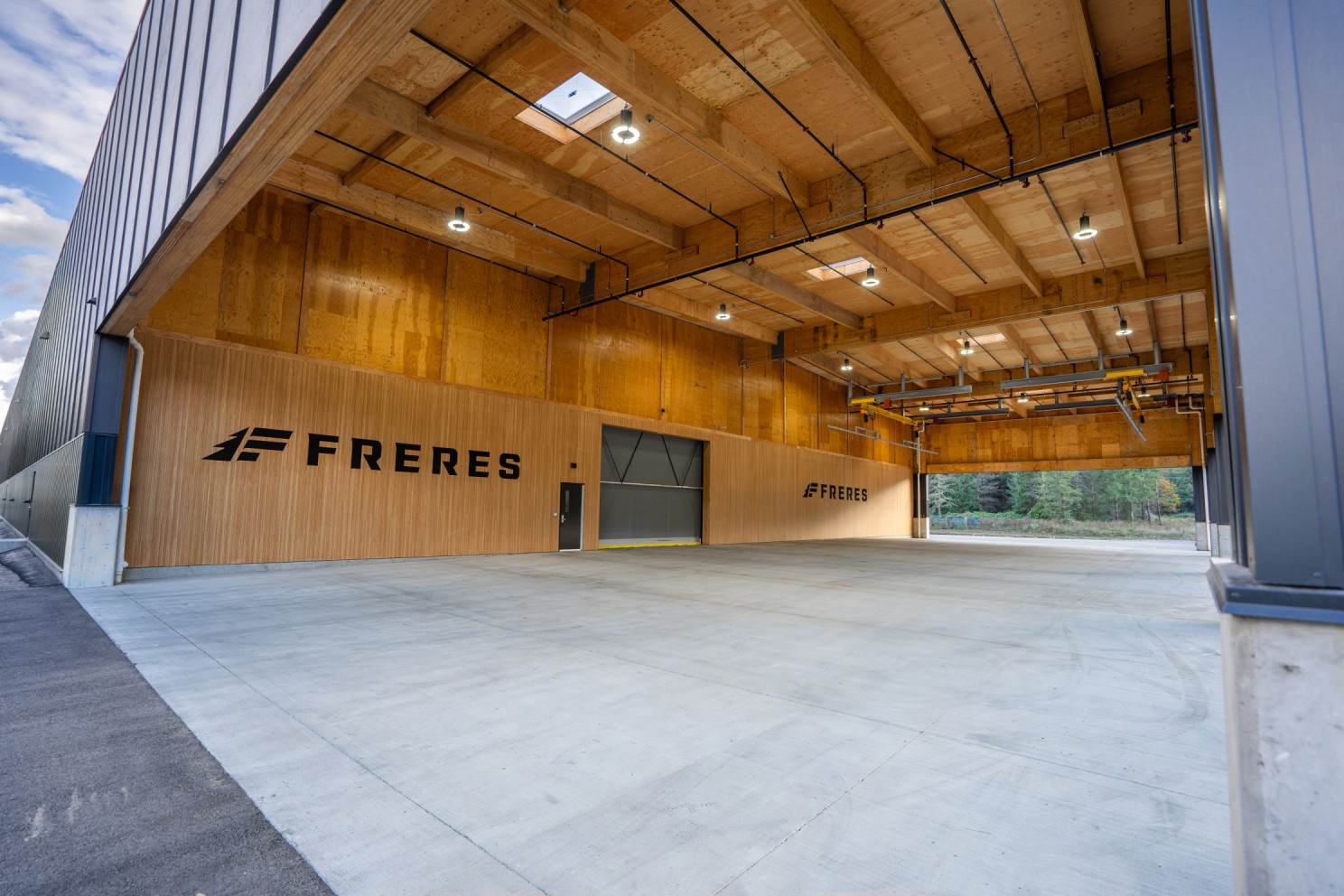
Beyond Structure: The Human and Spatial Impact of Mass Timber
While technical and economic factors often dominate the conversation, the experiential qualities of mass timber are impossible to ignore. The warehouse’s occupants and visitors consistently remark on the difference that natural materials and daylighting make in the industrial context.
Freres notes, “Every tour we have given of the warehouse, people walk through the door and gasp in astonishment.” The exposed timber, combined with generous glazing, transforms the warehouse from a utilitarian shell into a space that supports well-being and productivity.
This shift in atmosphere is not incidental—it is a direct result of design decisions enabled by mass timber. In an industry where worker retention and satisfaction are increasingly important, these qualitative benefits carry tangible value.
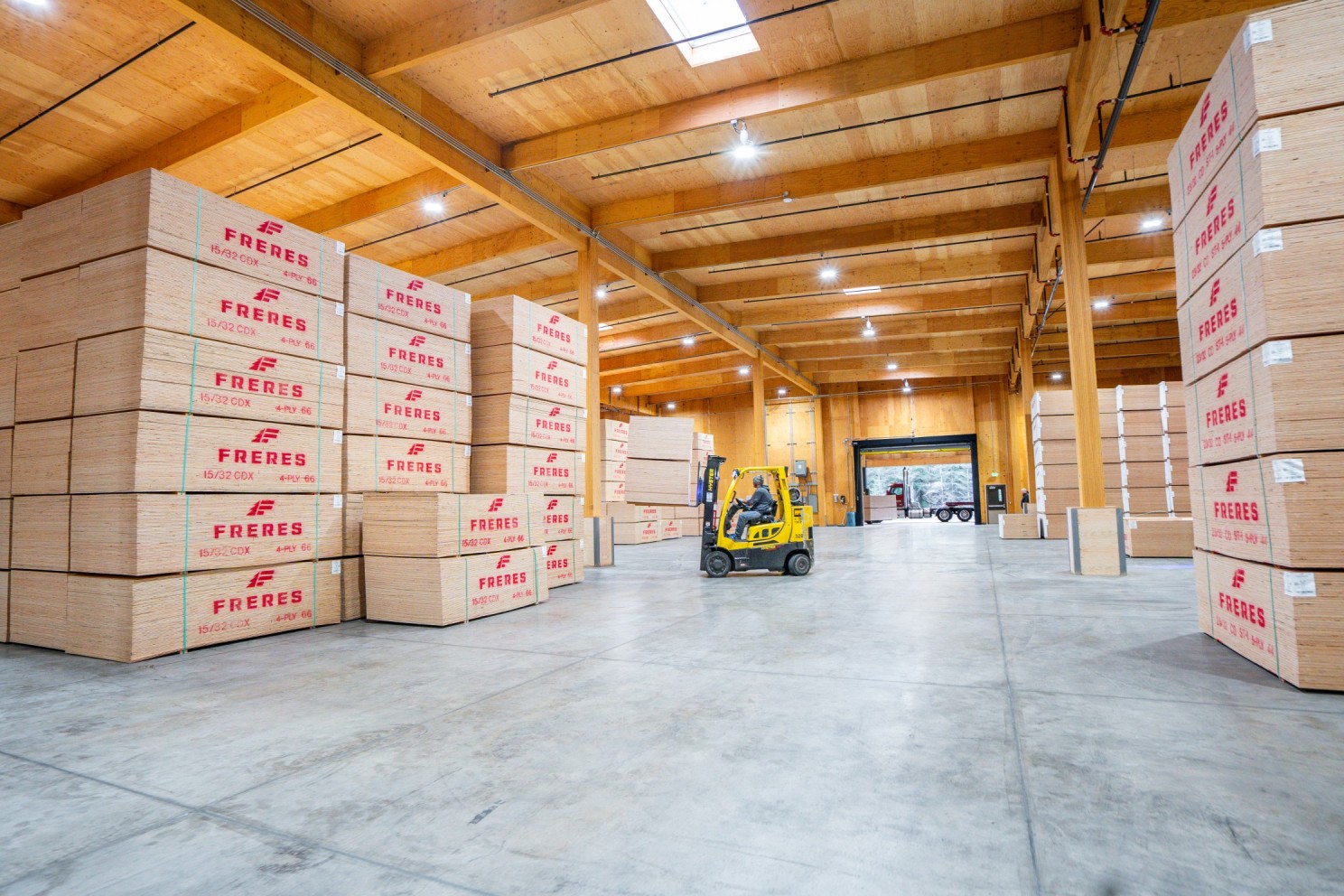
Environmental Accounting: Mass Timber’s Role in Sustainable Construction
The environmental case for mass timber extends from forest management to end-of-life scenarios. Freres and Bradford emphasize the importance of traceability and resource efficiency throughout the supply chain.
“We take the sustainability aspect of our product very seriously,” Freres asserts, describing a vertically integrated process that ensures responsible sourcing and manufacturing. The use of veneer in mass plywood panels achieves over 70% recovery from each log, maximizing material yield and minimizing waste.
This level of resource efficiency, combined with carbon sequestration in the finished product, positions mass timber as a credible solution for developers facing stringent ESG criteria. The ability to document and verify these impacts is increasingly a prerequisite for participation in major projects.
As regulatory and market expectations continue to evolve, the environmental performance of mass timber will only become more central to its adoption.
Conclusion: Toward a New Industrial Paradigm
The trajectory of mass timber in industrial construction is not defined by novelty, but by its capacity to resolve persistent tensions—between speed and quality, cost and sustainability, efficiency and experience. The Freres warehouse project demonstrates that when technical rigor, collaborative delivery, and environmental stewardship converge, mass timber is not an outlier but a logical next step.
For architects, engineers, and builders, the challenge is no longer whether mass timber can compete, but how to integrate its unique properties into the next generation of industrial spaces. The path forward is not about following trends, but about recalibrating the fundamentals of industrial design to meet the demands of a changing market and a changing planet.
Frequently Asked Questions
How did the construction timeline for the Freres mass timber warehouse compare to conventional industrial projects? The team delivered the mass timber warehouse three months ahead of comparable steel or concrete projects, offering a notable schedule advantage.
What specific fire safety benchmarks did the mass timber system achieve in this project? The mass ply product used in the warehouse was tested and achieved a two-hour fire rating, meeting key regulatory and insurance requirements.
How did mass timber impact the building’s thermal performance and envelope design? With panel walls four inches or thicker, the mass timber system met the mass criterion for energy, allowing for a streamlined envelope and reducing the need for complex insulation.
What procurement or supply chain advantages were realized by sourcing mass timber domestically? Sourcing mass timber locally helped shield the project from global tariff volatility and supported compliance with ESG requirements by reducing transportation emissions.
How did the design and assembly process differ from traditional industrial construction methods? The project team minimized unique components and connections, using a post-and-beam system that enabled faster, more reliable assembly and reduced construction risk.
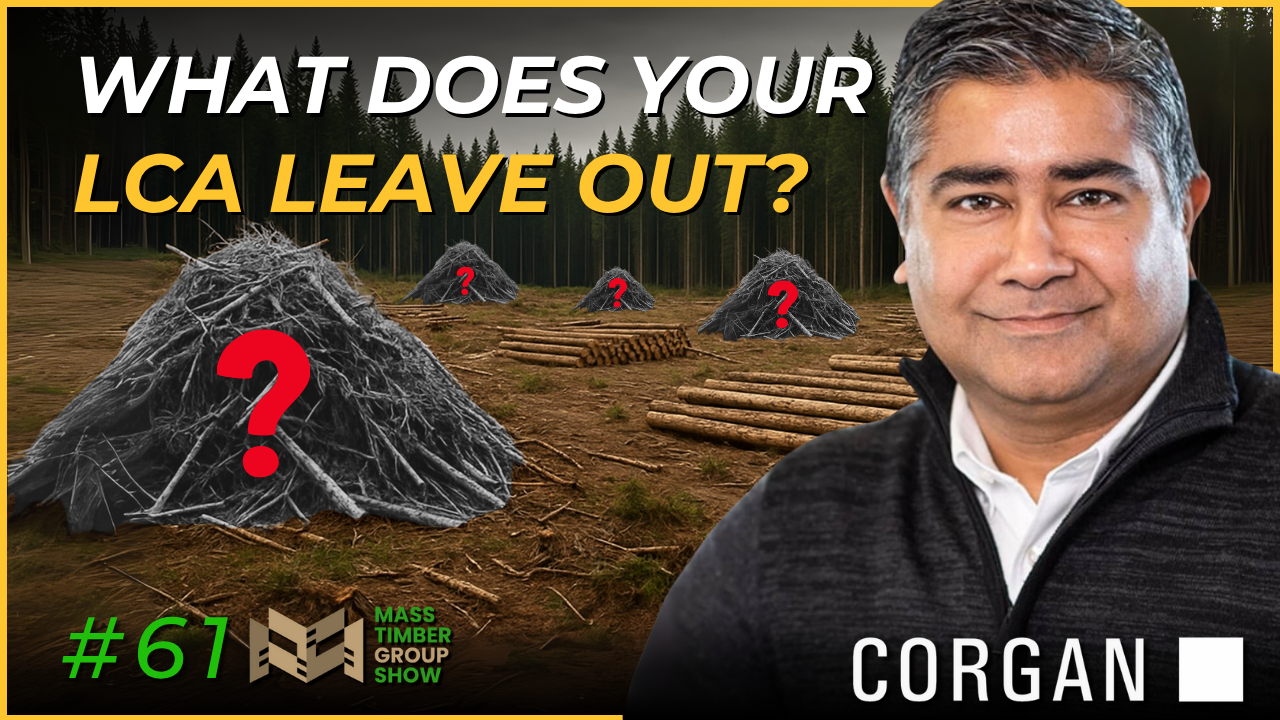
The Mass Timber Carbon Gap No One Talks About
What if the celebrated sustainability of your mass timber project is built on an incomplete carbon ledger? If you’re in a rush to use mass timber purely as a climate solution, you could be overlooking a critical detail: only about 35% of a harvested tree ends up in the building. The rest—bark, branches, roots—rarely factors into standard carbon accounting, even though its fate can dramatically alter a project’s true environmental impact. So, how do you get the whole picture?
As Varun Kohli puts it, “that [material is] rarely tracked in typical LCA models. But that carbon matters.” For architects, engineers, and developers committed to rigorous sustainability, understanding where biogenic carbon hides—and how to account for it—has become a new frontier in responsible design.
Carbon & Mass Timber
Did you know that most LCAs for mass timber often omit a substantial portion of the carbon emissions? While mass timber is widely celebrated for its environmental benefits, only about 35% of each harvested tree ends up in structural use; the rest—bark, branches, and roots—typically escapes both construction and carbon accounting. This can lead to a misunderstanding of the true carbon accounting of mass timber projects.
Varun Kohli, Director of Sustainability at Corgan, underscores the significance of this gap: “It’s often left behind or burned, releasing carbon that’s rarely tracked in typical LCA models. But that carbon matters.” For practitioners committed to rigorous sustainability, perhaps a more comprehensive approach is needed.
Why is carbon accounting for mass timber in the spotlight?
A single report from the World Resources Institute (WRI) set off a chain reaction within the sustainability community, exposing blind spots in conventional mass timber embodied carbon calculations.
Kohli recalls, “That report basically pointed out the fact that our industry might have been ignoring a portion of the embodied carbon or carbon emissions calculations, mostly associated with the forestry practices.” This realization shifted the Corgan Team’s focus toward slash management—the fate of the non-structural parts of the tree—and its substantial role in a project’s carbon profile. By scrutinizing these overlooked emissions, the team identified a critical variable that can account for up to a quarter of a tree’s total carbon.
The Birth of the Mass Timber Carbon Calculator
Recognizing the need for actionable data, Corgan’s research evolved from a white paper into a practical digital tool: the Mass Timber Carbon Calculator. This resource enables design teams to quantify the biogenic carbon impact of their projects with far greater specificity, incorporating variables such as building size, wood species, and transportation distances.
Kohli explains, “You can pick the size of your building, the square footage, the number of floors, and tell the tool whether you’re using both beams and columns or just one component.” This granularity allows users to see how each design decision influences the project’s carbon footprint.
The calculator transforms carbon accounting from a static report into an interactive design parameter, supporting more informed material sourcing and project planning. By making carbon impacts visible early in the process, it encourages teams to weigh environmental consequences alongside structural and economic considerations.
Understanding Slash Management Practices
The carbon fate of mass timber hinges not just on what is built, but on what is left behind. Slash management—whether through burning, masticating, or leaving material to decompose—directly affects the amount and timing of carbon released back into the atmosphere.
Kohli notes, “Up to 25% of a tree’s carbon is tied to how its leftover parts are handled.” For example, burning slash results in immediate carbon emissions, while leaving it on the forest floor can allow for partial sequestration or slower release. This nuance is often absent from standard LCA models, yet it is pivotal for teams seeking to minimize embodied carbon.
By integrating slash management scenarios into the calculator, the tool equips architects and engineers to ask more pointed questions of their suppliers and to specify timber with a clearer understanding of its full carbon story.
A Win-Win Proposition: Sustainability Meets Cost Efficiency
The implications of the calculator extend beyond environmental stewardship; they also intersect with project economics. By visualizing the impacts of sourcing decisions—things like slash management practices, carbon metrics, and even transportation distances—teams can identify opportunities for both emissions reduction and budget optimization.
Kohli observes, “If you’re transporting it closer to where the project is, you might also be saving cost.” The tool’s ability to map sourcing options against both carbon and other metrics enables a more holistic evaluation of project trade-offs. This dual lens strengthens the business case for sustainable choices, aligning environmental and economic objectives in project delivery.
Designing for the Future
The development and deployment of the Mass Timber Carbon Calculator highlight the necessity of industry-wide collaboration. Kohli stresses, “We’re trying to make it so visual and easy for you to assess that from day one when you’re thinking about mass timber.” By making the tool open and inviting feedback, Corgan aims to foster a shared platform for advancing best practices.
“We’re honest that we share what we know. At the end of the day, I still want to go back to my original thought of integrating sustainability and design.” This openness is not just a matter of transparency; it is a strategy for accelerating collective progress. Continuous refinement, informed by real-world use and peer input, is essential for keeping pace with the evolving demands of sustainable design.
The Future of the Carbon Calculator and Industry Standards
With regulatory frameworks tightening around embodied carbon, tools like the Mass Timber Carbon Calculator are becoming indispensable for compliance and leadership alike. Kohli notes, “We’re hearing about that coming in New York. The UK is gearing up towards something like that as well.” The tool’s adaptability positions it to support teams as standards shift and expectations rise.
Future iterations are already in development, aiming to expand the calculator’s capabilities and further embed sustainability into the design workflow. Kohli cautions, “If you don’t put your first foot forward correctly, then you’re just kind of fixing that right along the design process.” Early, accurate carbon accounting is no longer optional—it is foundational.
The Mass Timber Carbon Calculator marks a shift from aspirational sustainability to accountable practice. By illuminating the full carbon cycle of mass timber, it enables the industry to move beyond partial narratives and toward genuinely responsible building. As the sector confronts the realities of climate impact, such tools will be central to reconciling design ambition with environmental necessity.
Frequently Asked Questions (FAQs)
- How does the Mass Timber Carbon Calculator differ from standard LCA tools currently used in the industry? The calculator uniquely incorporates emissions from slash management—the fate of non-structural tree parts—offering a more complete picture of biogenic carbon than most LCA models, which often overlook these factors.
- What specific variables can users adjust within the Mass Timber Carbon Calculator to reflect their project conditions? Users can input building size, square footage, number of floors, wood species, transportation distances, and specify which timber components (beams, columns, or both) are being used.
- Why is slash management considered a critical variable in mass timber’s carbon profile? How leftover materials like bark, branches, and roots are handled after harvest can determine up to 25% of a tree’s total carbon impact, directly influencing the amount and timing of carbon released.
- How does the calculator help teams balance sustainability goals with project costs? By mapping both carbon and other impacts of sourcing decisions—such as transportation distances—the tool helps teams identify options that can reduce emissions and potentially lower expenses.
- What approach is Corgan taking to ensure the calculator remains relevant as industry standards evolve? Corgan is keeping the tool open to feedback and ongoing improvement, allowing it to adapt as new regulatory requirements and best practices emerge.
.png)
What Is Mass Timber & Why It Matters | Wood Replacing Concrete Explained
What is mass timber, and why is it gaining traction in construction?
In this video, Victor walks you through the exciting rise of mass timber – from engineered wood products like CLT and glulam to full‑scale multi‑story buildings. Learn how mass timber:
- Offers 4–5× the strength-to-weight ratio of concrete
- Enables faster, Lego-style offsite construction (18-story Brock Commons built in just 70 days!)
- Provides natural fire safety through char-layer protection
- Reduces carbon footprints by storing CO₂ and cutting embodied emissions
Whether you're curious about eco-friendly skyscrapers, modern architecture, or climate solutions, this beginner-friendly guide explains everything in plain terms.
What you’ll learn:
• The basic definition of mass timber (CLT, glulam, etc.)
• Strength, seismic, and fire benefits over concrete
• Case studies like Brock Commons and UBC Forestry Building
• Health + well-being perks: stress reduction with wood interiors
• Tips on building with mass timber — resources from the Mass Timber Group

Acoustic Design in Mass Timber: What Every Architect and Engineer Should Know
Client satisfaction in mass timber projects often comes down to what you don’t hear.
Acoustics are one of the top post-occupancy complaints in buildings, especially when exposed systems amplify the problem. And with mass timber - this can’t be ignored.
In mass timber buildings, acoustics are often overlooked until it’s too late - when the client is frustrated, complaints start piling up, and your team is asked to explain why a premium building sounds like a budget one.
The irony? The very things that make mass timber so desirable, its sustainability, openness, and exposed finishes, also make it harder to control noise.
This isn’t just a minor inconvenience, it’s a design liability.
“What you don’t want is to be hearing everything going on outside your walls,” says Aedan Callaghan with Pliteq.
And neither do your clients. Solving for sound requires remembering, and maybe a bit of rethinking, of the fundamentals - all without compromising the architectural or environmental intent that brought you to mass timber in the first place.

Breaking Down the Basics: Airborne vs. Structure-Borne Sound
Not all noise is created equal - distinguishing between its sources is fundamental to effective acoustic design. Callaghan clarifies the two principal categories: airborne sound, such as voices or music, and structure-borne sound, like footsteps or mechanical vibrations.
Airborne sound is quantified by the Sound Transmission Class (STC), a number rating that reflects a wall assembly’s ability to block noise passing through the air. Structure-borne sound is measured by the Impact Insulation Class (IIC), which gauges how well a floor or ceiling assembly dampens impact-generated vibrations.
“The higher the [STC or IIC] rating, the better job it does at preventing you from hearing that type of noise,” Callaghan explains.
Recognizing these distinctions is the first step toward specifying assemblies that genuinely improve acoustic comfort.
The Unique Acoustic Behavior of Mass Timber
The drive for exposed timber aesthetics introduces a paradox: the very qualities that make mass timber appealing can compromise its acoustic performance. Unlike concrete, mass timber’s lower density and the frequent omission of suspended ceilings create new transmission paths for sound.
“Ironically in mass timber, the mass isn't actually all that high… about one-fifth the weight of the same thickness concrete,” says Callaghan.
Traditional assemblies rely on suspended ceilings as acoustic buffers. In mass timber, with its exposed CLT ceilings, designers must rethink their approach—and build quiet from the top down.
Practical Acoustic Solutions for Mass Timber Projects
Solving for Sound, Layer by Layer
To deliver acoustic performance that lives up to design expectations, project teams must approach mass timber differently.
Here are four key areas of focus:
1. Floor Systems: Building Quiet from the Top Down In mass timber construction, exposed CLT ceilings are part of the appeal—but they come at an acoustic cost. Unlike traditional wood or steel systems, which often include a suspended ceiling cavity to house resilient channels or insulation, exposed timber ceilings eliminate that layer entirely. That means the burden of acoustic performance shifts upward—to the floor assembly above.
This challenge is compounded by mass timber’s relatively low density compared to concrete. Without the mass or the decoupling benefits of a dropped ceiling, structure-borne impact sounds (like footsteps, dropped items, or appliance vibrations) can easily travel from floor to floor unless the system above is properly engineered.
The fix? You need to introduce mass and isolation above the CLT, and do it in a way that doesn’t undermine the benefits of timber construction—namely speed, sustainability, and moisture sensitivity. A few widely used strategies include:
- Acoustic mats that isolate the finish floor or topping layer from the CLT substrate.
- Topping layers that add mass, like traditional concrete, lightweight Gypcrete, or newer dry solutions like compressed gypsum fiber board.
- Floating floors or decoupled subfloor assemblies that minimize direct mechanical connection to the CLT.
Aidan Callaghan recommends a composite dry system, combining isolation and mass without the downsides of wet trades:
- GenieMat FF – a post-consumer recycled rubber isolation underlayment laid directly over CLT to absorb vibration and prevent transmission.
- GenieBoard – a dry, high-density recycled gypsum fiber board that adds acoustic mass without introducing water into the building envelope.
“You’re trying to keep the timber as dry as possible. GenieBoard gets rid of the cure time and moisture challenges—and still meets code,” Callaghan says.
In side-by-side performance testing, this dry system matched traditional 2" concrete topping assemblies in acoustic performance while offering major construction benefits:
- Eliminated wet trades and cure time
- Reduced floor weight by 10 psf
- Enabled thinner foundations and CFS wall framing
- Shortened schedules by 7–10 days
2. Wall Assemblies: Separate to Isolate
When it comes to blocking airborne noise—voices, music, or television—wall assemblies are your primary line of defense. But not all walls are created equal. Standard single-stud assemblies with drywall on both sides typically fall short, allowing sound vibrations to travel through the rigid connections between materials.
The result? Code minimum STC ratings—and clients who hear far more than they should.
To improve isolation, the key is to introduce separation within the wall structure, either by decoupling layers or adding mass and damping between them. The most effective solution in high-performance multifamily and commercial projects is the double stud wall: two parallel stud walls with a 1" air gap between them and drywall applied to each outer face.
“When the sound gets into that first wall, there's an air gap preventing it from getting into that second wall,” explains Callahan.
This configuration minimizes rigid connections across the wall, allowing it to achieve STC ratings of 60–63—often enough to meet or exceed expectations for luxury residential, hospitality, and institutional settings.
For projects where space is at a premium and thicker wall assemblies aren’t viable, alternatives like resilient isolation clips (e.g., GenieClips) can decouple one side of the drywall from the framing without sacrificing square footage. These clips absorb and damp vibration, reducing the transfer of airborne sound while preserving the wall’s footprint.
No matter which path you choose—wider assemblies or resilient mounting hardware—the principle remains the same: disconnect the structure to block the sound.
3. Flanking: The Silent Saboteur
You can specify the highest-performing wall and floor assemblies on paper—but if flanking isn’t addressed, the sound will find another way in.
Flanking paths are indirect routes that sound takes around acoustic separations. In mass timber buildings, the most common culprit is the continuous CLT structure—a beautiful, solid surface that also acts as a bridge for vibration. Sound can travel over, under, or around rated walls via uninterrupted timber panels, undermining even the best acoustic assemblies.
Think of it like water slipping through the cracks—except in this case, the cracks are the architectural connections between timber elements.
Callahan emphasizes that flanking can completely undermine the performance of even top-tier assemblies, making them ineffective in real-world conditions if not addressed holistically. That’s why it’s critical to design with flanking in mind -not after the fact, but as part of the core acoustic strategy.
Several best-practice approaches include:
- Interrupting CLT panels at unit boundaries, where possible
- Using spline joints or acoustic gaskets to reduce sound transfer
- Designing bulkheads or dropped soffits at transition zones
- Alternating ceiling treatments (e.g., exposed vs. acoustic finishes) between adjoining spaces
- Performing detailed junction reviews with your acoustic consultant and timber fabricator
“If you've ignored flanking, you're not actually getting what you paid for with that upgraded assembly,” warns Callahan.
The fix isn't always complicated but it must be deliberate. Addressing flanking is about ensuring the building performs as designed, especially in exposed systems where structural continuity is visually celebrated but acoustically risky.
4. When to Act: Earlier Is Quieter Timing matters. Callahan recommends engaging acoustic teams no later than early design development (DD) to ensure integration of acoustic strategy into structural and architectural design. Late-stage fixes are costlier and often less effective.
The Importance of Considering Acoustics Early
Acoustics can't be value-engineered in after the fact. Callahan emphasizes the importance of bringing on acoustic consultants during design development (DD):
“The earlier that you can bring all these decisions forward, the better it is for the project as a whole.”
Early coordination allows for optimized junction details, accurate acoustic targets, and the ability to realize whole-building efficiencies like lighter foundations and thinner floor plates.
Case in Point: Multi-Family Building in New York
In a recent mass timber project in New York, Pliteq’s dry system replaced a conventional concrete topping with:
- 10 psf weight savings
- 2" less rebar and slab thickness
- 16% less cold-formed steel (CFS) wall material
- Acoustic performance equal to traditional assemblies
- Construction schedule shortened by 7–10 days
Despite a slightly higher installed cost for the GenieBoard system (~$1–2/sf), the overall project cost came out lower—thanks to structural and scheduling efficiencies unlocked by the lighter, dry floor assembly.
Conclusion
Acoustic design in mass timber construction is no longer a fringe concern. It’s a core pillar of performance, occupant satisfaction, and project success.
From floor isolation mats and dry subfloors to flanking mitigation and early consultant engagement, the path to quieter mass timber buildings is paved with proven, practical solutions. And with recycled materials like GenieBoard and GenieMat FF, those solutions don’t have to come at the cost of sustainability.
As Callaghan puts it: “We’re using end-of-life materials to stop you from hearing the guy upstairs snoring.”
That’s acoustic performance with a conscience.
Frequently Asked Questions
- How do airborne and structure-borne sound differ in mass timber buildings, and how are they measured? Airborne sound (like voices or music) is measured by Sound Transmission Class (STC), while structure-borne sound (like footsteps or vibrations) is measured by Impact Insulation Class (IIC). Mass timber’s lower density and lack of drop ceilings make these harder to control.
- What specific wall assembly is recommended for improved acoustic separation? A double stud wall with a 1" air gap can achieve STC 60–63. For tighter spaces, resilient isolation clips like GenieClips can help decouple drywall while maintaining acoustic performance.
- Why are traditional concrete toppings often replaced in mass timber buildings? Concrete introduces moisture and weight. Dry systems using GenieBoard avoid both while matching performance, saving time, and reducing foundation and framing loads.
- How does the absence of ceilings impact sound performance in mass timber? With no suspended ceilings to absorb or block noise, floor assemblies above must do all the work, making floor design critical for both airborne and impact sound.
- What’s the best time to bring in acoustic expertise? Early design development (DD). Waiting until construction begins limits options and costs more. Early decisions enable flanking control, optimized assemblies, and potential structural savings.